电动汽车用动力锂离子蓄电池检测:关键项目与技术解析
一、安全性能检测:极端工况下的防护屏障
-
- 方法:对电池进行超过额定电压的充电(如1.5倍)或放电至截止电压以下,观察是否发生泄漏、起火或爆炸。
- 标准:GB 38031要求电池在过充至终止电压的120%时保持稳定至少1小时。
-
- 方法:模拟电池正负极直接短路(外部电阻≤5mΩ),记录温升和表面形变情况。
- 要求:最高温度不超过150℃,且不起火、不爆炸。
-
- 挤压测试:以≥100kN压力挤压电池至变形量达30%,观察热失控反应。
- 针刺测试:用直径3-8mm钢针以25mm/s速度贯穿电池,监测是否引发连锁反应。
-
- 温度冲击:在-40℃至85℃间快速交替循环,验证密封性与结构稳定性。
- 热失控扩散(模组级别):通过局部加热触发单电池热失控,评估整个模组的阻燃设计。
二、电性能检测:核心参数的量化评估
-
- 测试方法:在25℃下以标准倍率(如1C)充放电,计算实际容量与标称值的偏差(国标要求≤5%)。
- 能量密度:通过质量/体积比计算,主流三元电池可达250Wh/kg以上。
-
- 交流法:注入1kHz交流电,测量欧姆内阻(反映极耳焊接质量)。
- 直流法:通过阶跃电流法获取极化内阻,评估电极材料活性。
-
- 库仑效率:循环中放电容量与充电容量的比值,优质电池首效应≥95%。
-
- 静置法:电池满电后在25℃下存放28天,容量损失应<5%。
三、环境适应性检测:复杂工况下的可靠性验证
-
- 低温放电:-20℃下以1C放电,容量保持率需≥70%(GB/T 31486)。
- 高温存储:55℃下满电存放7天,容量恢复率≥90%。
-
- 条件:温度40℃±2℃,湿度95%RH,循环12次(总计48小时),验证密封性与绝缘性能。
-
- 振动谱:模拟路面随机振动,频率5-200Hz,时长3小时。
- 冲击强度:半正弦波冲击加速度25g,脉冲宽度15ms。
四、寿命评估:全生命周期衰减分析
-
- 方法:以1C充放电循环至容量降至80%为止,优质电池需≥2000次(磷酸铁锂可达4000次)。
- SOH评估:通过微分电压分析(dQ/dV)追踪电极材料衰减。
-
- 加速老化模型:基于阿伦尼乌斯公式,通过高温存储(如45℃)推算常温下的寿命衰减曲线。
五、前沿检测技术与发展趋势
-
- 采用X射线衍射(XRD)、扫描电镜(SEM)实时观测电池内部结构变化。
-
- 利用机器学习分析历史数据,预测电池剩余寿命(RUL)和故障风险。
-
- GB 38031-2020新增“热扩散”要求,强制模组层级30分钟热失控预警时间。
结语
上一篇:番木瓜检测下一篇:民用航空X射线安全检查设备检测
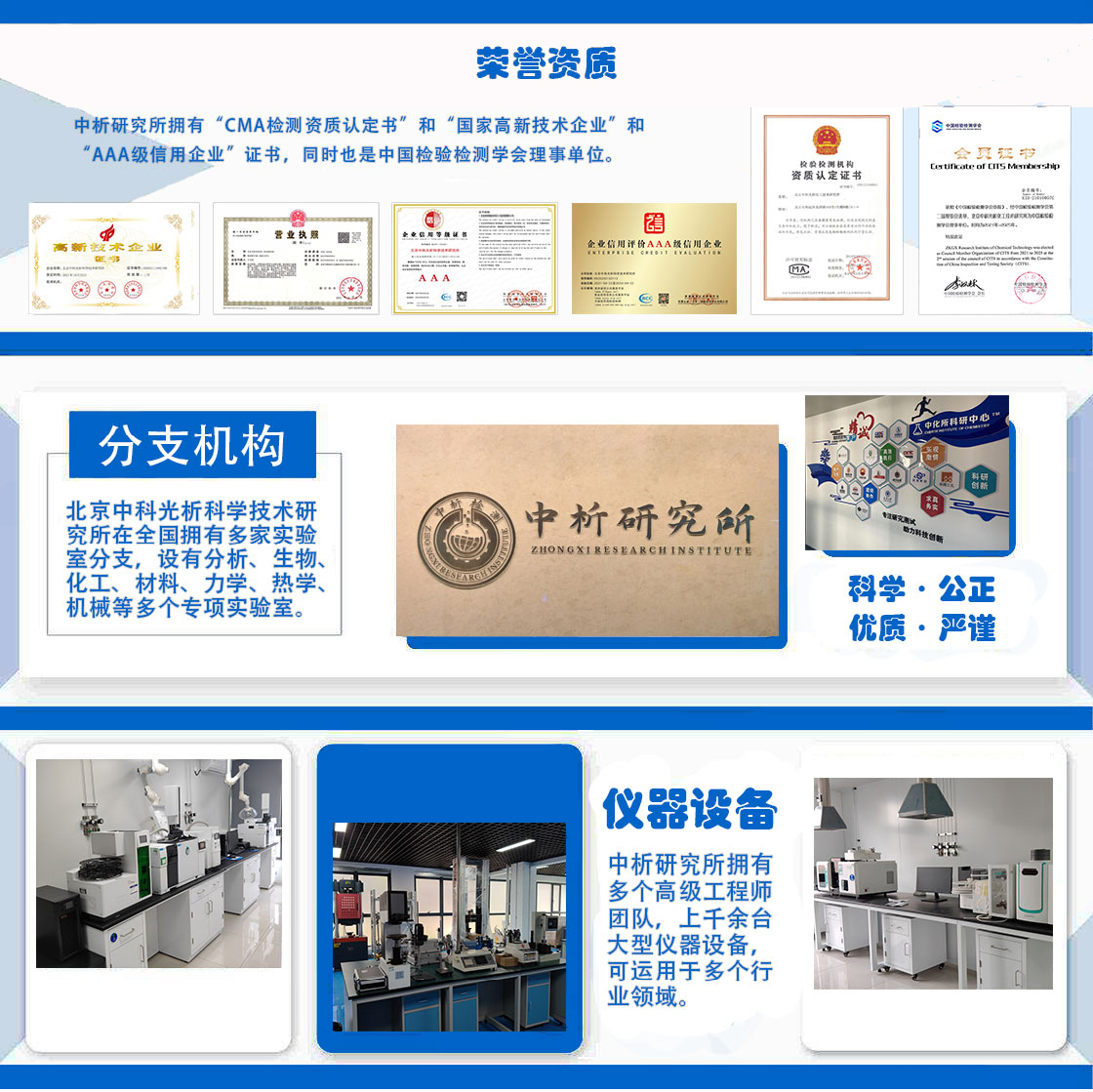
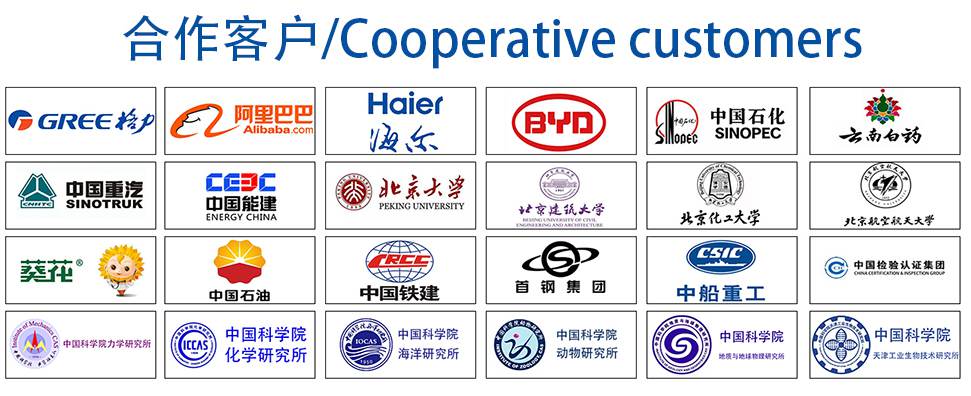
材料实验室
热门检测
280
234
209
217
216
221
230
224
234
233
221
221
223
222
214
212
227
213
227
221
推荐检测
联系电话
400-635-0567