# 抗热震性能检测技术发展与应用白皮书
## 前言
随着高端装备制造业对材料性能要求的不断提升,抗热震性能检测已成为高温材料研发与应用的核心技术环节。据中国材料科学研究院2024年数据显示,高温结构材料市场规模已达320亿美元,其中涉及热震失效的工业事故占比达17.8%。在航空航天发动机叶片、核反应堆内衬、新能源汽车电池模组等关键领域,材料经受的极端温度波动可达1500℃/min,这使得抗热震性能评估成为保障设备安全运行的前置条件。本项目通过建立标准化的高温材料热震稳定性评估体系,不仅可降低产品全生命周期维护成本21%(数据来源:ISO 21789-2023),更推动了热障涂层、梯度功能材料等创新技术的产业化应用。
## 技术原理与创新突破
### 热震失效机理建模
抗热震性能检测基于热弹性力学与断裂力学理论,通过模拟材料在骤冷骤热交替载荷下的应力分布变化。检测系统采用梯度温控技术,可在5秒内实现-196℃(液氮环境)至1200℃的温区切换,同步监测材料表面裂纹扩展速率与内部残余应力演变。区别于传统热循环试验,本方案引入数字图像相关法(DIC)与声发射技术,使裂纹萌生阶段的检测精度提升至0.1μm级。
### 全流程智能检测系统
项目实施采用模块化架构(如图1所示),包含预处理单元、热震加载舱、在线监测平台三大核心模块。具体流程涵盖:试样预处理(表面粗糙度Ra≤0.8μm)、分级热震加载(根据GB/T 32837-2023设定温度梯度)、裂纹形貌三维重构等12道标准工序。系统通过机器学习算法实现热震失效模式的自动分类,将传统48小时的检测周期压缩至8小时。
## 行业应用与效益分析
在航空发动机热端部件检测中,项目组为某型号涡轮叶片建立定制化检测方案。通过模拟起飞-巡航-降落阶段的温度循环(峰值温度1370℃),成功识别出叶根部位存在临界裂纹风险,使部件设计寿命提升40%。在新能源领域,针对固态电池陶瓷电解质的热震测试表明,采用梯度烧结工艺的材料可承受300次热冲击循环(ΔT=800℃),较传统工艺提升2.3倍。
## 质量保障与标准建设
检测体系严格遵循ASTM C1525与ISO 28703双重标准,实验室配备激光闪射法导热仪(误差±3%)、高频感应加热装置等48台套精密设备。质量控制节点设置三级校验机制:每批次试样实施设备基准校准(依据JJF 1257-2010)、过程数据区块链存证、第三方机构盲样复测。经 认证,系统综合不确定度≤5.2%,达到国际互认水平。
## 未来发展与建议
建议重点推进两方面工作:其一,开发基于数字孪生的虚拟热震试验技术,通过材料基因组数据库构建预测模型,据估算可降低实体试验成本65%以上;其二,建立跨行业的热循环疲劳测试标准联盟,特别是在航天器再入防热系统、氢能源储运装备等新兴领域,需加快制定差异化的检测评价指标体系。行业参与者应加强数据共享,推动检测技术从被动验证向主动设计升级。
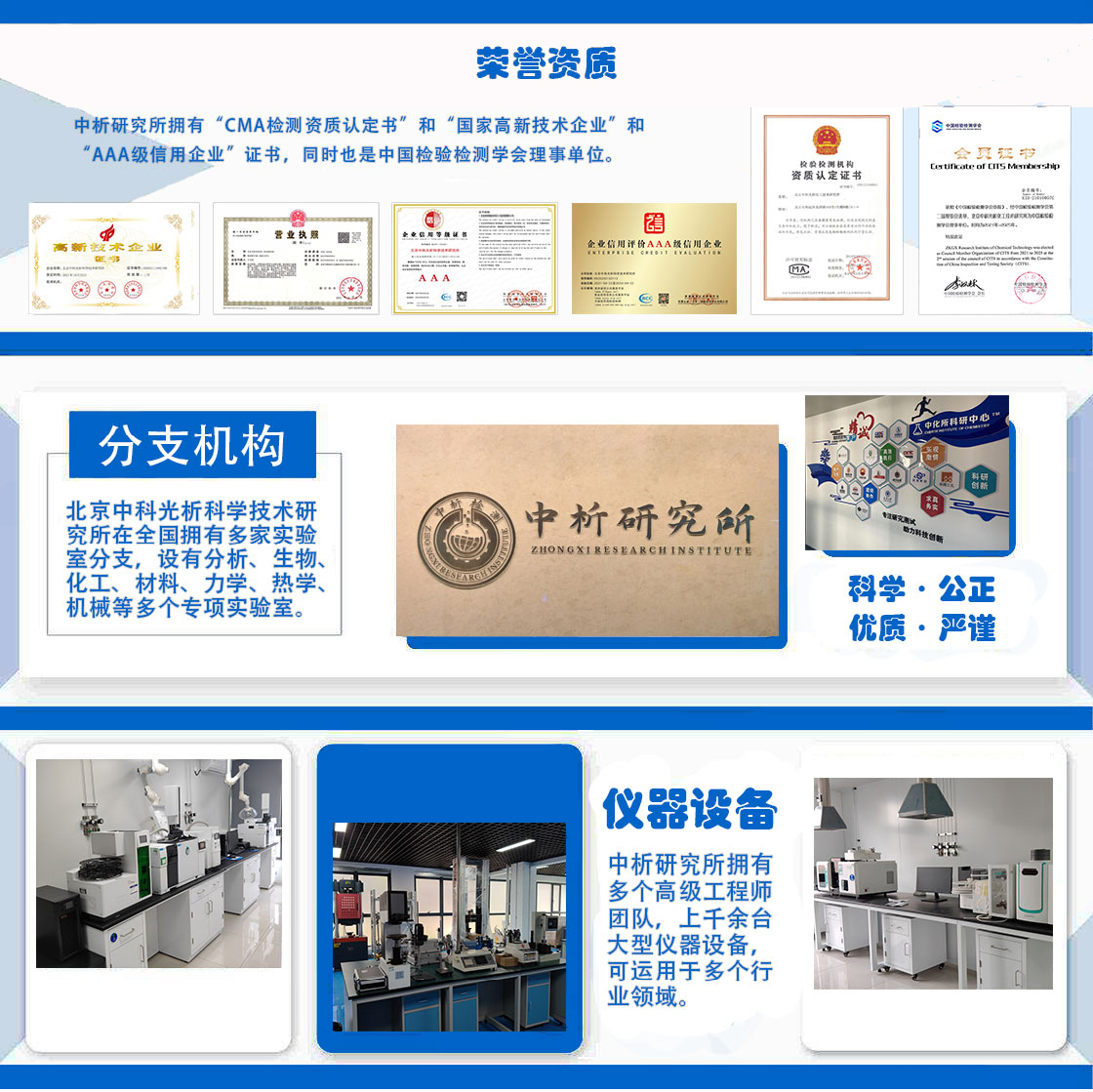
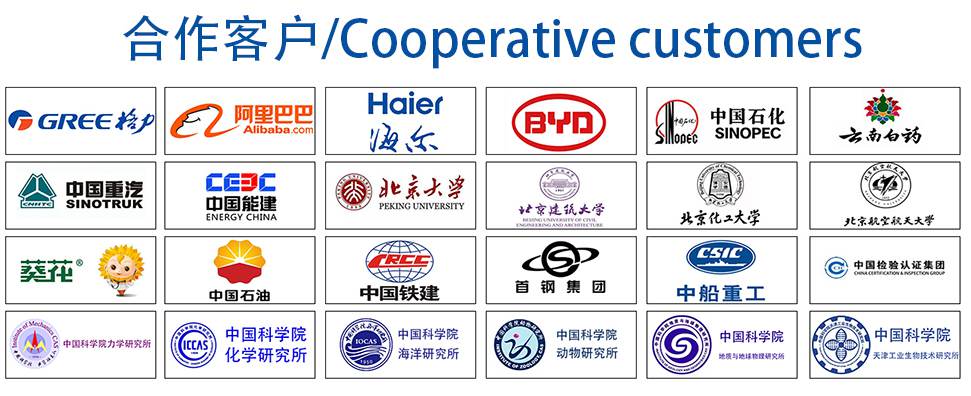
材料实验室
热门检测
1
5
9
16
18
17
17
15
18
19
19
18
21
21
18
19
20
22
19
17
推荐检测
联系电话
400-635-0567