溶解乙炔检测
实验室拥有众多大型仪器及各类分析检测设备,研究所长期与各大企业、高校和科研院所保持合作伙伴关系,始终以科学研究为首任,以客户为中心,不断提高自身综合检测能力和水平,致力于成为全国科学材料研发领域服务平台。
立即咨询溶解乙炔检测的重要性及核心项目解析
溶解乙炔作为一种广泛应用于金属切割、焊接和化学合成领域的高效工业气体,因其易燃易爆特性及储存方式的特殊性,在生产、运输和使用过程中需进行严格的质量与安全检测。乙炔以丙酮为溶剂溶解于多孔材料填充的钢瓶中,这种储存方式虽提高了稳定性,但受工艺条件、储存环境及设备老化等因素影响,仍可能产生纯度不足、杂质超标或容器泄漏等隐患。因此,系统化的检测项目是保障作业安全、防止事故的核心措施。
核心检测项目及执行标准
1. 乙炔纯度检测
通过气相色谱法或红外光谱分析,测定乙炔体积浓度是否达到GB 6819-2004要求的≥98%(体积分数)。纯度不足可能导致燃烧效率下降,同时杂质气体(如氧气、甲烷)的混入会显著增加爆炸风险。
2. 水分含量测定
采用露点仪或卡尔费休法检测水分含量,要求每升乙炔中水分≤1.0g。过量水分会降低丙酮对乙炔的溶解性能,导致钢瓶内压力异常升高,同时加速设备腐蚀。
3. 硫化氢与磷化氢检测
使用电化学传感器或吸收比色法检测有毒杂质,其中硫化氢≤0.1%(体积分数)、磷化氢≤0.2%(体积分数)。这些酸性气体会腐蚀管路系统,且在焊接时可能污染金属表面。
4. 丙酮溶剂残留量分析
通过蒸馏称重法或色谱法监控丙酮含量,确保每升乙炔中丙酮≥35g。溶剂不足会导致乙炔析出结晶,引发钢瓶内部压力剧增甚至爆裂。
5. 气体溶解稳定性测试
在40℃恒温条件下观察钢瓶压力变化,要求24小时内压力波动不超过0.2MPa。异常波动表明溶解体系失效,需立即停止使用。
6. 钢瓶密封性与压力检测
采用氦质谱检漏仪检测瓶体密封性,同时使用经校验的压力表监测工作压力是否处于1.5-2.5MPa安全区间。钢瓶定期需进行3年周期性的水压试验。
检测频率与风险控制策略
新充装钢瓶需实施全项目检测,常规使用中每批次抽样检测比例不低于10%。对于检测不合格产品,应立即启动追溯机制,排查生产环节中的温度控制、填料质量或净化系统故障。检测数据应同步录入物联网监测平台,实现全生命周期质量跟踪。
通过上述系统化检测体系的实施,可有效降低溶解乙炔在使用过程中的燃烧、爆炸及中毒风险,为工业安全生产提供可靠保障。同时,操作人员需定期接受检测技术培训,确保检测结果的准确性和时效性。
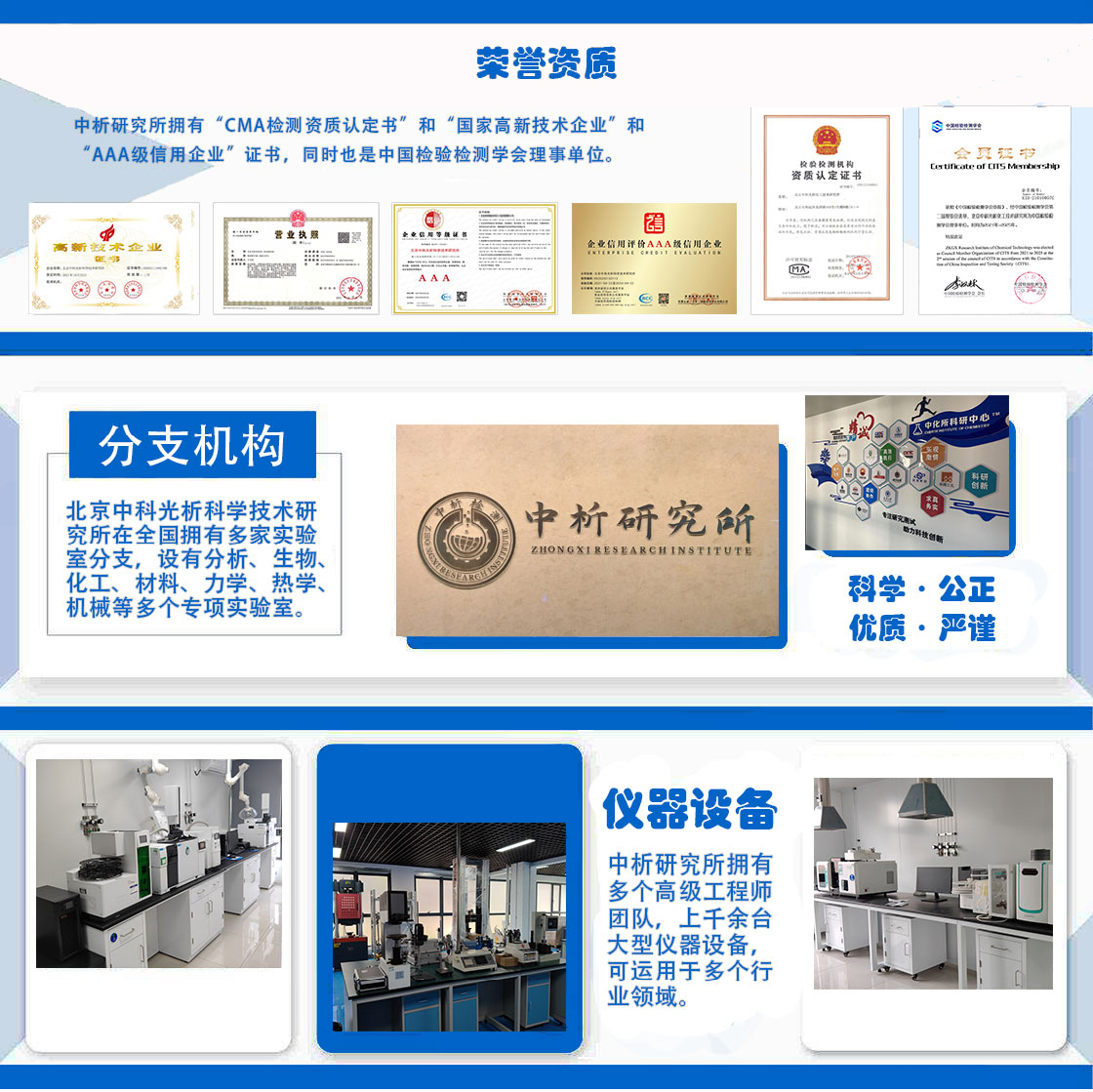
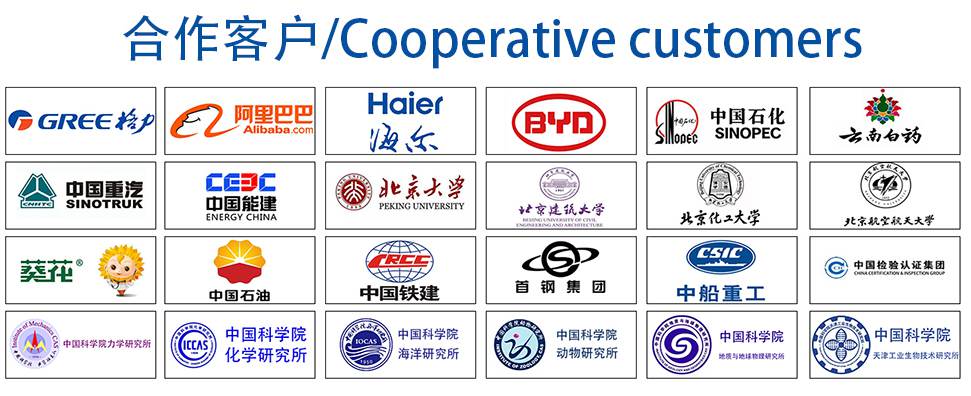