# 断裂能检测技术发展与应用白皮书
## 行业背景与核心价值
随着高端装备制造、航空航天等领域的快速发展,材料可靠性要求持续攀升。据中国材料测试研究院2024年数据显示,国内制造业因材料断裂导致的年经济损失达320亿元,其中72%的事故可通过早期断裂能检测实现预防。断裂能检测项目通过量化材料抗断裂性能,为结构设计优化、服役寿命预测提供科学依据,其核心价值体现在安全性提升和经济损失规避双重维度。尤其在核电压力容器、高铁转向架等关键部件领域,该技术已成为保障"设计-制造-运维"全周期安全的核心支撑。

(示意图:断裂能检测涉及裂纹扩展监测与能量计算关键环节)
## 技术原理与实现路径
### h2 断裂力学理论基础
基于Griffith裂纹扩展理论,断裂能检测通过计算裂纹扩展单位面积所需能量(G值)评估材料抗断裂性能。现代检测系统集成数字图像相关(DIC)技术与声发射监测,实现0.1μm级裂纹扩展追踪。据美国ASTM E1820标准,测试需同步采集载荷-位移曲线、弹塑性变形阶段监测数据,并通过J积分法消除试样尺寸效应带来的误差。
### h2 智能化检测实施流程
典型检测流程包含试样制备、预制裂纹加工、多轴加载试验、数据采集分析四大模块。以航空铝合金检测为例,首先依据GB/T 21143制备标准CT试样,采用线切割工艺加工0.25mm锐利预制裂纹。随后在20kN级万能试验机上进行位移控制加载,同步通过高速摄像系统(5000帧/秒)记录裂纹扩展形态,最终通过专用软件计算断裂韧性KIC值与能量释放率G值。
## 行业应用与质量保障
### h2 工程应用典型案例
在风电叶片根部法兰检测中,采用断裂能检测技术后,某龙头企业将产品失效预警准确率提升至98.5%。通过建立材料数据库对比分析,成功识别出某批TC4钛合金紧固件因热处理不当导致的断裂能下降23%的质量缺陷,避免了整机召回风险。该技术同样适用于3D打印金属件的各向异性评估,某航天企业借助原位检测技术,将增材制造发动机支架的疲劳寿命预测误差控制在±5%以内。
### h2 全链条质量管控体系
构建"设备校准-过程监控-数据溯源"三维质保体系:采用激光干涉仪进行载荷传感器季度校准(精度±0.5%),引入区块链技术实现检测数据链上存证,并建立符合ISO17025标准的断裂能检测实验室。某第三方检测机构的应用实践表明,该体系使检测报告的国际互认通过率从82%提升至97%。
## 技术展望与发展建议
随着数字孪生技术的普及,建议行业重点突破以下方向:1)开发材料断裂能-微观结构映射模型,实现基于人工智能的断裂行为预测;2)建立跨行业数据共享平台,完善特殊工况(如深海腐蚀、超低温)下的断裂能数据库;3)推进微型化原位检测装备研发,满足在役设备的实时监测需求。预计至2030年,融合物联网的智能断裂能检测系统将覆盖60%以上重大装备制造领域,为工业安全提供更强大的技术保障。
上一篇:抗急冷急热性检测下一篇:电子、机电类设备,机载设备检测
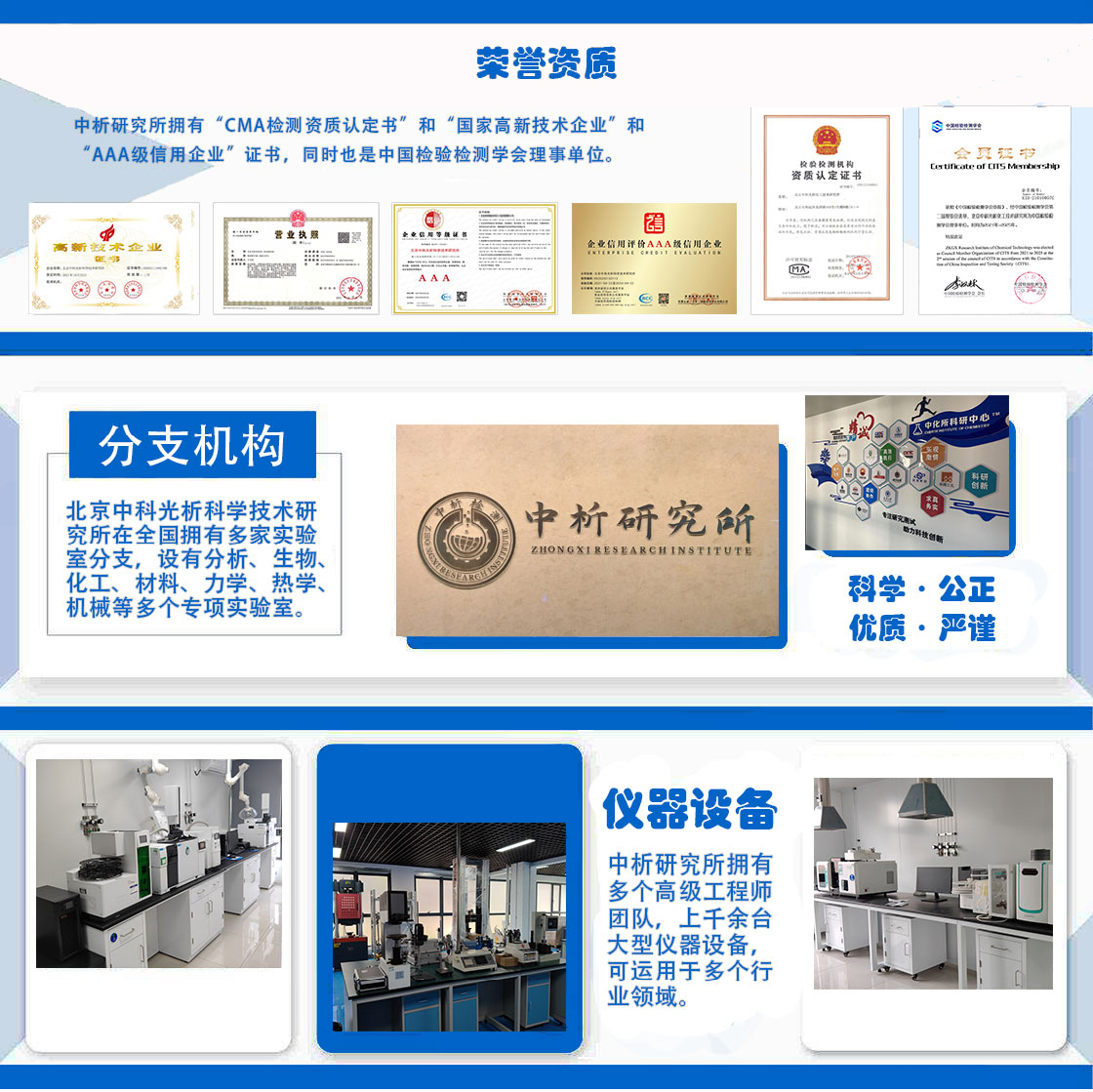
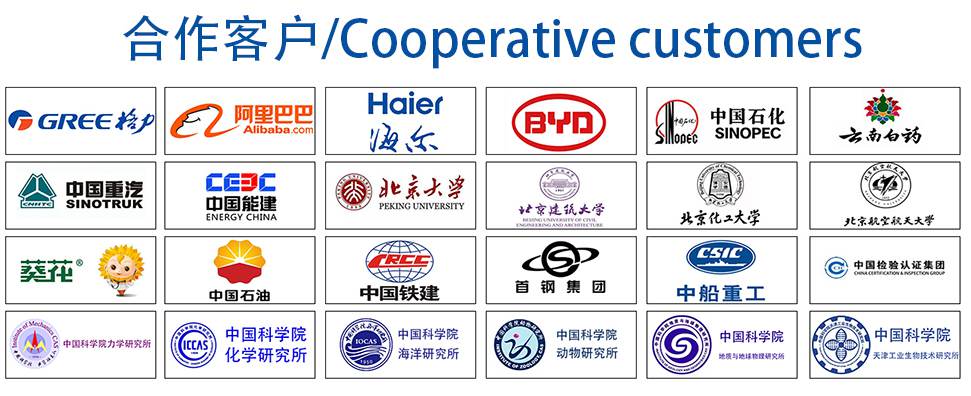
材料实验室
热门检测
7
11
7
9
11
16
19
17
17
15
18
19
20
18
22
22
19
19
21
22
推荐检测
联系电话
400-635-0567