钢检测:保障材料性能的核心技术体系
在机械制造、建筑工程、轨道交通等领域,钢材作为基础性结构材料,其质量直接影响着设备安全和使用寿命。根据国家市场监管总局2023年数据显示,我国每年因材料缺陷导致的工业事故中,钢材质量问题占比达37%。现代钢检测体系通过科学化的检测手段,系统性评估材料的化学成分、力学性能和工艺特性,已成为确保材料可靠性的重要技术保障。
一、化学成分分析
采用直读光谱仪(OES)和ICP发射光谱仪进行元素定量检测,重点检测碳(C)、硅(Si)、锰(Mn)、磷(P)、硫(S)五大基础元素含量,镍(Ni)、铬(Cr)、钼(Mo)等合金元素配比。依据GB/T 4336-2016标准,碳钢碳含量允许偏差控制在±0.03%,不锈钢铬含量偏差不超过±1.5%。齐全实验室已实现0.0001%级的微量元素检测精度。
二、力学性能测试
通过微机控制万能试验机进行拉伸试验,测定屈服强度(Rp0.2)、抗拉强度(Rm)、断后伸长率(A)等关键指标。冲击试验采用夏比V型缺口试样,在-40℃~常温范围内测试冲击吸收功。硬度检测包含布氏(HBW)、洛氏(HRC)、维氏(HV)三种方法,依据GB/T 228.1-2021标准,不同钢种应选用对应检测方法。
三、金相组织检测
使用金相显微镜(1000倍)和扫描电镜(SEM)观察材料微观结构,评估晶粒度(GB/T 6394)、非金属夹杂物(GB/T 10561)、脱碳层深度等指标。奥氏体不锈钢需检测δ铁素体含量,工具钢需确认碳化物分布状态。最新数字图像分析系统可实现组织定量评级,误差小于0.5级。
四、无损检测技术
超声波探伤(UT)可发现内部2mm以上缺陷,磁粉检测(MT)用于表面裂纹检测灵敏度达0.1mm,射线检测(RT)适用复杂结构件内部缺陷分析。根据NB/T 47013标准,压力容器用钢板必须进行100%超声波检测,焊缝需进行射线检测Ⅱ级合格。
五、腐蚀性能试验
中性盐雾试验(NSS)按GB/T 10125标准持续720h,不锈钢试样表面不得出现基体腐蚀。晶间腐蚀试验采用硫酸-硫酸铜法,弯曲后放大10倍观察无裂纹。海洋工程用钢还需进行模拟海水全浸试验,年腐蚀速率应小于0.1mm/a。
六、尺寸与公差检测
使用三坐标测量仪检测钢板平直度(≤3mm/m)、厚度公差(±0.15mm)。钢管椭圆度要求≤1%D,轧制H型钢翼缘斜度≤1.5%。依据GB/T 709-2019,热轧钢板宽度允许偏差分为普通精度(0~+25mm)和较高精度(0~+15mm)两个等级。
七、特殊性能检测
耐候钢需进行周期浸润腐蚀试验,模拟大气环境腐蚀120周期。低温钢冲击试验温度延伸至-196℃(液氮环境)。抗震钢筋需进行反向弯曲试验,弯曲角度135°不得出现裂纹。这些专项检测确保钢材满足特定工况需求。
完备的钢检测体系包含34项基础检测项目和18项特殊检测项目,检测周期从现场快速筛查的2小时到长期性能测试的90天不等。选择具备CMA和 资质的检测机构,采用符合ASTM、ISO、JIS等多国标准的检测方案,可确保检测结果的国际互认性,为材料选用提供科学依据。
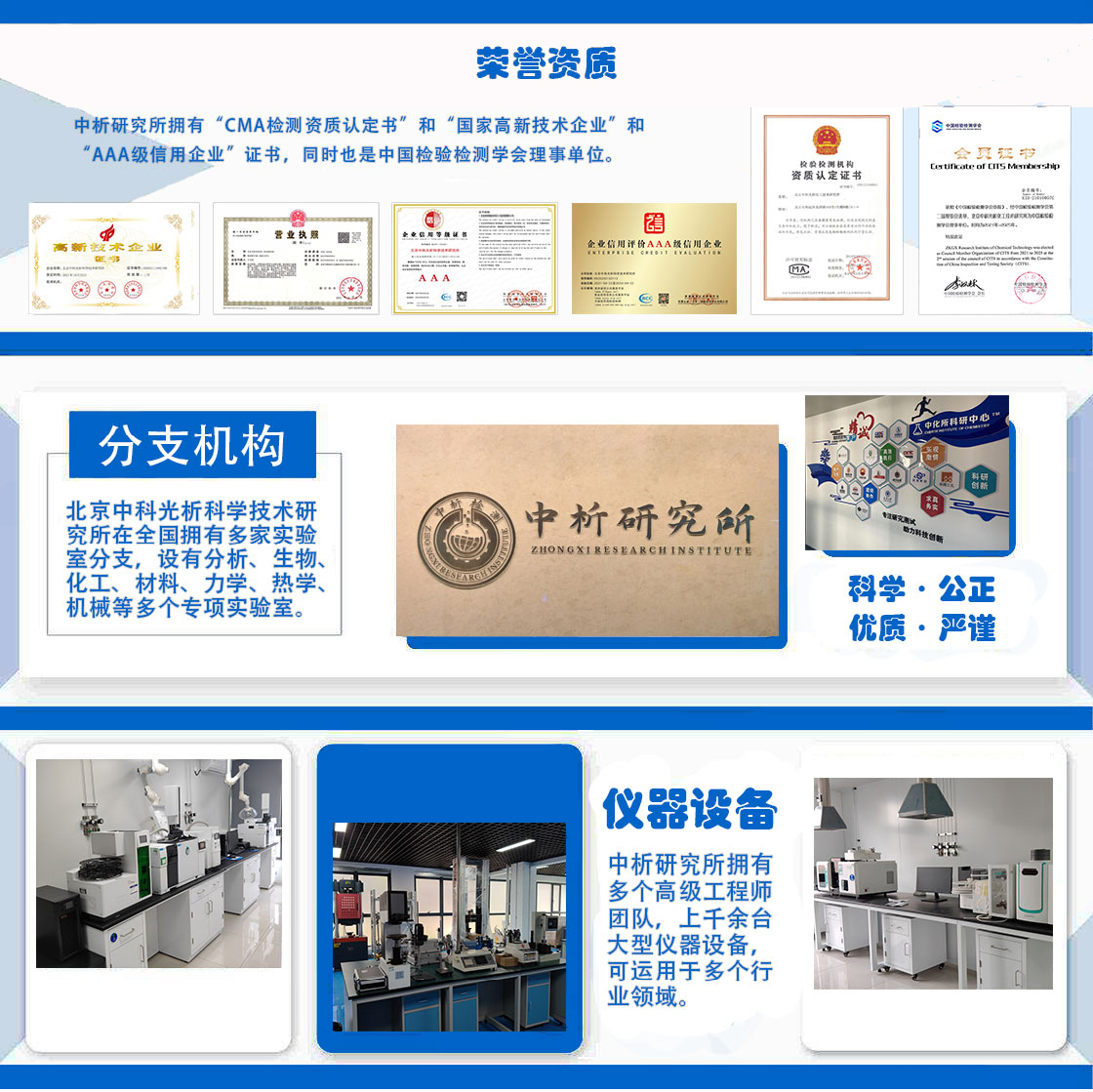
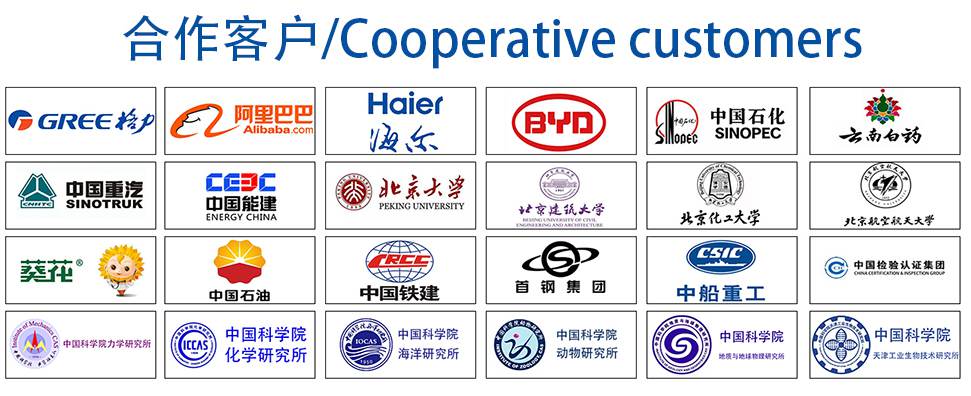