焊接管材检测的重要性与应用范围
焊接管材作为工业生产和基础设施建设中广泛使用的材料,其质量直接关系到管道系统的安全性、密封性和使用寿命。焊接管材检测是通过科学手段对焊缝及管体进行质量评估的关键环节,广泛应用于石油化工、天然气输送、建筑工程、机械制造等领域。由于焊接过程中可能产生气孔、裂纹、未熔合等缺陷,且材料强度、耐腐蚀性等性能易受工艺影响,因此需要通过系统化的检测项目确保产品符合国家标准(如GB/T 3091、API 5L)或国际规范(如ASTM、ISO)。
焊接管材核心检测项目
1. 外观质量检查
通过目视或放大设备对焊缝及管体表面进行观察,检测是否存在裂纹、咬边、焊瘤、凹陷等显性缺陷。同时检查焊缝成型是否均匀,管材表面是否有锈蚀、划痕等影响使用的质量问题。
2. 尺寸精度测量
使用卡尺、超声波测厚仪等工具对管材的外径、壁厚、椭圆度、直线度等指标进行测量,确保其符合设计公差要求。重点关注焊缝区域的几何尺寸一致性,例如余高是否在标准范围内(通常要求0-3mm)。
3. 力学性能测试
通过拉伸试验、弯曲试验和冲击试验评估焊接接头的机械性能:
- 拉伸试验:测定焊缝抗拉强度、屈服强度及延伸率
- 冷弯试验:检查焊缝在弯曲变形下的抗开裂能力
- 冲击试验:评估低温环境下焊缝的韧性表现
4. 无损检测(NDT)
采用非破坏性检测技术排查内部缺陷:
- 超声波检测(UT):精准定位焊缝内部的夹杂、未熔合缺陷
- 射线检测(RT):通过X射线或γ射线成像分析缺陷形态
- 磁粉检测(MT)/渗透检测(PT):用于表面及近表面缺陷筛查
5. 化学成分分析
使用光谱仪对母材和焊材进行元素成分检测,确保材料符合牌号要求,重点关注碳当量(Ceq)对焊接性的影响,防止因成分偏差导致脆性断裂风险。
6. 耐压与气密性试验
通过水压试验或气压试验验证管道的承压能力和密封性能,试验压力一般为设计压力的1.25-1.5倍,保压时间需满足相关标准规定。
7. 腐蚀性能评估
针对特殊用途管材(如海洋工程用管),需进行盐雾试验、晶间腐蚀试验等,评估其在腐蚀环境中的耐久性。同时检测焊缝区域的显微硬度,避免因硬度异常加速腐蚀进程。
检测流程标准化管理
现代焊接管材检测需建立从原材料入厂检验、过程质量控制到成品验收的全流程管理体系。采用自动化检测设备(如在线涡流检测系统)与人工复检相结合的方式,确保检测数据的准确性。检测报告应完整记录各项参数,并实现质量追溯,为工程安全提供可靠保障。
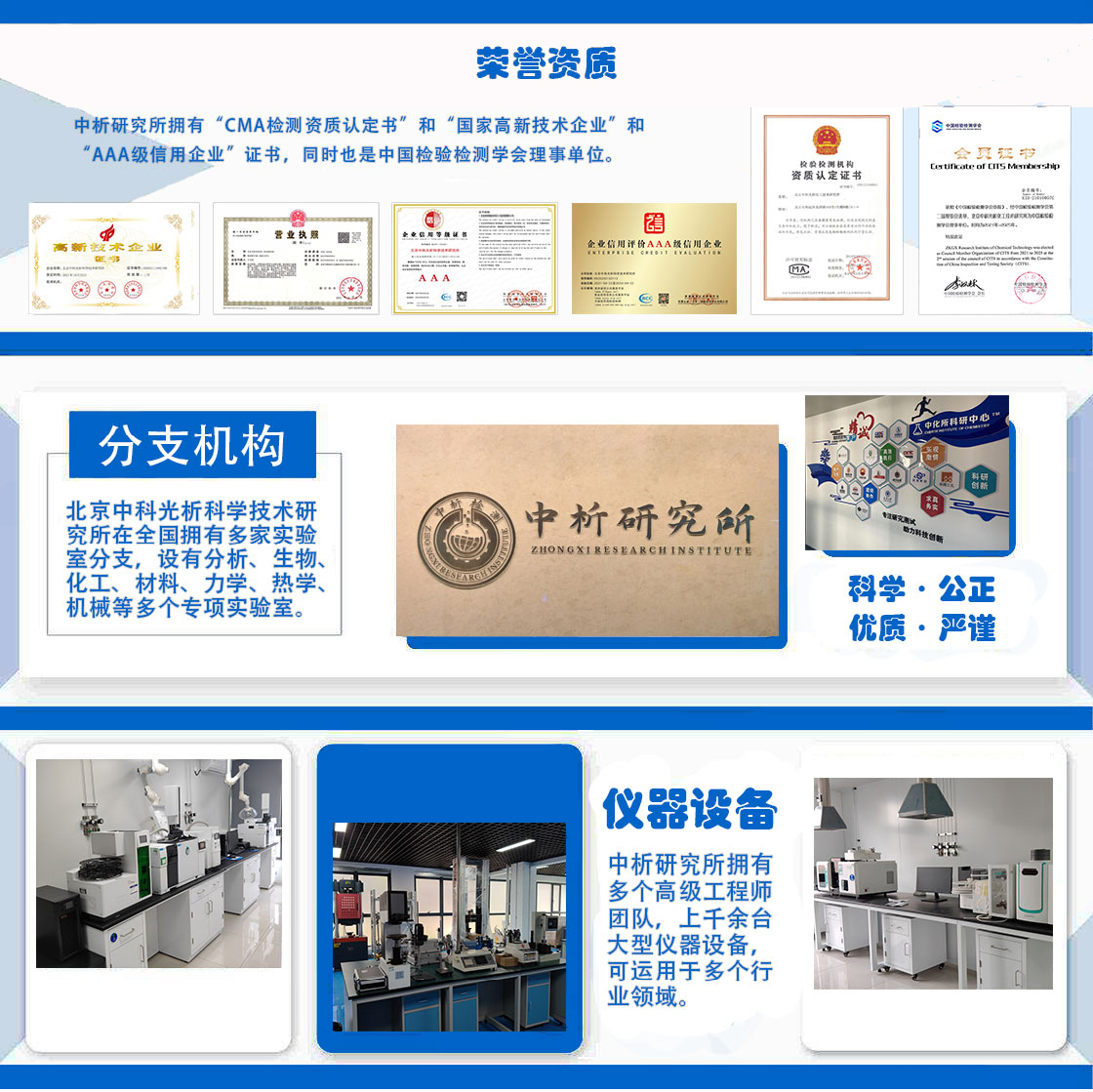
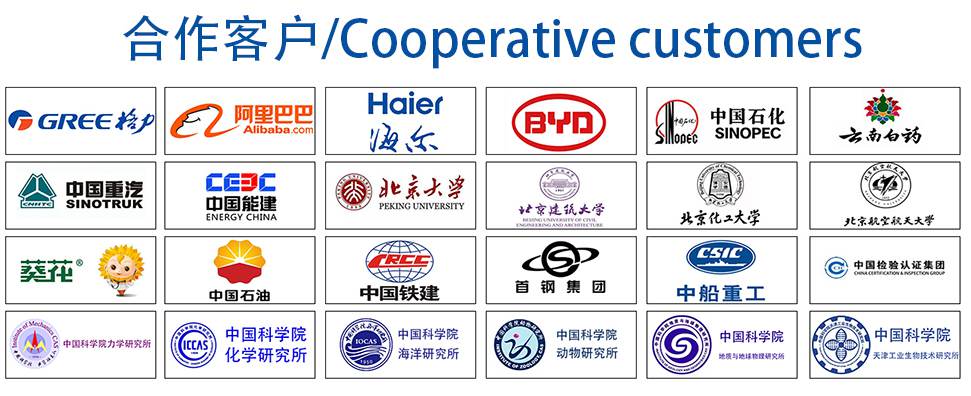