柴油机电控共轨喷油系统高压供油泵总成检测
柴油机电控共轨喷油系统是现代柴油发动机的核心技术之一,其高压供油泵总成作为系统的“心脏”,承担着为共轨管提供高压燃油的关键任务。随着发动机对燃油喷射压力、精度及环保性能要求的不断提高,高压供油泵总成的可靠性直接影响发动机的动力输出、燃油经济性及排放水平。因此,对高压供油泵总成的定期检测与状态评估,成为保障系统正常运行、预防突发故障的重要环节。
一、压力性能检测
高压供油泵的核心功能是建立稳定的燃油压力。检测时需使用专用压力测试仪,结合发动机ECU读取实时数据,验证泵体在不同转速和负荷工况下的压力输出能力。重点观察以下指标:
1. 最大压力是否达到设计值(通常为1600-2500bar);
2. 压力波动范围是否在允许误差内(一般不超过±50bar);
3. 压力建立速度是否符合标准(冷启动时需快速响应)。
若出现压力不足或波动异常,需排查柱塞偶件磨损、调压阀故障或进油量不足等问题。
二、密封性检测
高压环境下的密封失效会导致燃油泄漏和压力衰减。检测包含以下步骤:
1. 静态密封性:通过目视检查泵体表面、管路接口是否渗油;
2. 动态密封性:在高压工况下使用荧光检漏剂或红外热成像仪定位微小泄漏点;
3. 柱塞密封环测试:通过保压试验判断柱塞副磨损程度,正常保压10分钟内压力下降不超过10%。
三、电磁阀响应检测
高压泵的燃油计量单元(MEUN)通常采用电磁阀控制,其性能直接影响供油量精度:
1. 使用示波器检测电磁阀驱动电流波形,确认开关响应时间(一般≤2ms);
2. 测试电磁阀线圈电阻值(典型值3-10Ω)及绝缘性能;
3. 通过ECU模拟信号输入,验证流量调节阀的线性度与控制精度。
四、机械部件磨损分析
对关键运动部件进行拆解检测:
1. 柱塞与套筒配合间隙(极限值0.003-0.005mm);
2. 凸轮轴表面硬度及型线磨损量;
3. 轴承游隙与润滑通道畅通性;
4. 齿轮传动副啮合间隙(通过着色法检测接触面积)。超过磨损极限的部件必须更换。
五、控制信号与软件诊断
结合诊断仪进行系统级检测:
1. 检查ECU与高压泵的CAN通信信号是否稳定;
2. 读取历史故障码,分析轨压传感器、温度传感器等关联参数;
3. 通过编程器刷新泵体控制MAP,验证软件版本兼容性。
通过上述系统性检测,可全面评估高压供油泵总成的技术状态,及时修复隐患。建议每运行2000小时或车辆行驶10万公里进行一次专业检测,结合燃油品质监控与滤清器更换,可显著延长泵体使用寿命,保障发动机高效稳定运行。
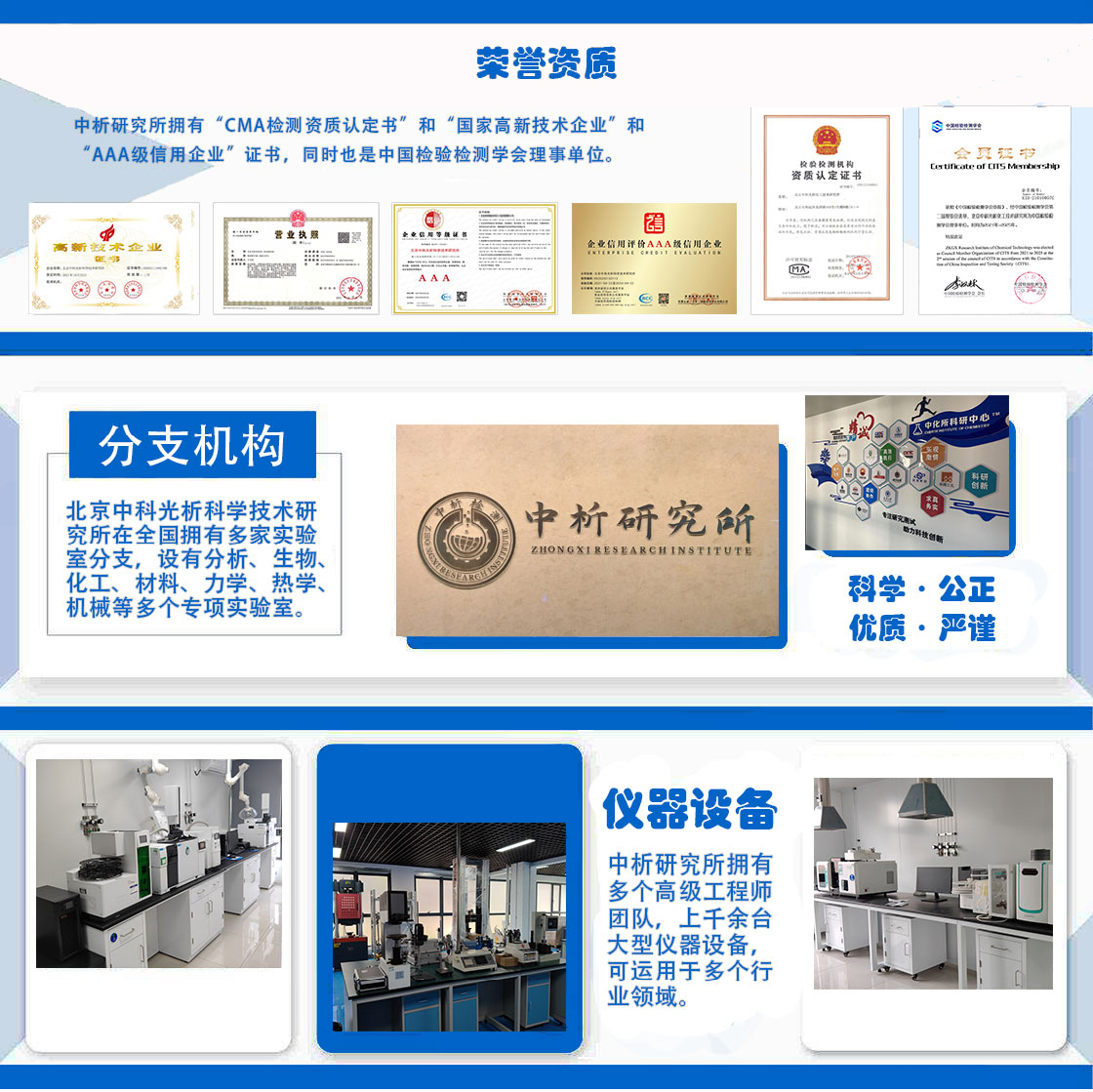
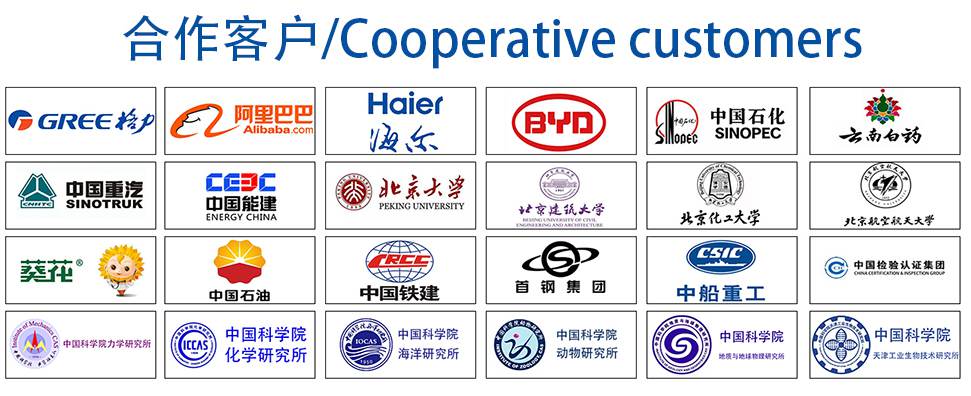