铸件质量检测的重要性
铸件作为机械制造、汽车、航空航天等领域的核心零部件,其质量直接影响产品的性能、安全性和使用寿命。铸造过程中可能因工艺参数波动、材料缺陷或模具问题产生气孔、裂纹、缩松等缺陷,这些隐患若未被及时发现,可能导致零件断裂、设备故障甚至安全事故。因此,铸件质量检测是生产流程中不可或缺的环节,需要通过系统性、多维度的检测项目,确保铸件的几何精度、力学性能和内部结构完整性,从而满足行业标准与设计要求。
铸件质量检测的核心项目
1. 外观与尺寸检测
通过目视检查、三坐标测量仪或光学投影仪,检测铸件表面是否存在裂纹、砂眼、毛刺等缺陷,并验证关键尺寸是否符合公差要求。例如,发动机缸体的铸造变形量需控制在±0.2mm以内,否则将影响装配精度。
2. 化学成分分析
采用光谱分析仪或湿法化学分析,测定材料中碳、硅、锰等元素的含量。以球墨铸铁为例,镁元素残留量需保持在0.03%-0.06%区间,超出范围会导致石墨球化率下降,显著降低材料韧性。
3. 力学性能测试
通过拉伸试验机、冲击试验机等设备,检测抗拉强度、屈服强度、延伸率和冲击功等指标。船用柴油机曲轴铸件的抗拉强度通常要求≥600MPa,确保能承受交变载荷作用。
4. 无损检测(NDT)
综合运用X射线探伤、超声波检测和磁粉探伤技术:
- X射线可发现内部气孔、缩孔(灵敏度达Φ0.5mm)
- 超声波适用于检测深层裂纹(分辨率达1mm)
- 磁粉法用于检测表面及近表面线性缺陷
5. 金相组织分析
通过金相显微镜观察微观组织形态,评估石墨形态、基体结构及晶粒度等级。汽车刹车盘铸件要求珠光体含量>95%,铁素体比例过高会导致耐磨性下降。
6. 压力密封性试验
对液压阀体等承压铸件实施水压试验,在1.5倍工作压力下保压10分钟,检查是否有渗漏现象。航空液压件要求泄漏量<0.1ml/min,确保极端工况下的可靠性。
智能化检测技术发展
随着AI和机器视觉技术的应用,铸件检测正向自动化方向演进。某铸造企业引入深度学习算法后,表面缺陷识别准确率从85%提升至98%,检测效率提高3倍。工业CT扫描技术可实现三维重构,精确量化内部缺陷的体积与分布,为工艺优化提供数据支撑。
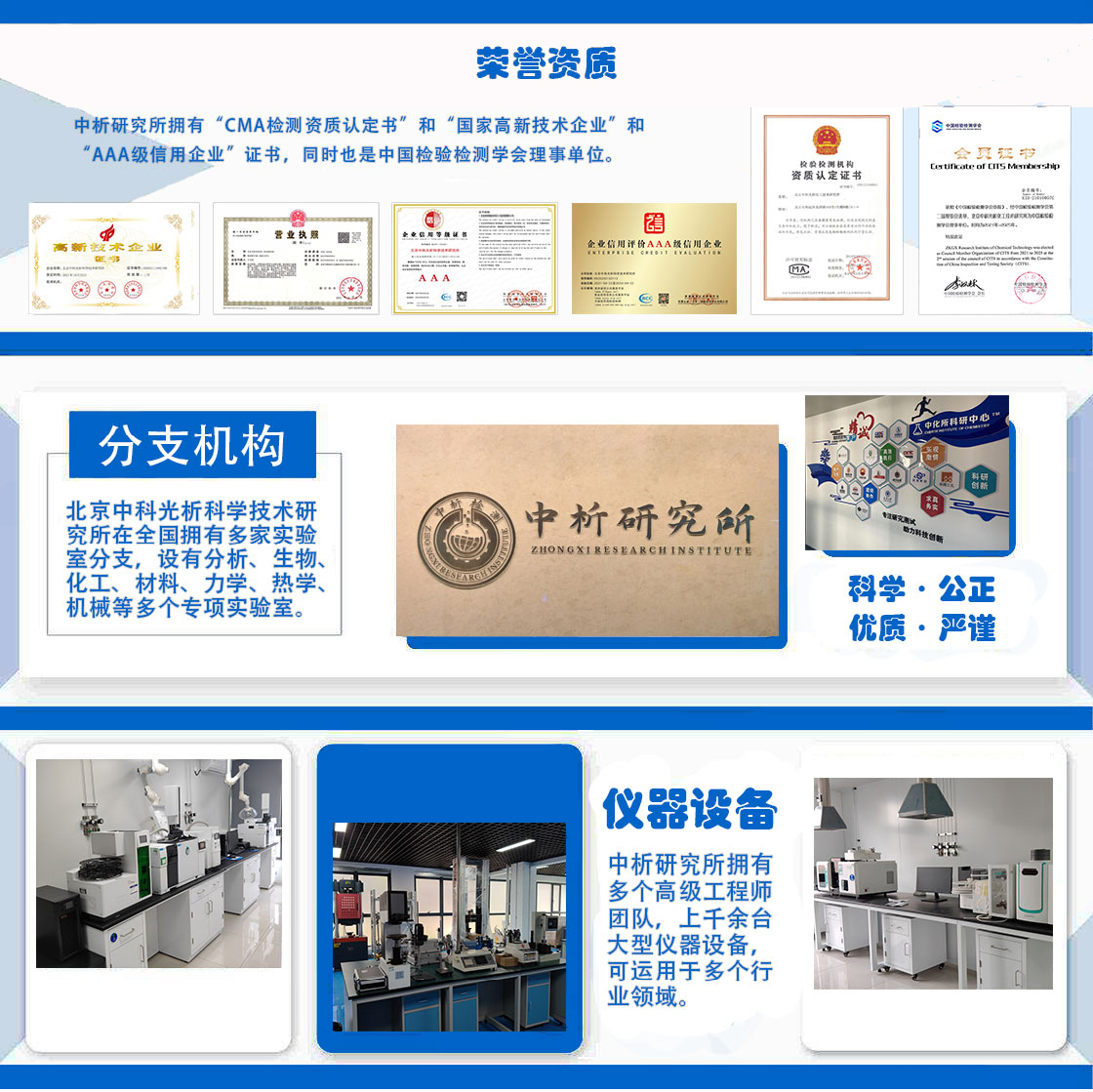
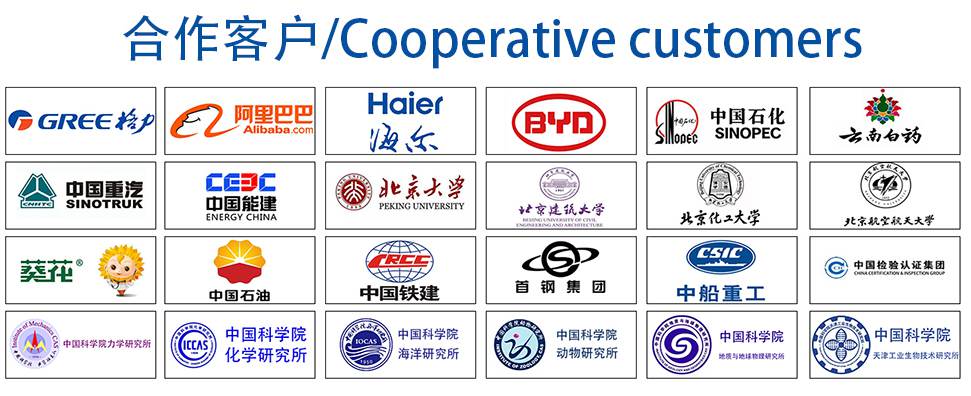