防静电周转容器检测:关键项目与方法解析
一、防静电性能检测项目
-
- 检测意义:表面电阻直接反映容器表面的导电能力,是评估防静电性能的核心指标。电阻值过高可能导致静电无法及时导泄。
- 测试方法: 使用表面电阻测试仪(如符合ASTM D257标准),在容器表面施加一定电压(通常100V或500V),测量电极间的电阻值。
- 合格标准: 根据IEC 61340-5-1标准,防静电材料表面电阻应在 104∼1011 Ω104∼1011Ω 范围内;导静电材料则需低于 104 Ω104Ω。
-
- 检测意义:评估材料内部的导电性能,防止静电在容器内部积累。
- 测试方法: 采用体积电阻测试仪,将电极嵌入材料内部一定深度,测量电阻值。
- 合格标准:通常要求与表面电阻一致,具体需参照GB/T 1410或ISO 3915标准。
-
- 检测意义:衡量材料消散静电荷的速度,时间越短说明防静电性能越优。
- 测试方法: 使用静电衰减测试仪(如符合MIL-STD-3010C标准),对样品充电至±1000V以上,记录电压衰减至10%所需时间。
- 合格标准:一般要求衰减时间≤2秒(依据ANSI/ESD STM12.1)。
-
- 检测意义:模拟实际使用中容器与其他材料摩擦产生的静电压。
- 测试方法: 在摩擦试验机上以标准速度(如30次/分钟)摩擦容器表面,用静电场计测量产生的电压。
- 合格标准:通常要求≤100V,严苛场景需≤50V(如半导体行业)。
二、物理性能及环境适应性检测
-
- 项目包括:抗冲击性(如跌落测试)、堆码强度、耐压性。
- 标准方法:依据GB/T 4857系列,模拟满载状态下的跌落或堆码(如高度1.2m自由跌落3次无破裂)。
-
- 检测意义:表面涂层磨损可能导致防静电性能下降。
- 测试方法:使用Taber耐磨试验机,以规定转速和负重摩擦表面,检测磨损后的电阻值变化。
-
- 检测意义:验证极端温湿度环境下防静电性能的稳定性。
- 测试方法:将容器置于高温(如60℃)、低温(-20℃)、高湿(90% RH)环境中循环48小时,测试电阻值变化率(通常要求≤20%)。
三、其他专项检测
-
- 通过电化学阻抗谱(EIS)或显微镜观察涂层厚度及分布。
-
- 对于带接地装置的容器,需测试接地电阻(一般≤1Ω)。
-
- 接触腐蚀性液体后,测试表面电阻是否稳定。
四、检测频率与注意事项
- 检测周期:建议每6-12个月进行一次全面检测,高频使用场景需缩短周期。
- 机构选择:优先选择通过 或ISO 17025认证的实验室。
- 日常维护:避免使用酒精等溶剂擦拭表面,防止破坏防静电涂层。
五、结语
- IEC 61340-5-1:2016《静电防护-电子器件通用标准》
- ANSI/ESD S20.20-2021《静电放电控制方案》
- GB/T 32367-2015《防静电周转容器通用技术规范》
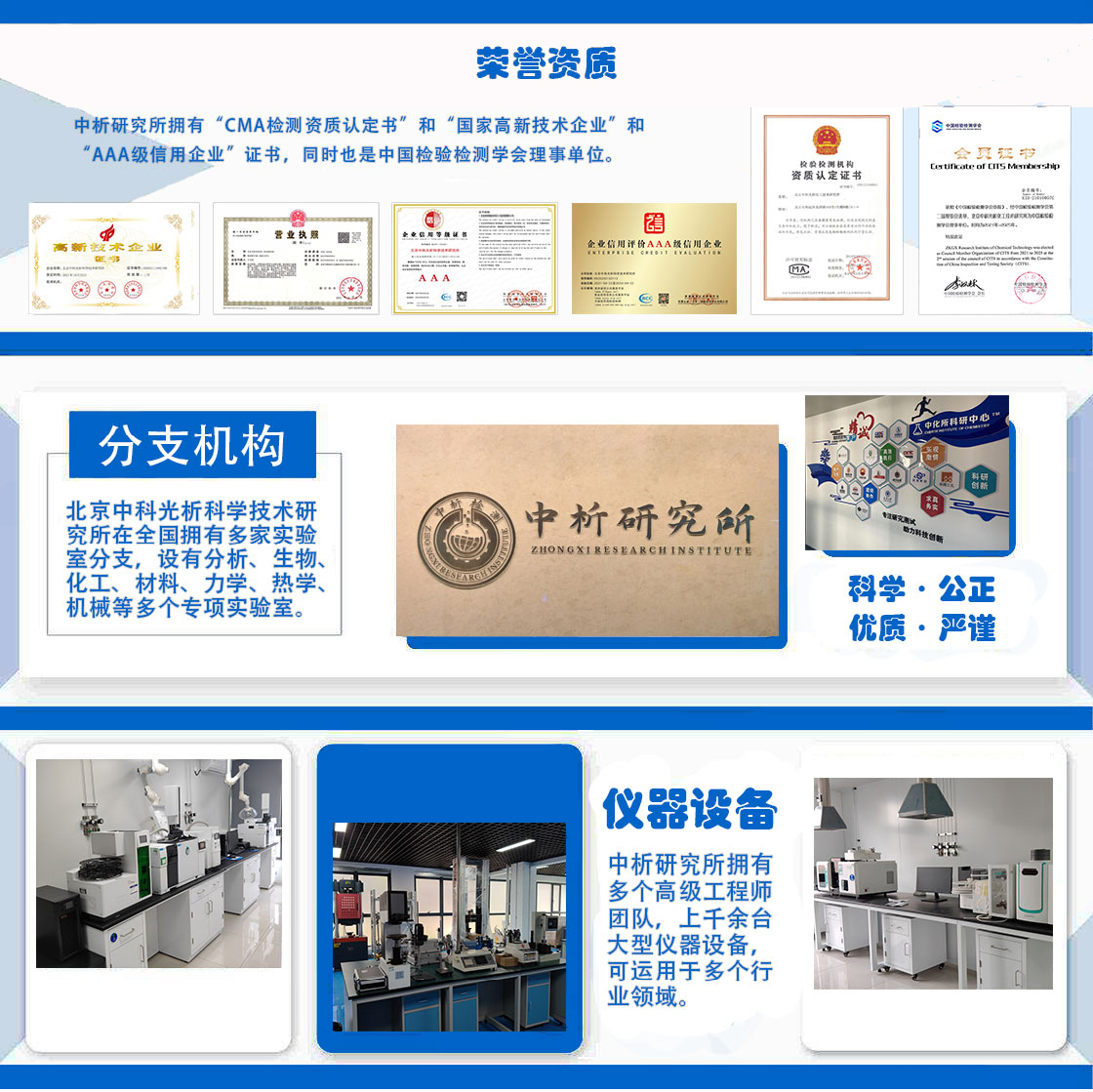
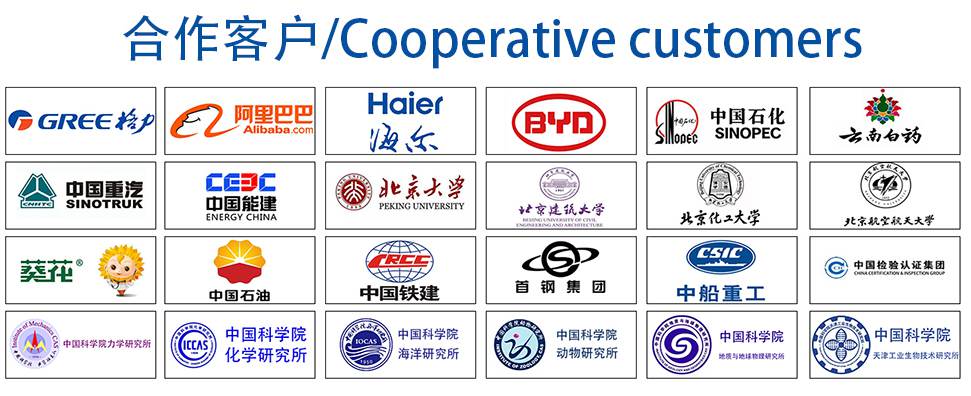
材料实验室
热门检测
264
221
200
208
203
207
217
208
219
222
208
207
211
209
201
200
213
204
211
208
推荐检测
联系电话
400-635-0567