压水堆核电厂设施设备防护涂层检测的重要性
压水堆核电厂作为重要的能源设施,其设备长期处于高温、高压、辐照及化学腐蚀等复杂环境中。防护涂层是保障金属结构耐久性、防止设备腐蚀和放射性物质泄漏的第一道屏障。然而,涂层在运行过程中可能因机械损伤、老化或工艺缺陷导致性能退化。定期开展防护涂层检测不仅能够评估涂层状态、延长设备使用寿命,还能有效预防因涂层失效引发的安全隐患,对核电厂的运行安全和成本控制具有重要意义。
防护涂层检测的核心项目
1. 外观完整性检测
通过目视检查、高清成像技术或无人机巡检,评估涂层表面是否存在开裂、剥落、起泡、锈蚀等缺陷。重点检查焊接接头、法兰连接处等易损区域,记录缺陷位置及面积占比,为后续修复提供依据。
2. 涂层厚度测量
采用磁感应测厚仪或超声波测厚仪对涂层厚度进行定量分析,要求符合设计规范(通常为200-400μm)。对关键设备(如反应堆压力容器、蒸汽发生器)需执行网格化多点测量,统计厚度均匀性并识别局部过薄区域。
3. 附着力测试
使用划格法、拉开法或胶带剥离法检测涂层与基材的结合强度。对于辐照区域需采用远程操作设备,确保测试过程符合辐射防护要求。附着力低于5MPa时需触发预警机制。
4. 电化学性能分析
通过电化学阻抗谱(EIS)和极化曲线测试,评估涂层的耐腐蚀性能。重点监测涂层孔隙率、离子渗透率等参数,预测涂层在硼酸环境下的长期稳定性。
5. 老化与辐照损伤评估
采用傅里叶红外光谱(FTIR)分析涂层树脂的氧化降解程度,结合加速老化实验数据建立寿命预测模型。对高辐照区域的涂层还需检测交联密度变化,评估抗辐照性能衰减情况。
6. 修复涂层验收检测
在涂层修复后实施阶梯式验收:表面处理洁净度检测(Sa2.5级)、修补层厚度复测、24小时湿膜附着力测试,确保修复区域性能达到原设计标准的90%以上。
智能化检测技术应用趋势
近年发展出的涂层缺陷AI识别系统、激光诱导击穿光谱(LIBS)原位分析仪等新技术,已逐步应用于核电厂检测作业。通过建立涂层数字孪生数据库,实现全生命周期状态监控,大幅提升检测效率和缺陷识别准确率。
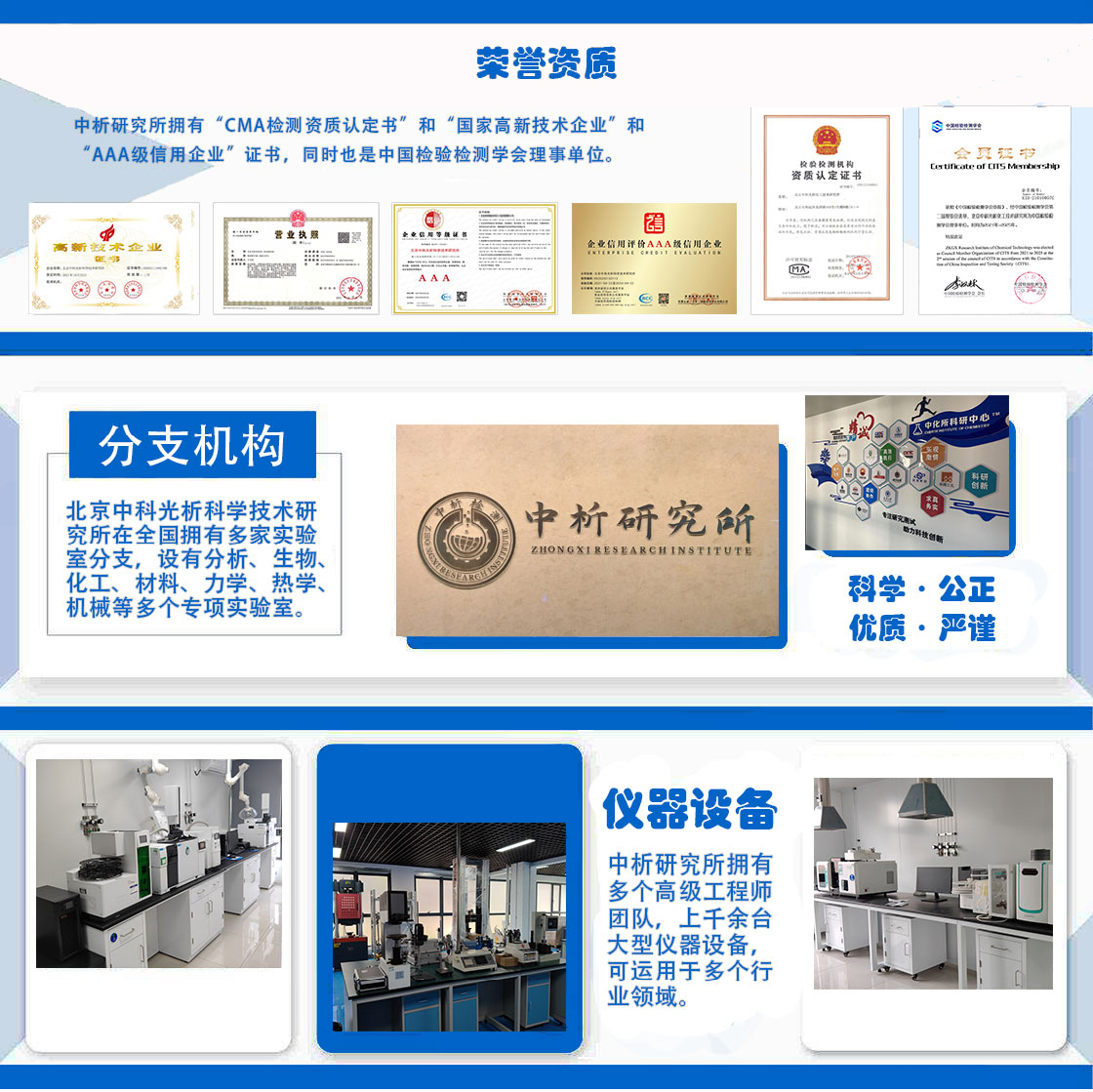
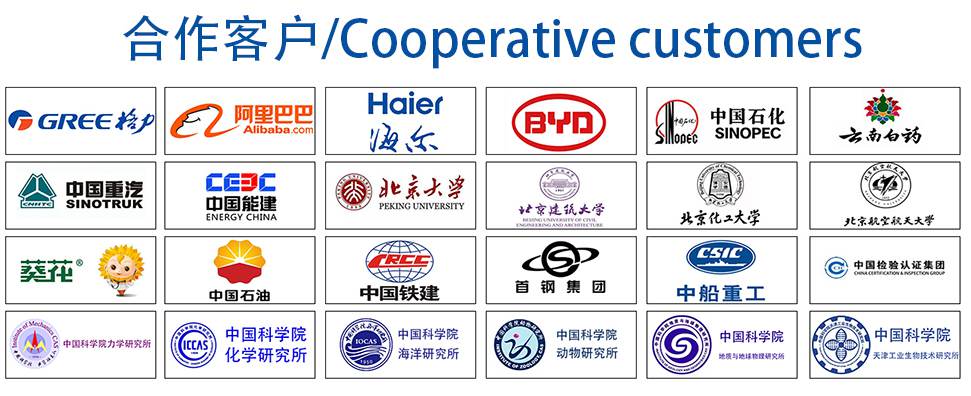