绝缘胶粘带检测的重要性及核心内容
绝缘胶粘带作为电气工程、电子设备制造及电力系统维护中的关键材料,其性能直接关系到用电安全和设备稳定性。这类胶粘带主要用于导线绝缘包扎、电缆接头密封、元器件固定等场景,需在高温、潮湿、化学腐蚀等复杂环境中保持优异性能。因此,通过科学规范的检测手段对其物理特性、电气性能及耐久性进行全面评估,是确保其符合国家标准(如GB/T 5013、IEC 60454等)和行业应用需求的核心手段。检测结果不仅影响产品质量控制,更是避免因绝缘失效引发短路、漏电甚至火灾事故的重要保障。
绝缘胶粘带检测的核心项目
1. 物理性能检测
包括厚度均匀性、拉伸强度、伸长率、剥离强度及粘接力测试。通过万能材料试验机测量胶带在拉伸状态下的断裂强度和形变率,验证其机械耐用性;使用剥离试验机评估胶带与被粘物间的结合力,确保长期使用中不脱胶。例如,汽车线束用胶粘带通常要求剥离强度≥1.5N/mm。
2. 电气性能检测
重点检测介电强度(击穿电压)、体积电阻率和耐电压性能。采用高压测试仪在标准温湿度条件下(如23℃±2℃,50%±5%RH)进行击穿试验,验证胶带在额定电压下的绝缘可靠性。光伏用胶粘带常要求击穿电压≥6kV/mm,体积电阻率需达到10^12Ω·cm级别。
3. 环境耐受性检测
包含高温老化(如150℃×168h)、低温脆性(-40℃×24h)、湿热循环(85℃/85%RH)、紫外线加速老化等测试。模拟极端气候条件后的性能保留率需≥80%,同时观察是否出现开裂、粉化或脱胶现象。例如,户外变压器用胶粘带需通过2000小时盐雾试验。
4. 化学兼容性检测
测试胶带对变压器油、酸碱溶液、有机溶剂的耐受能力。通过浸泡试验(如ASTM D543)后评估外观变化及性能衰减,确保在化工环境中不发生溶胀或降解。船用电气胶粘带需满足72h耐海水浸泡要求。
5. 环保与安全指标检测
依据RoHS、REACH等法规检测重金属(铅、镉等)、多环芳烃(PAHs)、卤素含量,同时评估燃烧特性(UL94阻燃等级)。动力电池用胶粘带需达到V-0级阻燃且卤素含量≤900ppm。
检测技术发展趋势
随着新能源、5G等领域对绝缘材料要求的提升,检测项目正向智能化、精细化发展。例如引入红外光谱(FTIR)分析胶粘剂成分一致性,采用热重分析仪(TGA)研究热稳定性,以及通过电痕化指数(CTI)测试评估漏电起痕风险。部分高端应用场景已增加长期电老化寿命评估(如20年加速老化模拟),推动检测技术从合规性验证向性能预测延伸。
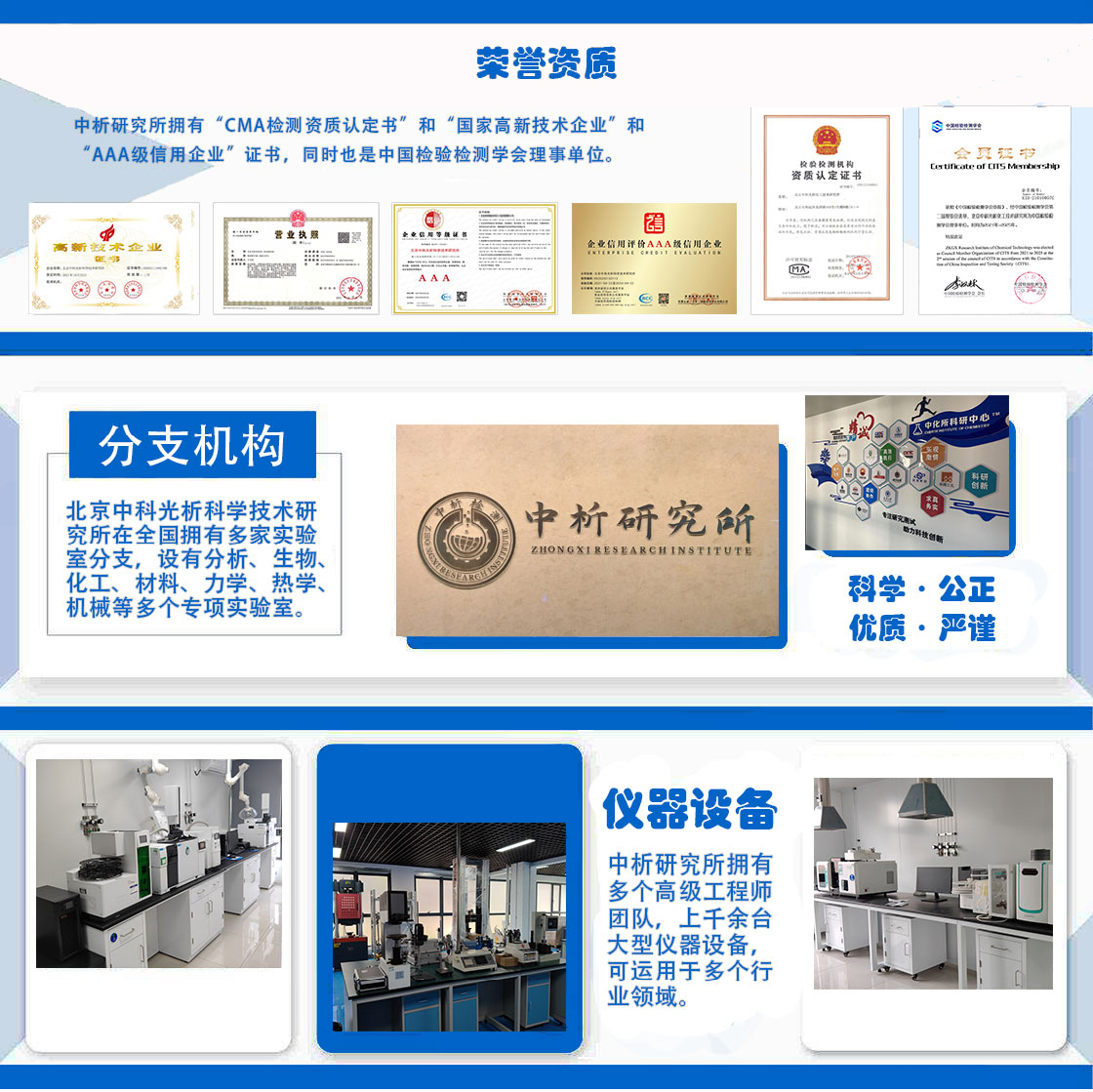
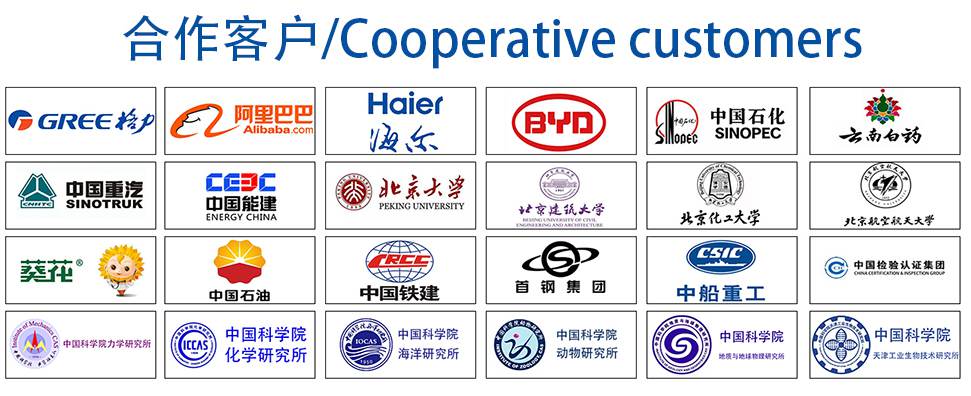