车辆电子/电气零部件检测的重要性与背景
随着汽车智能化、电动化的发展,电子/电气零部件已成为现代车辆的核心组成部分,涵盖从传感器、控制单元到高压电池系统的众多领域。这些零部件的性能与可靠性直接关系到车辆的安全性、功能稳定性及用户驾驶体验。因此,严格的质量检测流程成为汽车制造和零部件供应的关键环节。通过科学规范的检测手段,可以识别潜在的设计缺陷、材料问题或制造误差,确保零部件在复杂工况下的耐久性和抗干扰能力,同时满足国际和行业标准的合规性要求。
主要检测项目
车辆电子/电气零部件的检测项目主要包括以下几类: 1. **电气性能测试**:如电压/电流稳定性、绝缘电阻、耐压强度等; 2. **环境适应性测试**:涵盖高低温循环、湿热老化、振动冲击及盐雾腐蚀等模拟极端条件; 3. **电磁兼容性(EMC)测试**:评估零部件在电磁干扰下的抗扰度及自身辐射水平; 4. **功能可靠性测试**:如长时间运行稳定性、故障模式诊断及软件逻辑验证; 5. **安全性测试**:包括短路保护、过载防护及阻燃性能等。
常用检测仪器与设备
为实现上述检测目标,需依赖专业仪器设备: - **高精度示波器与万用表**:用于实时监测电压、电流波形及参数; - **环境试验箱**:模拟温度(-40℃至150℃)、湿度(10%~98% RH)及振动条件; - **EMC测试系统**:包括暗室、频谱分析仪及射频信号发生器; - **绝缘耐压测试仪**:检测绝缘材料在高压下的击穿风险; - **振动台与冲击试验机**:验证机械结构强度与抗疲劳性。
检测方法及流程
检测流程通常分为以下阶段: 1. **预处理**:根据标准(如ISO 16750)对零部件进行环境适应性调节; 2. **参数校准**:使用标准源对仪器进行精度验证; 3. **分项测试**:按功能模块逐项执行电气、环境及EMC测试; 4. **数据记录与分析**:通过自动化软件采集数据并生成报告; 5. **失效分析与改进**:针对测试中发现的异常进行根因追溯与设计优化。
核心检测标准
检测标准的制定依据包括国际法规和行业规范: - **ISO 7637**:道路车辆电气瞬态传导干扰测试标准; - **AEC-Q系列**:汽车电子委员会制定的可靠性验证标准; - **SAE J1113**:电磁兼容性测试规范; - **GB/T 28046**:中国国标中的环境试验要求; - **UN R100/R136**:电动汽车高压系统安全与EMC法规。
总结与趋势展望
随着新能源与自动驾驶技术的普及,车辆电子/电气零部件的检测需求将持续升级。未来,检测技术将向智能化(如AI故障诊断)、高精度(纳米级元件分析)及标准化统一方向演进,以确保供应链的质量协同与合规性。
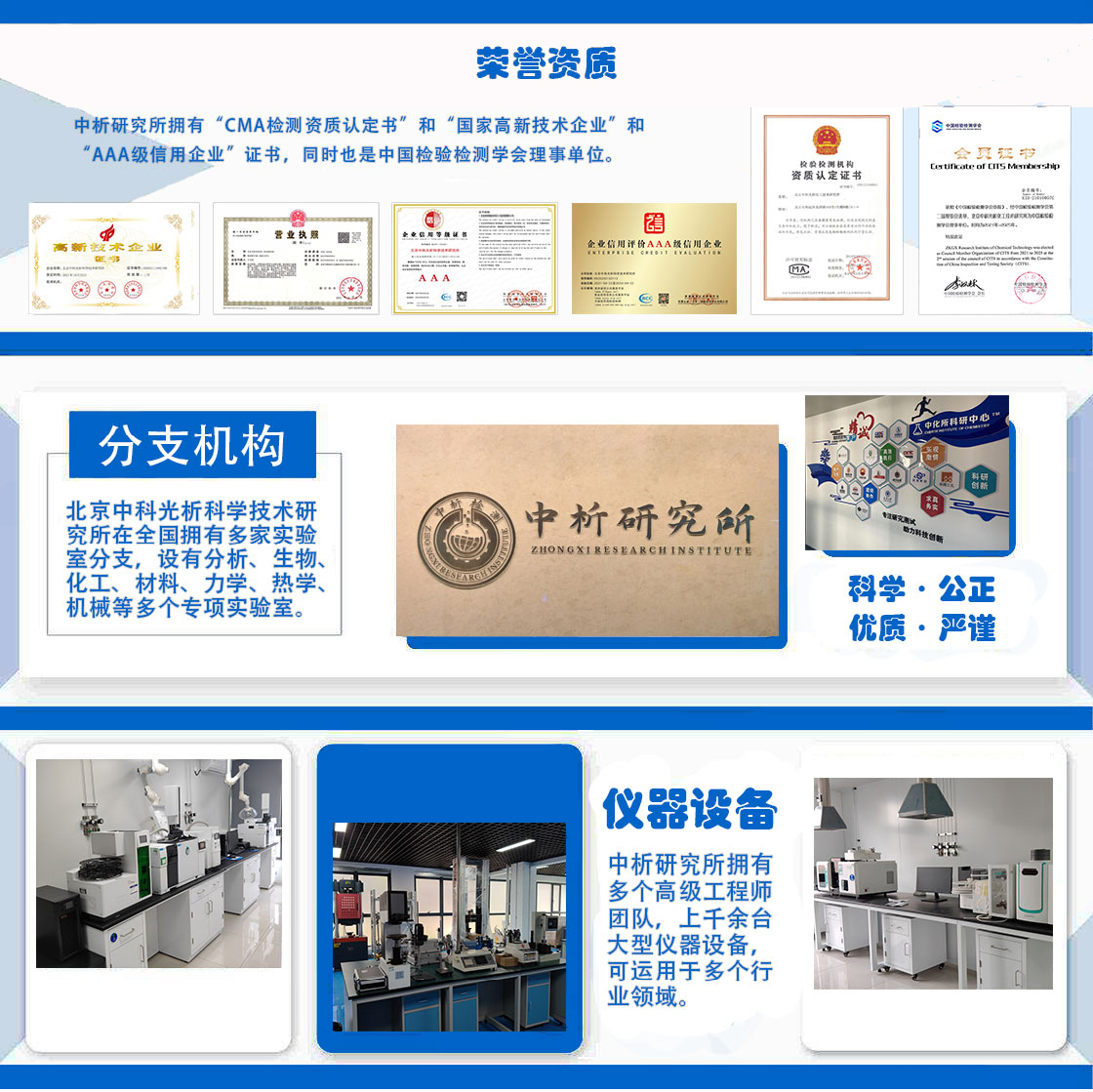
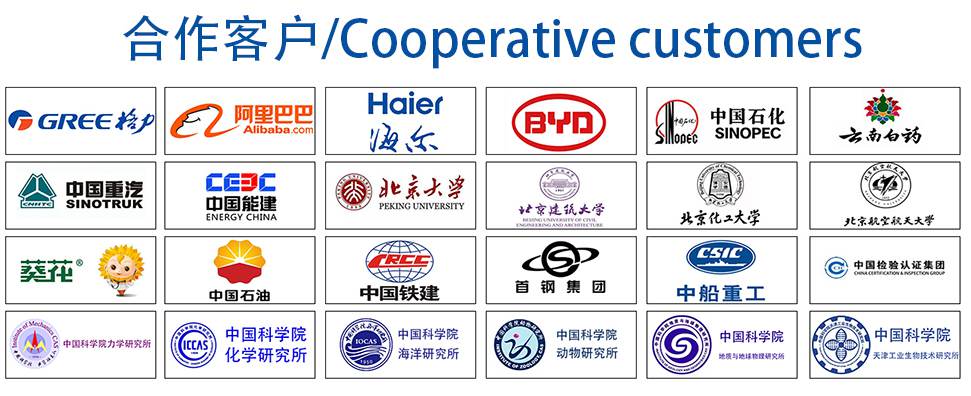