连续累计自动衡器(电子皮带秤)检测的重要性
连续累计自动衡器(电子皮带秤)是工业生产中用于物料连续称重和累计计量的关键设备,广泛应用于矿山、冶金、化工、水泥、粮食等领域。其核心功能是实时监测输送皮带上的物料重量,并通过自动化系统实现精准计量。然而,由于长期运行、环境因素(如温度、湿度、粉尘)以及机械磨损的影响,电子皮带秤的精度和稳定性可能逐渐下降,导致生产数据失真甚至经济损失。因此,定期对电子皮带秤进行系统性检测和校准,不仅是保障企业生产效率和质量的关键措施,也是满足行业标准与法规要求的必要环节。
电子皮带秤检测的必要性
电子皮带秤的检测目标在于验证其计量准确性和运行可靠性。具体而言,检测工作能够: 1. **确保计量精度**:防止因误差累积导致生产原料或成品计量偏差,影响成本核算或产品质量; 2. **满足合规要求**:符合国家《自动衡器检定规程》(JJG 195)及相关行业标准; 3. **延长设备寿命**:通过早期发现机械部件异常(如皮带磨损、传感器故障),避免设备突发停机; 4. **优化生产效率**:减少因计量错误引发的生产流程中断或返工。
核心检测项目与技术要求
1. 静态精度测试
在静止状态下,使用标准砝码对电子皮带秤的称重单元进行校准,验证其静态称量误差是否在允许范围内(通常要求≤±0.1%)。测试需涵盖全量程范围,包括空载、半载和满载状态。
2. 动态累计误差检测
通过模拟实际物料流动,连续运行皮带秤并记录累计重量,与预设标准值对比计算动态误差。动态精度需满足≤±0.5%的要求,高精度场合可提升至≤±0.25%。
3. 皮带张力与跑偏检查
检测皮带张力的均匀性及跑偏程度。张力不均或跑偏会导致物料分布异常,显著影响称重结果。通常采用张力测试仪和视觉观察法进行综合评估。
4. 速度传感器校准
速度传感器是计算物料流量的关键组件。需通过标准转速发生器或编码器验证其输出信号的准确性,确保皮带速度与实际值一致。
5. 零点漂移测试
在空载状态下连续运行皮带秤,监测零点输出值的波动。零点漂移量超过阈值(如±0.05%满量程)时,需排查传感器故障或机械结构松动问题。
6. 载荷线性度检测
通过分段加载不同质量的砝码,绘制称重传感器的输入-输出特性曲线,分析线性度误差是否符合技术规范(通常≤±0.2%)。
7. 环境适应性测试
评估设备在极端温度、湿度或振动条件下的稳定性。例如,高温可能导致传感器信号漂移,需通过温控试验箱模拟实际工况。
8. 报警与保护功能验证
检查超载、断带、电源异常等故障的自动报警功能是否正常,确保设备具备安全保护机制。
检测方法与技术手段
电子皮带秤的检测需结合现场测试与实验室分析: - **现场检测**:使用移动式砝码小车、标准链码或循环链码模拟物料流量,实时采集数据; - **实验室校准**:对关键传感器(如荷重传感器、速度编码器)进行高精度标定; - **自动化测试系统**:通过工业计算机与专用软件实现数据采集、误差分析和报告生成,提高检测效率。
常见问题与改进措施
检测中常见问题包括传感器信号干扰、皮带打滑、机械结构变形等。针对这些问题,可采取以下措施: - **传感器屏蔽**:加装电磁屏蔽装置,降低外部干扰; - **皮带张力调整**:定期维护张紧装置,确保皮带运行平稳; - **抗腐蚀设计**:在潮湿或腐蚀性环境中选用不锈钢材质部件。
维护与周期性检测建议
企业应建立电子皮带秤的日常维护制度,包括: - 每日检查皮带跑偏情况; - 每月进行零点校准; - 每季度开展动态精度测试; - 每年委托第三方机构进行全面检定。
总结
电子皮带秤的检测是保障其长期稳定运行的核心环节。通过科学的检测项目设置、严格的误差控制标准以及规范的维护流程,企业可显著提升生产数据的可靠性,降低运营风险,同时满足行业合规要求。随着物联网和人工智能技术的应用,未来电子皮带秤的检测将更加智能化,实现实时监控与预测性维护的深度融合。
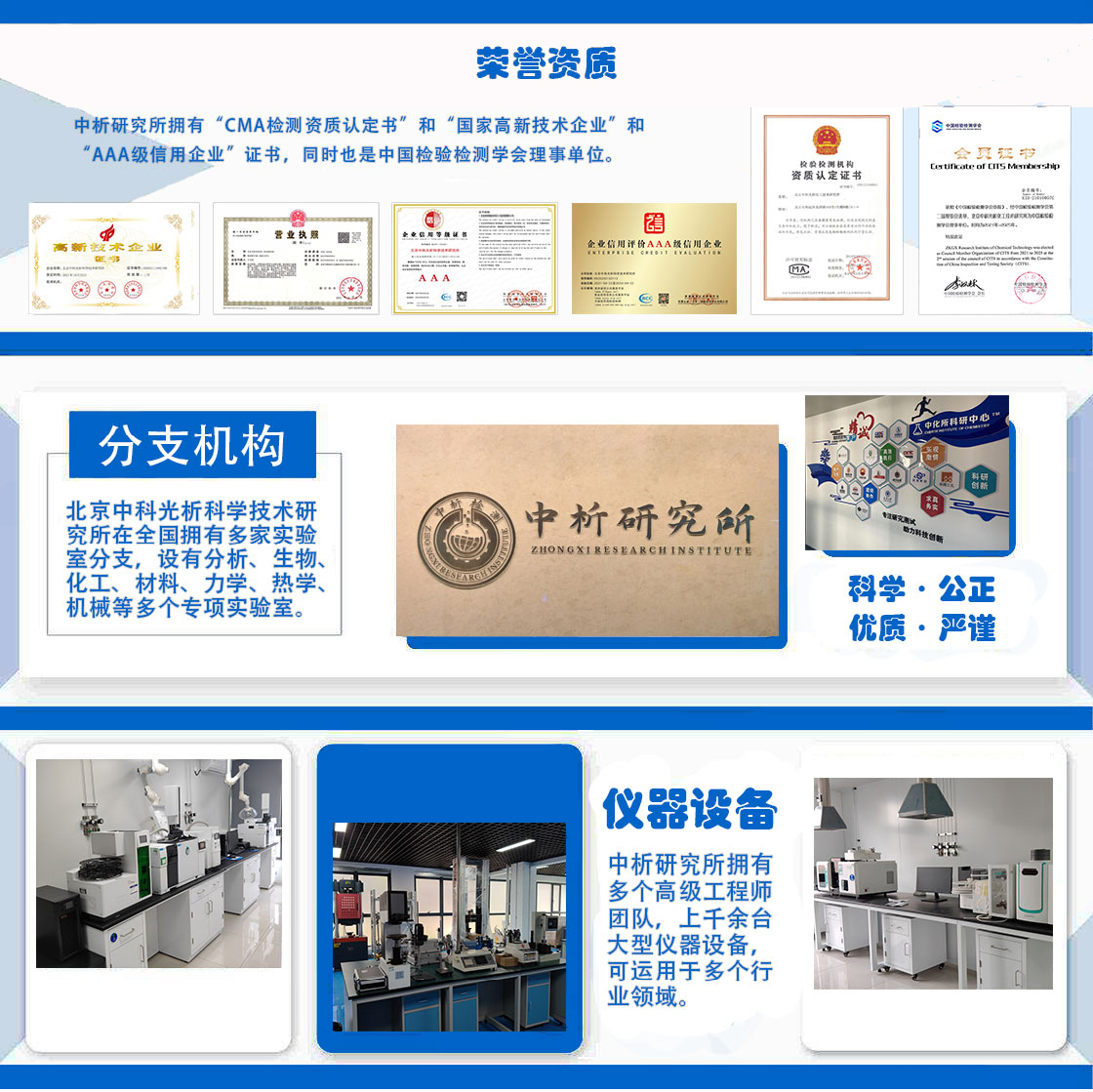
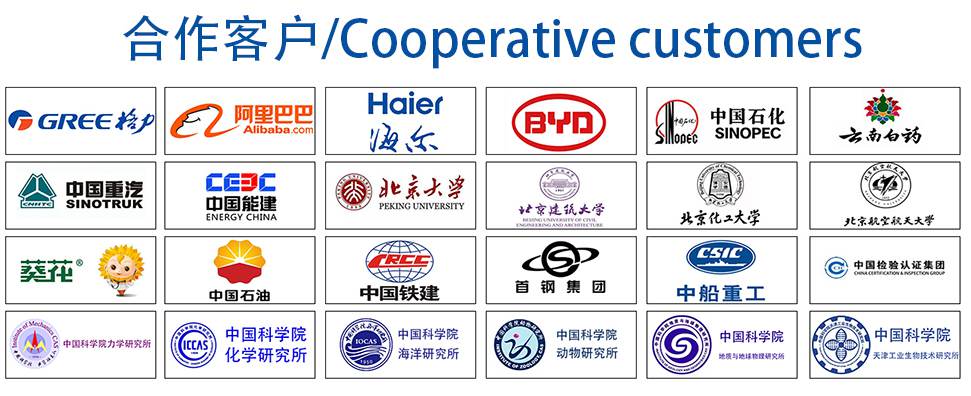