压力控制器检测的重要性
压力控制器是工业自动化、暖通空调、能源设备等领域中广泛应用的关键控制元件,其核心功能是通过监测系统压力并输出控制信号,确保设备在安全压力范围内运行。由于其直接关系到生产安全与系统稳定性,定期开展压力控制器检测项目至关重要。通过科学规范的检测,能够验证控制器动作精度、响应速度及密封性能等关键指标,避免因设备老化、误差累积或环境因素导致的误动作、泄漏甚至系统瘫痪风险。同时,检测还可帮助企业满足行业规范(如GB/T 22093-2018等标准)、降低维护成本并延长设备使用寿命。
压力控制器主要检测项目
1. 外观与机械结构检查
通过目视检测压力控制器外壳完整性、接口密封性及内部弹簧、膜片等机械部件的磨损情况,确认无裂纹、锈蚀或变形。使用游标卡尺测量关键尺寸是否符合出厂参数,确保安装适配性。
2. 动作点与复位点测试
在压力校验台上逐步增压/减压,记录控制器触点切换时的压力值。重复测试3-5次,计算设定值与实际动作点的偏差,误差需控制在量程的±1.5%以内。同时验证复位点与动作点的差值(即死区范围)是否满足设计要求。
3. 气密性试验
将控制器接入密封系统并加压至1.5倍额定压力,保压15分钟。采用气泡法或压降法检测阀体、接口处的泄漏量,要求泄漏率低于0.1mL/min。对于防爆型控制器需额外进行IP65防护等级验证。
4. 电气性能检测
使用兆欧表测量绝缘电阻(≥100MΩ/500VDC),耐压测试仪施加2000VAC/1min验证耐压强度。同时检测触点接触电阻(≤50mΩ)及开关动作时的电弧消除能力,确保控制信号的稳定传输。
5. 环境适应性测试
在温湿度试验箱中模拟-40℃~85℃的温度循环,检测控制器在不同温湿度条件下的动作精度漂移。高温试验后需验证材料抗老化性能,低温环境下检查润滑脂是否冻结导致动作迟滞。
6. 长期稳定性验证
通过72小时连续压力循环测试(每分钟10次频率),统计触点磨损情况及压力重复性误差。对比初期与末期数据,性能衰减不得超过允许范围的30%,评估控制器的使用寿命。
检测流程与设备配置
标准检测需配置精密压力源(精度0.05级)、数字压力表、数据采集系统及专用测试工装。检测前需进行设备校准,测试环境温度应控制在23±5℃,湿度≤85%RH。建议每12个月或5000工作小时进行周期性检测,恶劣工况下需缩短检测间隔。
结语
系统化的压力控制器检测不仅能提前发现潜在故障,更能通过数据追溯优化设备选型与维护策略。企业应建立完整的检测档案,结合智能传感器与物联网技术实现预测性维护,从而最大限度保障生产系统的安全高效运行。
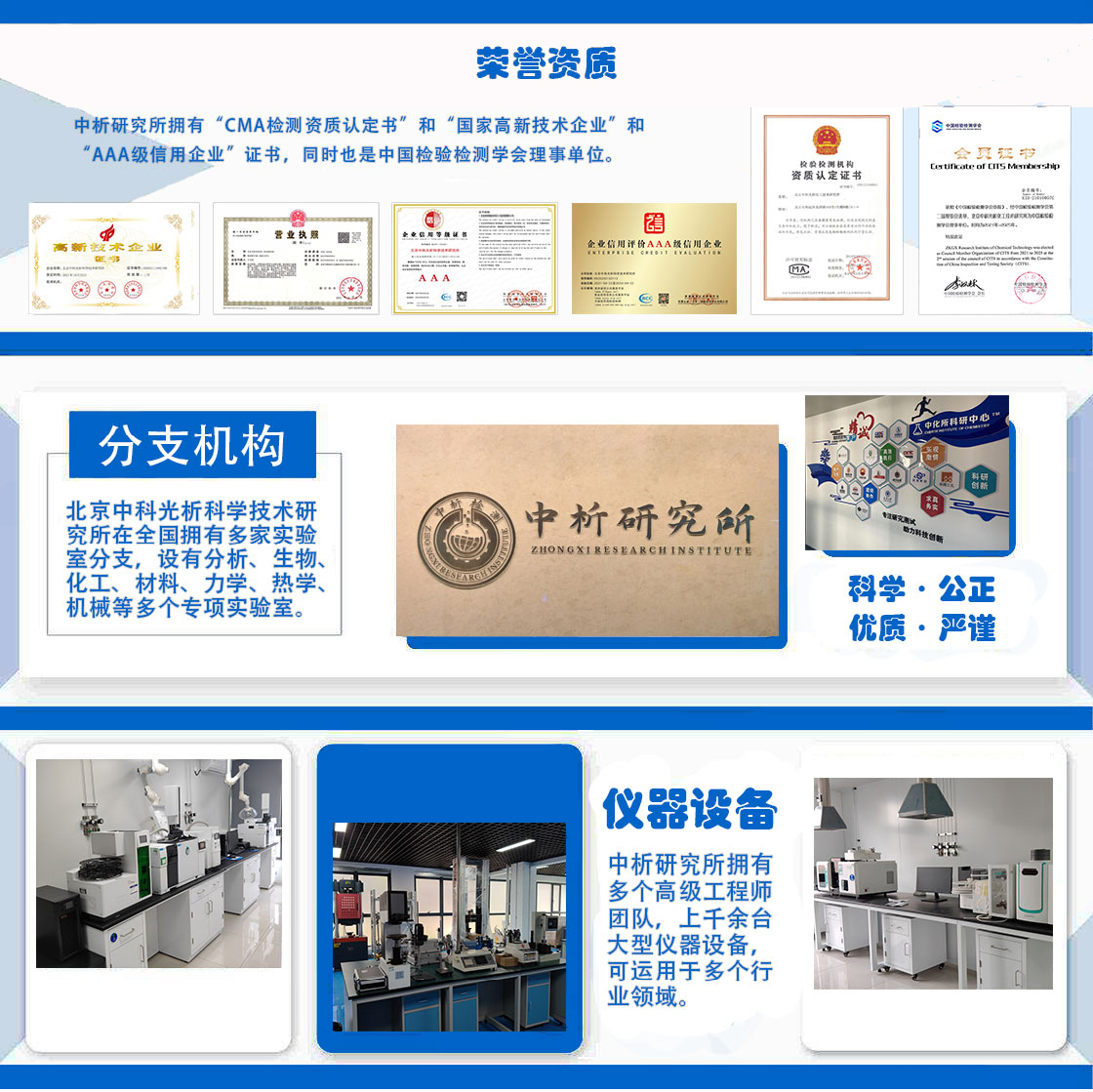
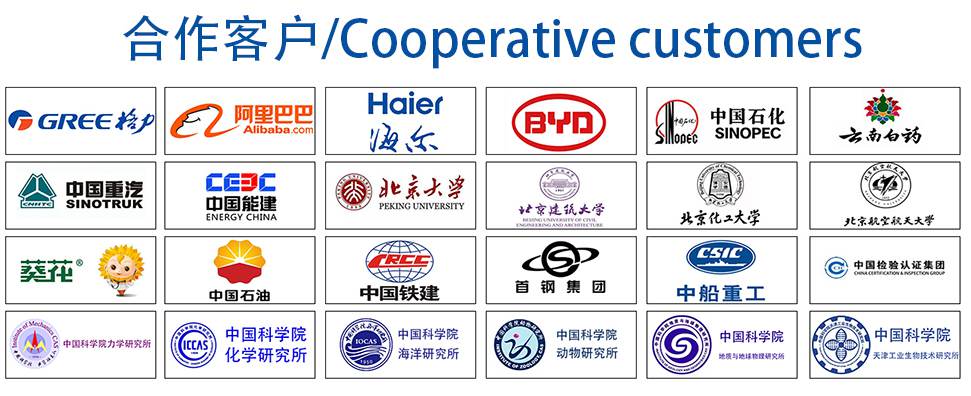