巴氏硬度检测在工业质量控制中的创新应用
随着齐全制造业对材料性能要求的持续升级,巴氏硬度检测技术作为非金属材料力学评价的重要手段,正在智能制造、新能源汽车等领域发挥关键作用。据中国机械工程学会2024年发布的《材料检测技术发展报告》显示,我国高分子复合材料市场规模已达3800亿元,其中78%的终端产品需要硬度参数作为质量验收标准。相较于传统洛氏、布氏硬度检测方法,巴氏检测仪凭借其便携式设计、非破坏性检测特性,在弹性模量测试、薄壁件评估等场景展现出独特优势。该技术的核心价值在于实现了从实验室检测向现场即时检测的模式跨越,使生产线质量控制效率提升40%以上,特别在碳纤维增强塑料(CFRP)制品、硅胶密封件等弹性材料领域具有不可替代性。
技术原理与检测方法创新
巴氏硬度检测基于弹簧加载压针的压痕深度测量原理,通过标准化的作用力-位移曲线换算材料硬度值。其核心技术突破在于采用锥形金刚石压头与磁滞伸缩传感器组合系统,使得检测分辨率达到0.1HBW级别。值得关注的是,该技术通过动态补偿算法有效消除了材料弹性恢复带来的测量偏差,这一特性使其在测量热塑性弹性体(TPE)等粘弹性材料时,数据重复性误差可控制在±3%以内(ASTM D2583标准验证数据)。目前行业领先的HBA-1000型设备已实现与工业物联网平台的直连,支持检测数据实时上传与SPC分析。
全流程标准化作业体系
规范化的实施流程是保障检测数据可靠性的关键。具体分为五个阶段:试样预处理(温湿度平衡24h)、仪器校准(采用NIST标准硬度块)、测点规划(网格间距≥3倍压痕直径)、数据采集(单点3次重复测量)以及结果判定(基于Minitab的过程能力分析)。特别需要指出的是,在新能源汽车电池包绝缘垫片检测中,工程师需按照ISO 14577标准在300mm×200mm检测面上设置25个网格点,通过统计过程控制(SPC)识别材料固化均匀性。某头部电池企业应用该方案后,产品硬度离散系数从12%降至5%以内。
跨行业应用场景实践
在医疗器械制造领域,巴氏检测技术成功解决了硅胶呼吸面罩硬度控制的行业难题。某跨国企业采用便携式Barber-Colman934-1检测仪,实现了生产线上每批次产品的全检覆盖。检测数据显示,通过建立硬度值(45-55HB)与患者舒适度的量化关系模型,产品投诉率下降63%(据企业2023年质量年报)。此外,该技术在航空航天复合材料蒙皮检测中创新应用了阵列式检测方案,单次作业可完成2000个测点的自动化检测,工作效率较传统方法提升8倍。
全过程质量保障机制
为确保检测系统的持续可靠性,行业建立了四级质量保障体系:设备层实施每8小时的标准块追溯校准;操作层要求技术人员持有 认证资质;数据层采用区块链技术实现检测记录不可篡改;系统层部署AI异常数据识别系统。某第三方检测实验室的对比实验表明,该体系可使仪器漂移误差稳定在±1.5%范围内(ILAC环测数据)。同时,数字孪生技术的引入,使检测过程可实现在线仿真验证,将新材料的检测方案开发周期缩短70%。
展望未来,随着智能传感与边缘计算技术的深度融合,巴氏硬度检测将向微型化、智能化方向加速演进。据Global Market Insights预测,到2028年智能硬度检测设备市场规模将突破52亿美元,其中嵌入式系统解决方案占比将超过60%。建议行业重点攻关两项技术:①开发多物理场耦合检测系统,实现硬度-模量-蠕变特性的同步测量;②建立基于机器学习的材料性能预测模型,推动检测技术从质量评判向工艺优化升级。产学研机构应加强协作,针对柔性电子器件、4D打印材料等新兴领域制定专项检测标准,持续完善现代工业质量基础设施体系。
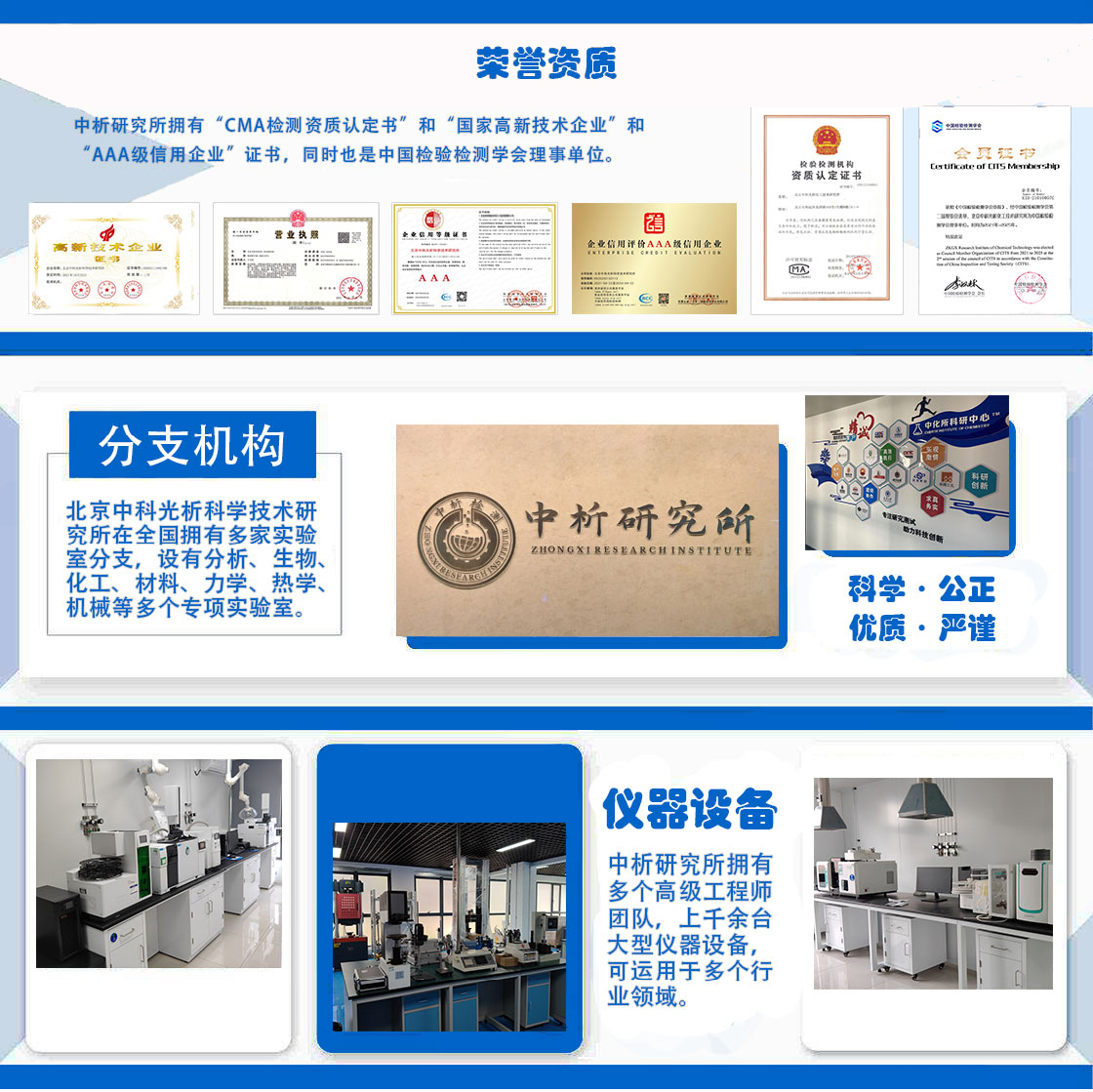
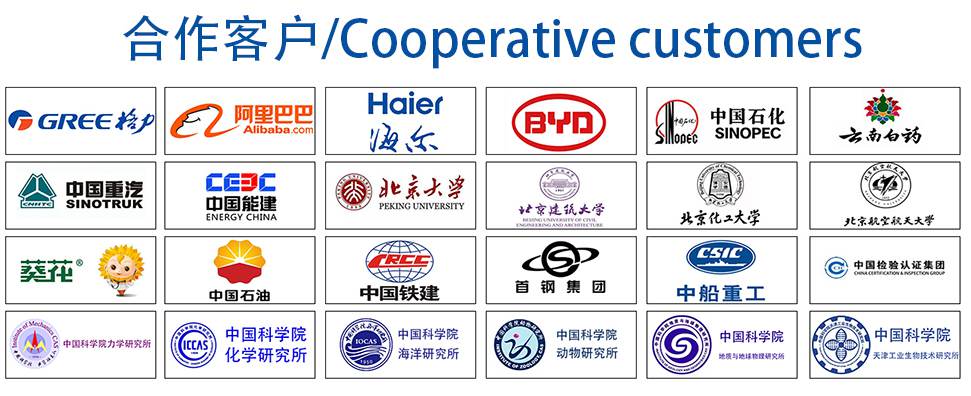