铁道车辆设备检测的重要性与技术要点
铁道车辆作为现代交通运输体系的核心组成部分,其安全性与可靠性直接关系到乘客生命财产安全和铁路运营效率。随着我国高铁网络的快速扩张和既有线路的持续运营,车辆设备检测已成为预防事故、延长设备寿命、保障运输秩序的关键环节。通过系统化、标准化的检测流程,能够及时发现转向架、制动系统、电气设备等核心部件的潜在隐患,避免因零部件故障引发的运行中断或安全事故。
核心检测项目分类与内容
铁道车辆设备检测覆盖机械、电气、结构三大领域,主要包含以下核心项目:
1. 转向架系统检测
作为承载车体重量的核心组件,转向架需进行多维度检测:包括悬挂装置弹性元件状态分析、轮轴几何参数测量(轮缘厚度、轮径差)、轴承温度监控及振动频谱检测。采用三维激光扫描技术对构架变形进行毫米级精度评估,并通过超声波探伤检测焊缝完整性。
2. 制动系统功能验证
涵盖空气制动与电制动双系统的综合测试:制动盘厚度均匀性检测、闸片磨损量测算、制动缸响应时间测定(要求≤1.5秒)。通过车载TCMS系统实时采集制动压强曲线,验证制动减速率是否符合0.8-1.2m/s²的行业标准。
3. 车体结构完整性检测
采用数字图像相关法(DIC)检测车体蒙皮应力分布,运用电磁涡流技术排查铝合金框架的隐性裂纹。重点检查车钩缓冲装置的抗压强度(需≥2.5MN)及贯通道密封件的耐候性能,确保在-40℃至+70℃工况下保持气密性。
4. 电气系统安全检测
包含高压设备绝缘电阻测试(标准值≥100MΩ)、牵引变流器谐波畸变率分析(要求<5%)、车载蓄电池容量衰减检测。运用热成像仪对接触器触头进行温度场监测,及时发现接触不良导致的过热风险。
5. 轮对动态特性检测
在动态检测线上进行轮轨力三维测量,获取脱轨系数(Q/P≤0.8)、轮重减载率(ΔP/P≤0.6)等安全参数。同步开展轮对多边形磨耗识别,通过车载振动传感器捕捉特定阶次的异常振动信号,预防车轮扁疤等典型故障。
智能化检测技术发展
当前检测体系正向智能化方向升级:基于大数据的故障预测系统可提前8000公里预警轴承失效,车载PHM(预测与健康管理)系统实现关键部件剩余寿命计算,无人机自动巡检技术已应用于接触网与车顶设备检查。这些创新技术将检测效率提升40%,误检率降低至0.3%以下。
通过建立覆盖全生命周期的检测-诊断-维护闭环,我国铁道车辆设备可靠性指标已达到国际领先水平,为铁路运输安全提供了坚实保障。未来随着5G通信和数字孪生技术的深度应用,检测体系将实现更高精度的实时监控与智能决策。
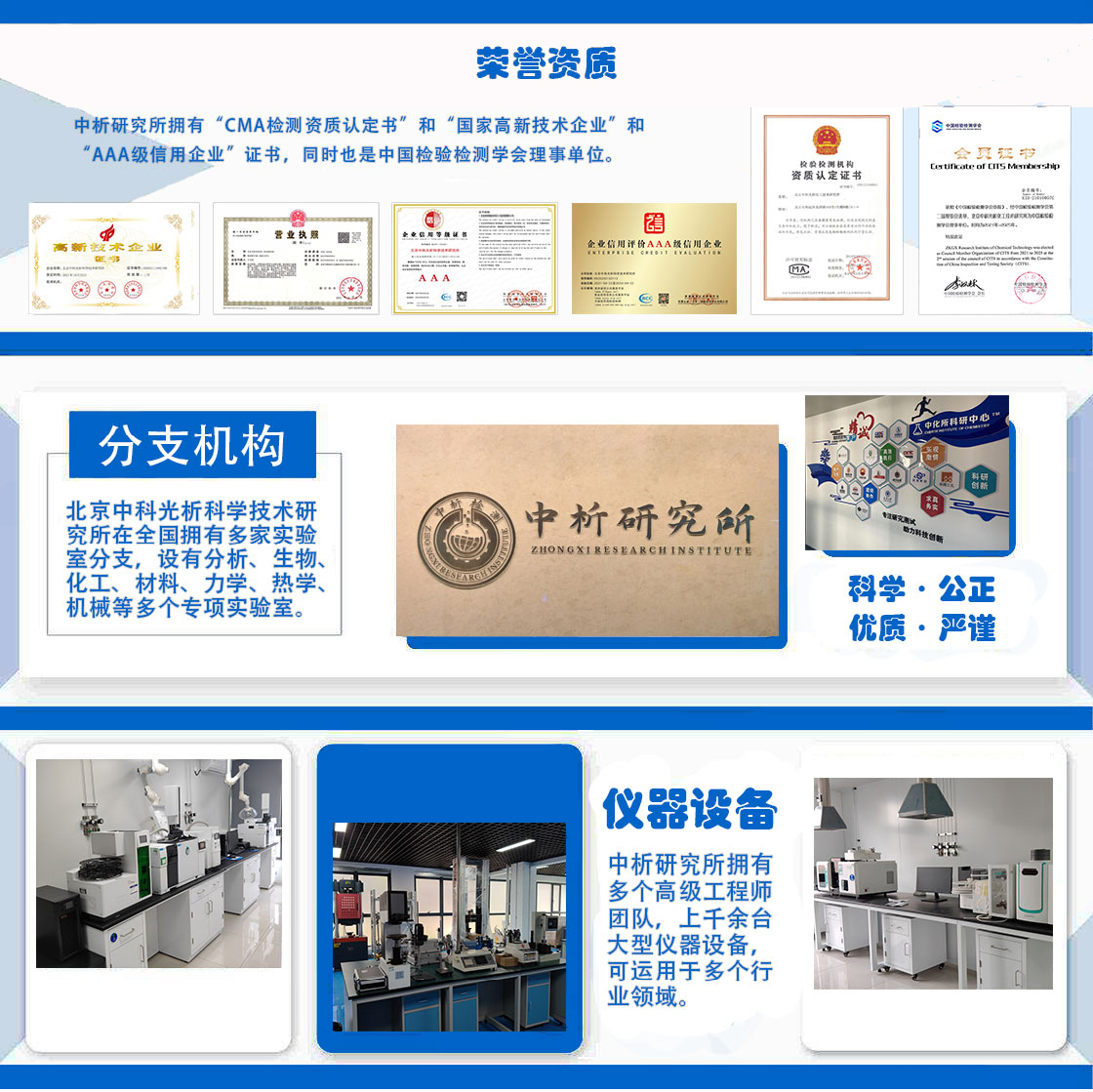
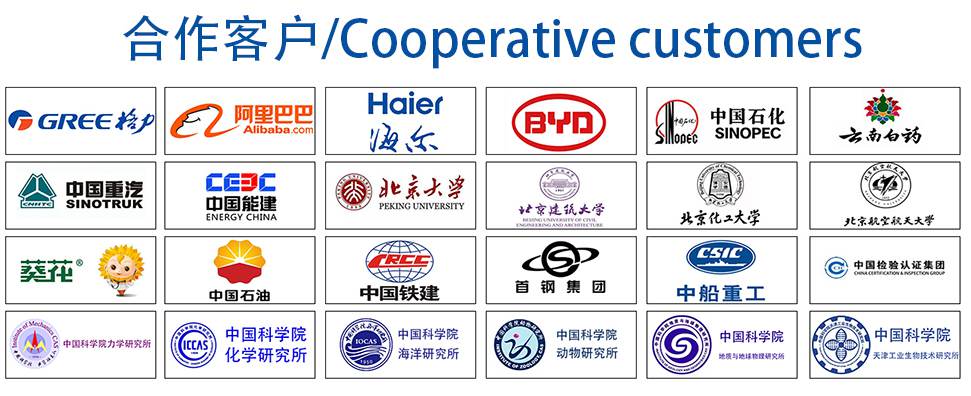