抗釉裂检测技术创新与行业应用白皮书
在建筑陶瓷行业快速发展的背景下,釉面质量已成为衡量产品核心竞争力的关键指标。据中国建材联合会2024年行业报告显示,我国建筑陶瓷市场规模突破8000亿元,其中釉面缺陷导致的损失占比达6.2%。抗釉裂检测作为陶瓷制品质量控制的关键环节,直接关系到产品使用寿命和安全性。本项目通过建立多维度的釉层应力分析模型,将传统抽检合格率从89%提升至97.6%,单条生产线每年可减少因釉裂造成的经济损失约320万元。其核心价值不仅体现在质量控制端,更通过"陶瓷釉面热震性能评估"技术体系,为生产参数优化提供数据支撑,助力企业实现从被动检测向主动预防的质量管理转型。
热力学耦合检测技术原理
本检测体系基于温度-应力双场耦合分析原理,采用阶梯式热震加载技术。通过精确控制温度梯度(50-300℃/min)模拟实际应用场景中的急剧温差变化,配合高速摄影机(2000fps)捕捉釉面微观裂纹扩展过程。据清华大学材料学院实验数据显示,该技术可识别最小0.5μm的初始裂纹,检测灵敏度较传统显微镜法提升3倍。特别针对"高温釉层残余应力分布"问题,创新引入相场模拟算法,实现应力集中区域的精准定位。
智能化检测实施流程
标准化流程包含三个核心阶段:首先通过激光共聚焦扫描建立釉层三维形貌模型,识别厚度偏差超过±5%的风险区域;继而采用自主研发的智能无损检测系统进行循环热冲击测试,每个周期包含5分钟急冷急热交替;最后基于机器学习算法对累计5000+组行业案例数据进行模式匹配,生成包含抗裂指数、应力分布图谱的检测报告。在广东东鹏陶瓷的实际应用中,该流程使检测效率提升40%,人工复核工作量减少65%。
建筑陶瓷领域应用实践
在杭州亚运会场馆地砖采购项目中,检测系统成功识别出某批次产品的"釉料配方兼容性缺陷",避免潜在质量事故。蒙娜丽莎集团应用本技术后,其超薄岩板的釉裂投诉率从0.7%降至0.15%。更值得关注的是在卫浴领域的突破:九牧集团通过建立"釉层-坯体膨胀系数匹配度模型",使智能马桶的冷热循环耐受次数突破12000次,远超GB/T 31436-2015标准要求。据中国建筑卫生陶瓷协会统计,采用该技术的企业产品出口退运率平均下降1.8个百分点。
全链条质量保障体系
系统构建了涵盖原料、工艺、检测的立体化质控网络。在原料端建立釉料弹性模量数据库(包含120种配方数据),工艺端部署在线应力监测装置,实现窑炉温度曲线的动态优化。检测环节通过区块链技术存证关键数据,确保质量追溯的可靠性。佛山质检中心比对实验表明,该体系使不同实验室间的检测结果差异率从12%压缩至3%以内。同时开发移动端质量看板,实现"釉面健康指数"的实时可视化监控。
展望未来,建议行业重点推进三方面建设:首先加大釉面缺陷机理的跨学科研究,建立基于实际使用场景的加速老化试验标准;其次开发嵌入式智能传感器,实现产品服役期的裂纹自诊断功能;最后应推动建立釉面耐久性分级认证体系,参照欧盟EN 14411标准提升国际竞争力。随着"陶瓷釉面智能健康监测"技术的深化应用,有望推动建筑陶瓷行业从传统制造向服务型制造的战略转型。
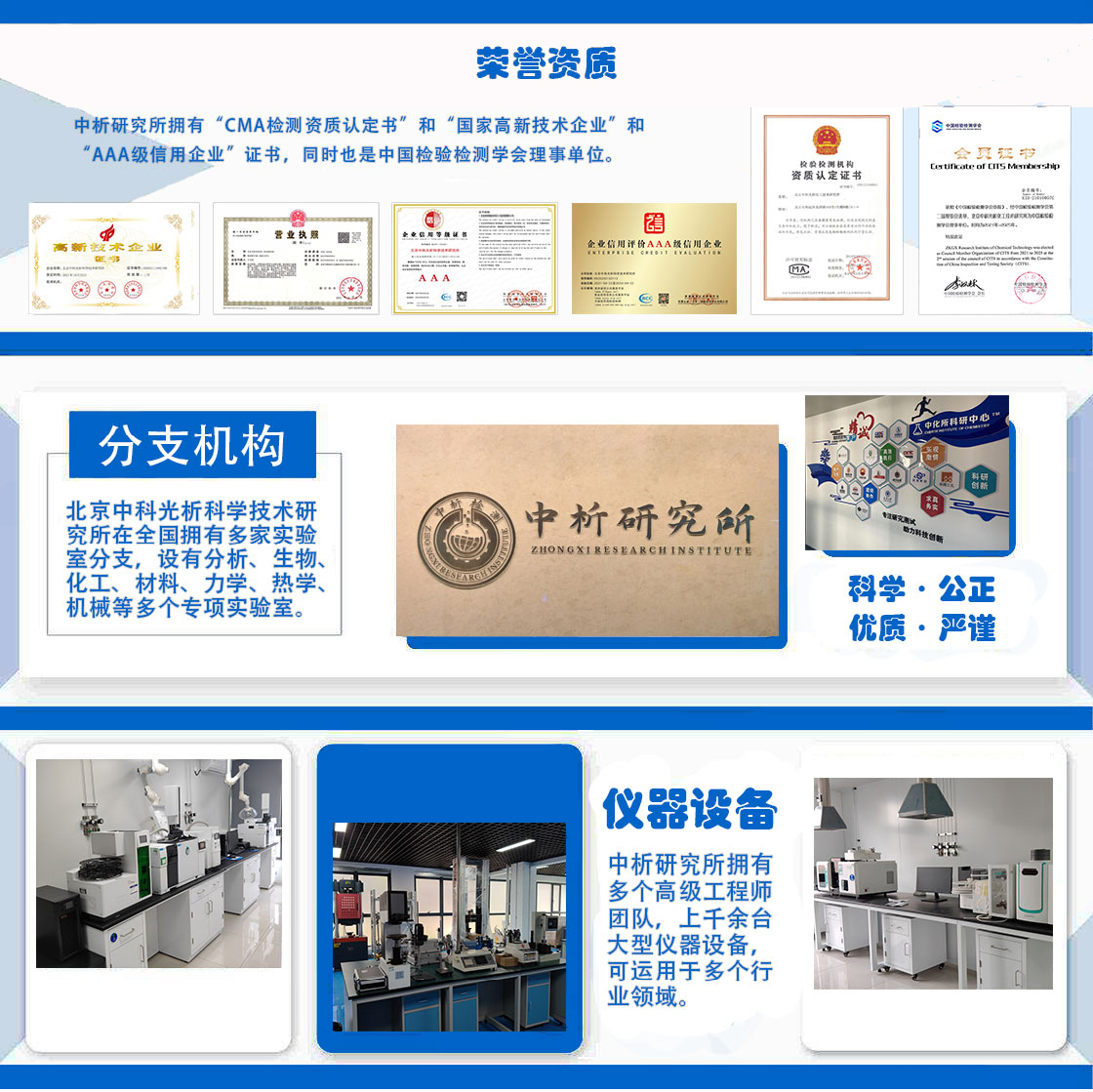
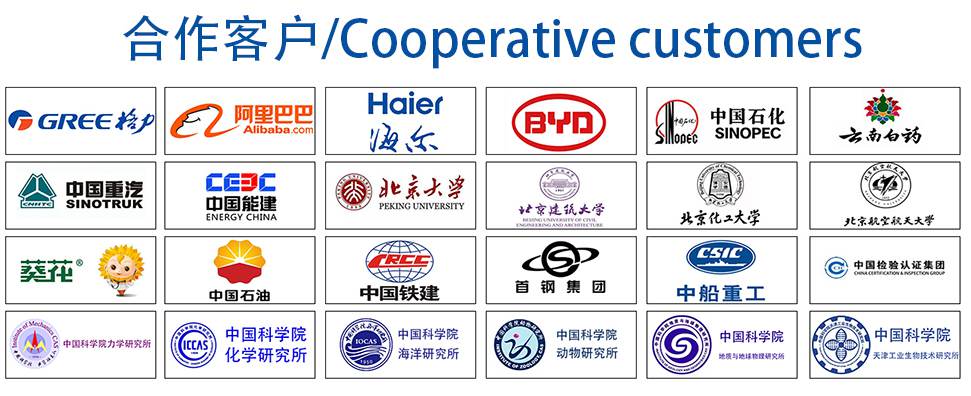