电动汽车用驱动电机系统检测的重要性与发展背景
随着新能源汽车产业的快速发展,驱动电机系统作为电动汽车的"心脏",其性能直接决定了车辆的动力输出、续航里程和运行安全性。根据中国汽车工程学会统计,2023年我国新能源车电机系统市场规模已突破800亿元,年检测需求增长率达35%以上。驱动电机系统的检测不仅关乎产品质量控制,更是实现"双碳"目标下能效提升的核心环节。
行业标准GB/T 18488-2015《电动汽车用驱动电机系统》明确规定,驱动电机系统必须通过八大类36项关键性能检测才能投入量产。这些检测贯穿研发验证、生产质检和售后维护全生命周期,形成了覆盖电气性能、机械特性、环境适应性等多维度的完整检测体系。
核心检测项目体系解析
1. 电气性能检测
(1)效率特性测试:在额定电压下,通过测功机系统测量电机在5%-150%负载范围内的效率曲线,要求最高效率点不低于94%。采用ISO 8854标准中的MAP图法绘制全工况效率图谱。
(2)转矩-转速特性:使用高精度扭矩传感器(精度±0.2%)测试堵转转矩、最大转矩及恒功率区特性,验证与设计值的偏差不超过±5%。
2. 环境适应性测试
(1)高低温循环试验:-40℃至120℃温度冲击测试,验证绕组绝缘电阻(≥500MΩ)和密封件性能。某品牌电机在此项测试中出现密封圈脆化问题,促使行业改进材料耐候性标准。
(2)盐雾腐蚀测试:按GB/T 2423.17标准进行96小时5%NaCl溶液喷雾,检测壳体防护等级维持IP67的能力。
3. 电磁兼容性(EMC)检测
(1)传导发射测试:在30MHz-108MHz频段,使用LISN网络测量控制器的传导干扰,要求低于CISPR 25 Class3限值。
(2)辐射抗扰度测试:依据ISO 11452-2标准,在电波暗室中进行200V/m场强辐射,确保系统功能不降级。
4. 耐久性验证
(1)台架耐久试验:模拟整车工况进行2000小时连续交变负载测试,功率循环次数超100万次,检测轴承磨损和永磁体退磁情况。
(2)振动疲劳测试:按SAE J2380标准施加XYZ三轴随机振动,峰值加速度达25g,验证结构件抗疲劳性能。
前沿检测技术发展趋势
当前行业正加速应用数字孪生技术,通过构建电机系统的虚拟样机,实现80%的检测项目在仿真阶段完成。某头部企业采用AI驱动的预测性检测系统,使故障预警准确率提升至92%。同时,基于碳化硅器件的高频化检测(开关频率达100kHz)催生新型宽频测量设备研发,推动检测技术持续升级。
随着国际电工委员会(IEC)正在制定的新版电动汽车电机标准,未来检测体系将更强调系统级能效评价和网络安全防护,驱动检测方法向智能化、集成化方向深度演进。
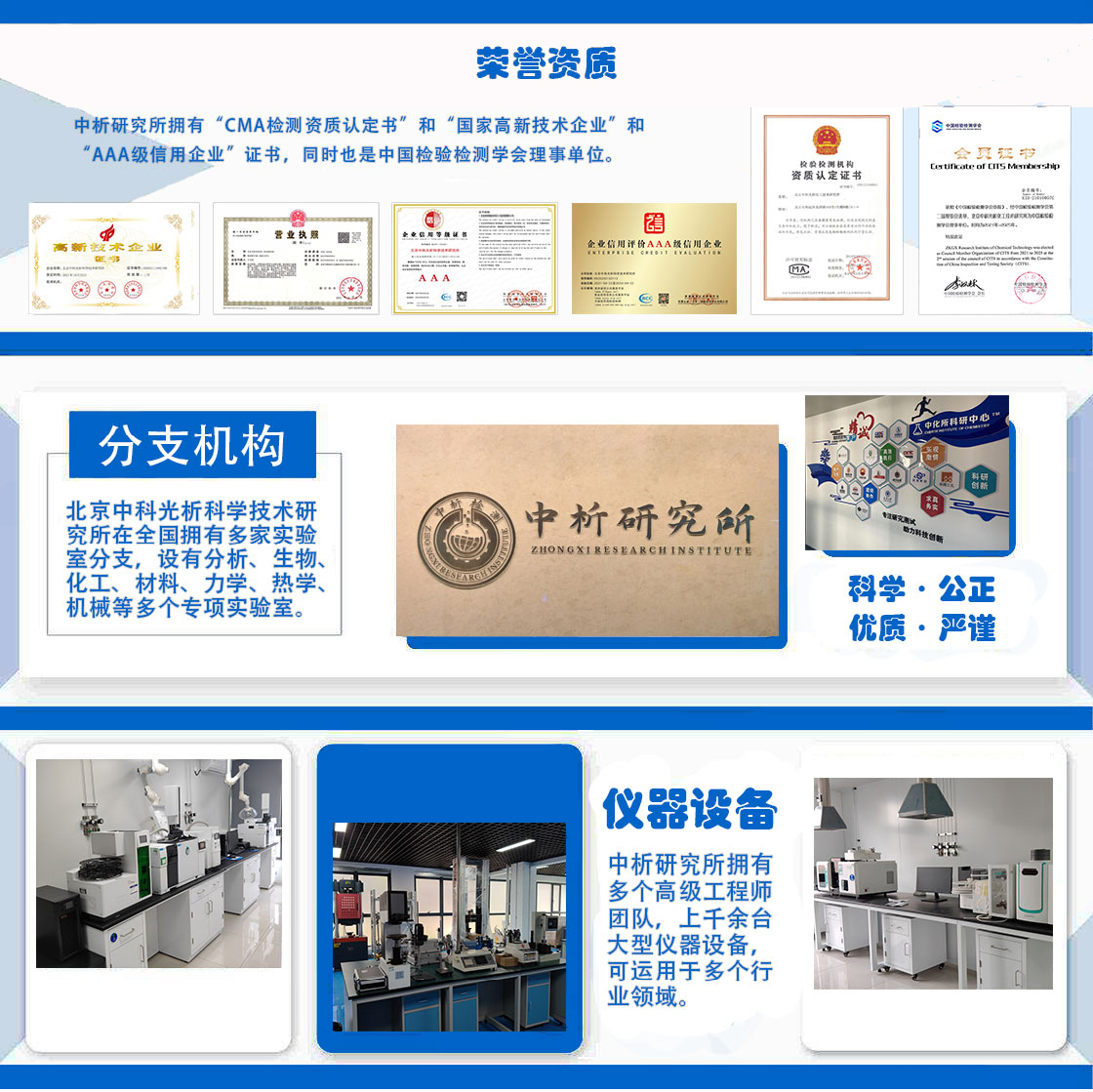
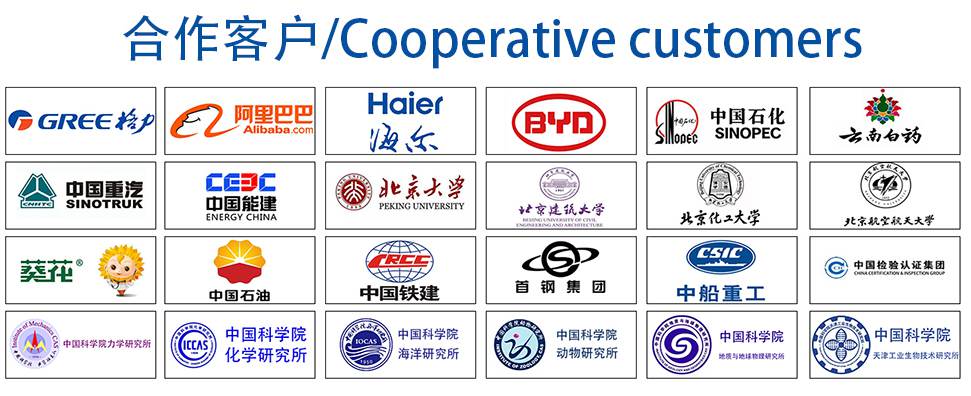