爆炸性环境设备检测的重要性与实施要点
在石油化工、矿山、粉尘加工等高风险行业中,爆炸性环境设备的可靠性直接关系到人员安全和生产连续性。此类设备需长期暴露于易燃气体、蒸气或粉尘环境中,任何设计缺陷或性能退化都可能引发灾难性事故。因此,爆炸性环境设备检测不仅是国际通行的强制性安全要求(如ATEX指令、IECEx体系),更是企业履行社会责任的核心环节。检测过程需严格遵循GB 3836系列标准(中国防爆标准)、EN 60079(欧盟标准)等技术规范,通过系统性验证设备在极端条件下的安全性。
核心检测项目解析
1. 防爆结构完整性检测
针对隔爆外壳(Ex d)、增安型(Ex e)、本质安全型(Ex i)等不同防爆型式,采用压力测试、接合面间隙测量、冲击试验等方法验证结构是否符合设计规范。例如隔爆型设备需通过1.5倍参考压力的动态燃爆测试,确保火焰阻隔能力。
2. 材料相容性测试
检测设备外壳、密封件等材料与爆炸性介质的化学兼容性,包括抗腐蚀性、抗静电性及耐高温性能。通过盐雾试验、表面电阻测试(要求≤1×10⁹Ω)、灼热丝试验(如960℃耐燃测试)等手段评估材料安全性。
3. 温度组别验证
采用热成像仪与热电偶监测设备表面及内部元件的最高工作温度,确保不超过对应气体/粉尘的引燃温度(如T6组别要求≤85℃)。测试时需模拟设备在额定负载、过载15%等极端工况下的温升数据。
4. 防护等级(IP)测试
通过粉尘箱试验(IP6X)、喷水试验(IPX5)验证设备外壳对危险介质的隔绝能力。例如粉尘防爆设备需在20m³/h流速的滑石粉环境中持续喷射8小时,内部无可见沉积。
5. 非金属部件评估
对绝缘材料、电缆护套等非金属部件进行CTI值(相比漏电起痕指数)测定,要求≥175V(ⅡA类气体)至≥100V(ⅢC类粉尘)。同时开展紫外线老化试验,评估材料在长期使用后的性能稳定性。
6. 机械强度测试
实施7焦耳冲击能量试验(参考IEC 60079-0)、振动试验(10-150Hz扫频振动3小时)及跌落测试,确保设备在运输、安装过程中的结构可靠性。
7. 安全参数监测
对本质安全回路进行电压/电流/功率限制值检测,确保电路能量低于最小点燃能量(如甲烷为0.28mJ)。采用火花试验装置模拟故障条件下的潜在点火风险。
检测流程优化建议
建议企业建立全生命周期检测体系,新设备需通过型式试验+出厂检验,在役设备实施周期性维护检测(通常每3年全面检测1次)。采用X射线探伤技术检测铸件缺陷,运用红外热像仪进行在线温度监测,结合大数据分析预测设备劣化趋势,可提升检测效率30%以上。
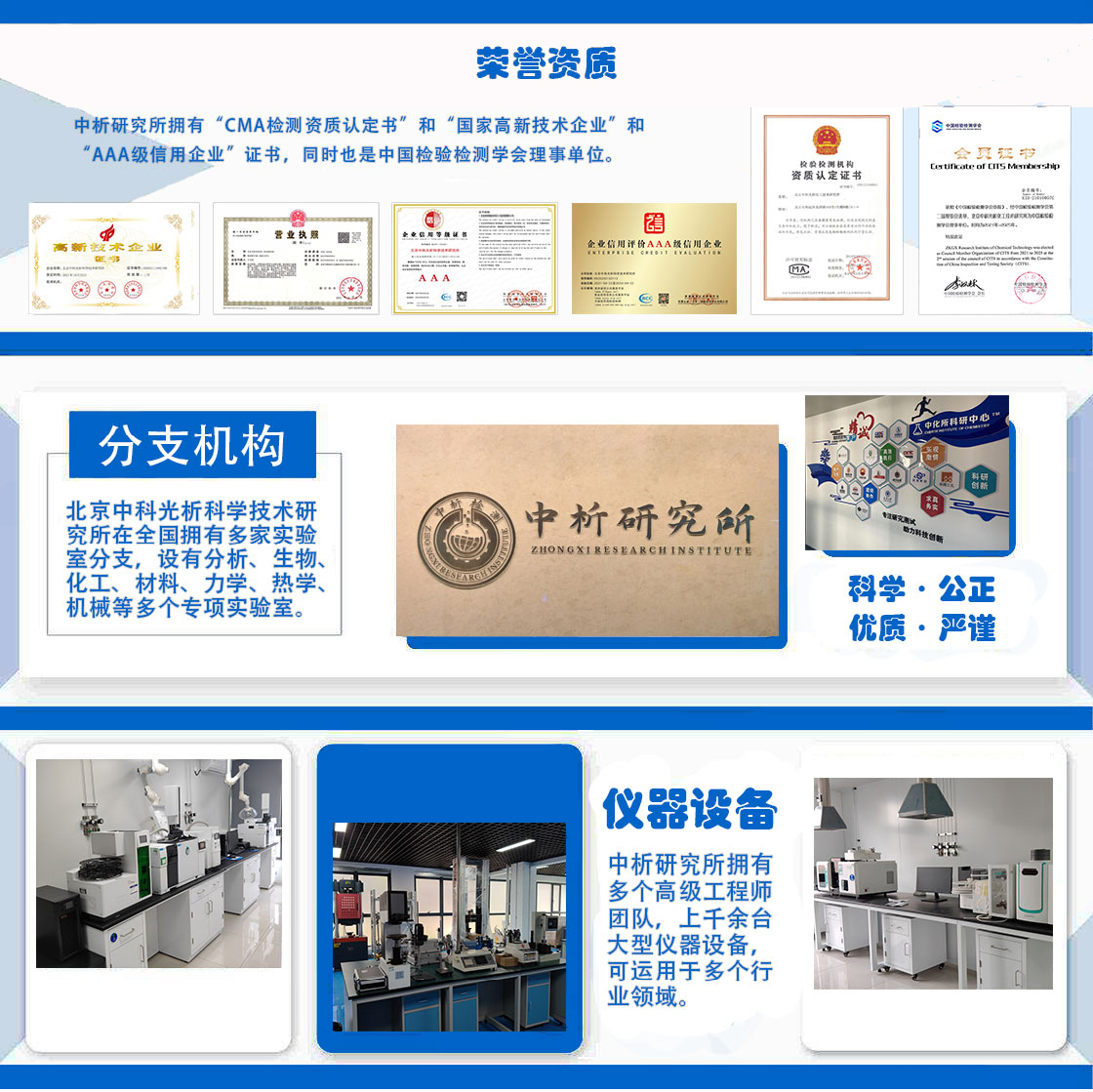
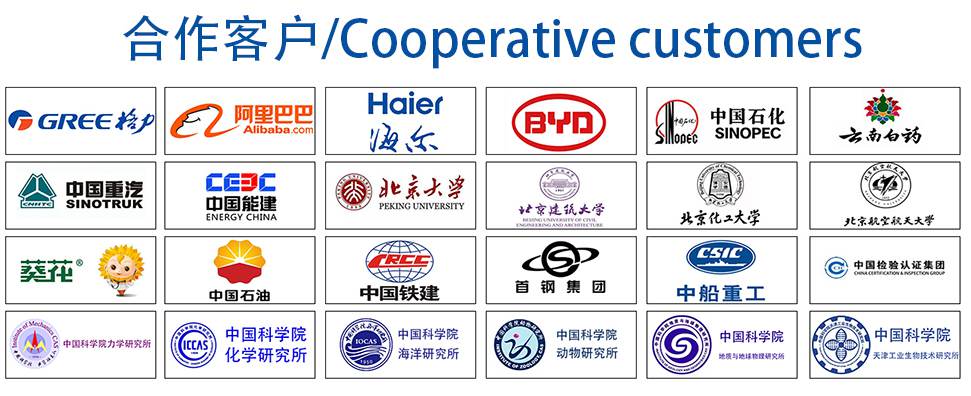