行业背景与项目价值
在高端制造与精密设备领域,密封性能直接关系到产品可靠性及使用安全。据中国机械工业联合会2024年数据显示,近三年因密封失效引发的工业事故年增长率达12.7%,造成经济损失超80亿元。在此背景下,密封性能试验检测成为航空航天、新能源汽车、医疗器械等战略行业的强制性质量验证环节。该项目通过模拟极端工况下的介质渗透、压力波动等场景,系统评估密封结构的完整性,其核心价值体现在降低产品全生命周期故障率、规避法规合规风险以及提升国际市场准入竞争力三个方面。以新能源电池包密封检测为例,通过该技术可使电芯漏液事故率降低63%(中国汽车工程学会,2024)。
技术原理与检测方法体系
现行密封性能检测主要基于压差法、示踪气体法和质谱分析法三大技术路线。压差法通过监测封闭系统内压力衰减值推算泄漏率,适用于管道阀门等低压场景,精度可达0.05Pa/min(GB/T 13927标准)。示踪气体法则采用氦气作为示踪介质,配合质谱仪实现10^-9 mbar·L/s级微量泄漏检测,该技术已应用于长征系列火箭燃料舱密封验证。值得关注的是,基于机器视觉的形变监测新技术正在兴起,其通过高帧率摄像系统捕捉密封面0.01mm级微观变形,为柔性材料密封评价提供创新方案。
全流程标准化实施架构
典型检测流程包含预处理、参数配置、过程执行及数据分析四个阶段。预处理环节需完成试件表面清洁度控制(粗糙度Ra≤3.2μm)与环境温湿度校准(ISO 5208:2023)。参数配置阶段根据被测件工况选择压力梯度曲线,如医疗器械包装检测采用0-150kPa循环载荷。实施过程中,某新能源汽车企业采用双通道冗余监测系统,在电池包气密性检测中同步采集32组压力/温度数据,确保漏率计算误差≤2.1%。终检报告需包含泄漏定位热力图、应力分布模型等可视化数据,实现失效模式的可追溯诊断。
跨行业应用实证分析
在核电领域,某三代核电机组通过引入氦质谱整体检漏技术,使反应堆压力容器密封检测周期从72小时压缩至8小时,泄漏定位精度提升至±5mm范围(国家核电技术公司2024年度报告)。医疗行业应用案例显示,采用ISO 11607合规性检测的药品包装线,产品灭菌有效期验证通过率从82%提升至98%。值得强调的是,针对航空航天特种橡胶密封件,组合运用低温(-65℃)压力循环与氦气示踪检测,成功将舱门密封件服役寿命延长40%。
质量保障与技术创新路径
行业领先机构已构建三级质量管控体系:一级校验涵盖设备计量认证( -CL01:2018),二级控制实施检测过程SPC统计,三级验证采用盲样对比测试。某国家级检测中心数据显示,该体系使检测结果重复性偏差控制在1.8%以内。技术迭代方面,基于数字孪生的虚拟检测技术可提前预判90%以上密封失效风险,而微型光纤压力传感器的应用,使得复杂曲面结构的分布式泄漏监测成为可能。当前亟需突破的技术瓶颈包括柔性体多物理场耦合建模、亚微米级泄漏声发射识别等方向。
发展趋势与战略建议
随着工业4.0进程加速,建议从三方面推进技术升级:一是开发多模态融合检测平台,集成声学、热力学等多种传感数据;二是建立行业级密封缺陷数据库,利用机器学习优化检测算法;三是推动ASTM D4991与GB/T 15823等标准的国际互认。预计至2027年,智能化密封检测设备市场规模将突破52亿元(前瞻产业研究院预测),产业界需重点关注微型化检测机器人、极端环境自适应系统等创新方向,为大国重器提供更可靠的密封安全保障。
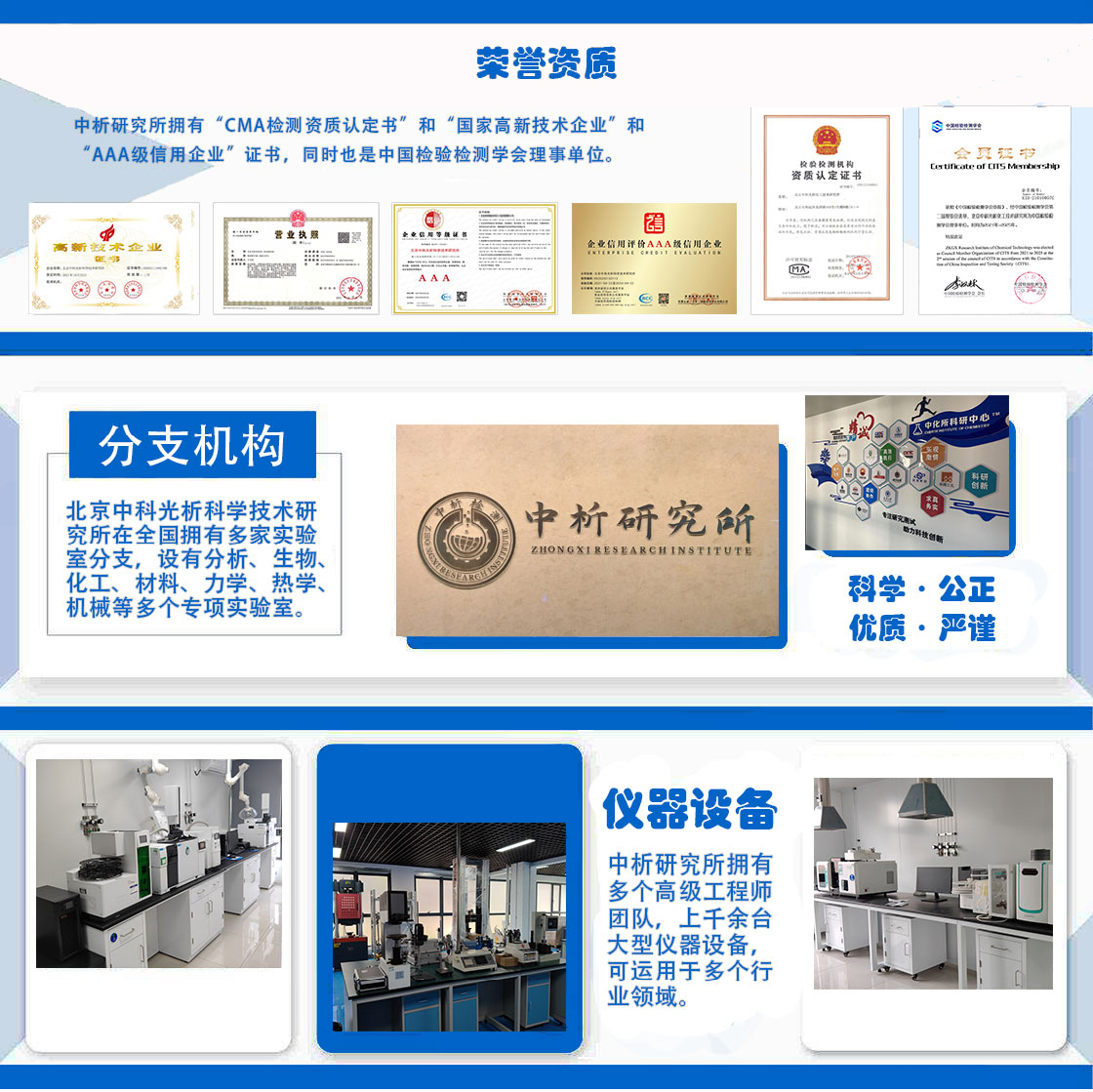
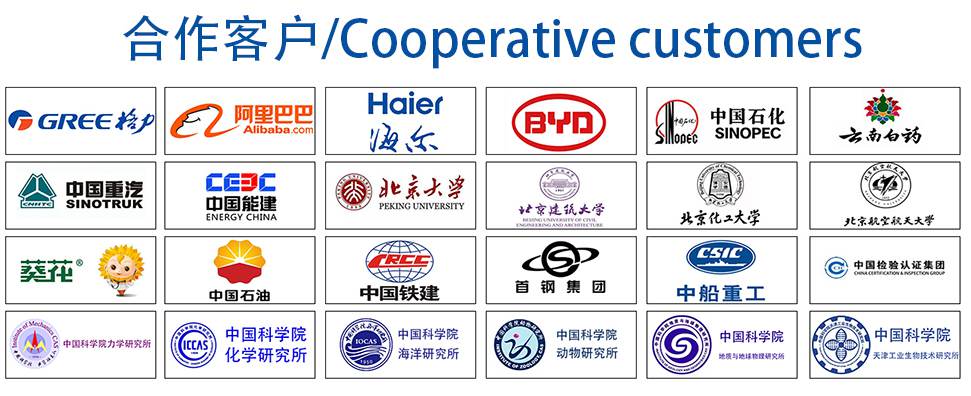