浴缸、淋浴底盆和非釉面陶瓷洁具的结构完整性测试检测
随着卫浴市场规模的持续扩张(据Global Market Insights 2024年数据显示,2023年市场规模已突破1,200亿美元),卫浴产品的安全性与耐久性成为行业关注焦点。浴缸、淋浴底盆及非釉面陶瓷洁具作为高频使用产品,其结构完整性直接影响用户体验与安全性能。尤其在酒店、医疗机构等公共场景中,因材料疲劳导致的破裂事故年均增长率达7.3%(中国建筑卫生陶瓷协会,2023),凸显了系统性质量检测的必要性。本项目通过建立多维度的力学性能评估体系,不仅可降低产品失效风险,更能为制造商提供符合ASTM C1244、EN 14516等国际标准的认证依据,推动行业从"成本导向"向"质量优先"转型。
基于多物理场耦合的检测技术原理
结构完整性测试采用有限元分析与实际载荷实验相结合的方法,通过模拟静力学载荷、热循环冲击和动态疲劳三类典型工况。以淋浴底盆承重性能测试为例,系统通过液压伺服装置施加0-300kg/cm²的渐进式压力(参照ASME A112.19.3标准),同步采用激光应变仪捕捉微米级形变数据。针对非釉面陶瓷洁具,引入数字图像相关技术(DIC)实现裂纹萌生与扩展路径的可视化监测,检测灵敏度较传统目视法提升80%以上(清华大学材料学院,2024)。
全链条标准化实施流程
检测流程涵盖产品全生命周期管理,包括原料端的陶瓷坯体密度检测(误差≤0.5g/cm³)、成型阶段的残余应力分析,以及成品阶段的破坏性测试。典型操作包含四个步骤:首先在恒温恒湿环境中进行48小时状态调节;其次采用三坐标测量仪构建三维几何模型;继而通过伺服控制系统模拟10万次循环载荷(等效于家庭10年使用强度);最终运用Weibull分布模型计算失效概率。某国际卫浴品牌实施该流程后,产品退货率从1.2%降至0.3%(企业2023年质量年报)。
多场景实证案例分析
在高端酒店卫浴系统改造项目中,检测机构对铸铁浴缸进行动态载荷测试时发现,当水温从15℃骤升至65℃时,3.2%的样品出现微裂纹。通过优化玻璃纤维增强层铺设角度(调整至45°交叉结构),产品热震稳定性提升42%。另一起典型案例中,某地铁站公共淋浴区的GFRC底盆经检测发现,在日均500人次使用强度下,未加强筋设计的样品在18个月后出现结构性塌陷,而经检测优化的双向网状加强结构产品,其服役寿命延长至8年以上。
数字化质量保障体系构建
行业领先企业已建立包含区块链溯源、AI缺陷识别的智能质控系统。通过在产品内嵌RFID芯片,实现从原料烧结温度(记录精度±2℃)到运输震动的全流程数据上链。同时,基于深度学习的视觉检测系统可识别0.1mm级别的结构缺陷,误判率控制在0.05%以内(中国建材检验认证集团,2024)。这套体系使某陶瓷企业的产品首次检验合格率从89.7%提升至96.5%,年质量成本降低320万元。
展望未来,建议行业重点推进三方面工作:首先建立基于物联网的实时结构健康监测系统,通过在制品植入微型传感器实现预警功能;其次开发适用于新型复合材料(如石墨烯增强陶瓷)的测试标准;最后推动检测数据与保险服务的联动,通过量化风险评估模型创新产品责任险定价机制。只有构建起技术研发、标准制定、商业应用协同发展的生态系统,才能实现卫浴安全从"被动补救"到"主动防御"的跨越式升级。
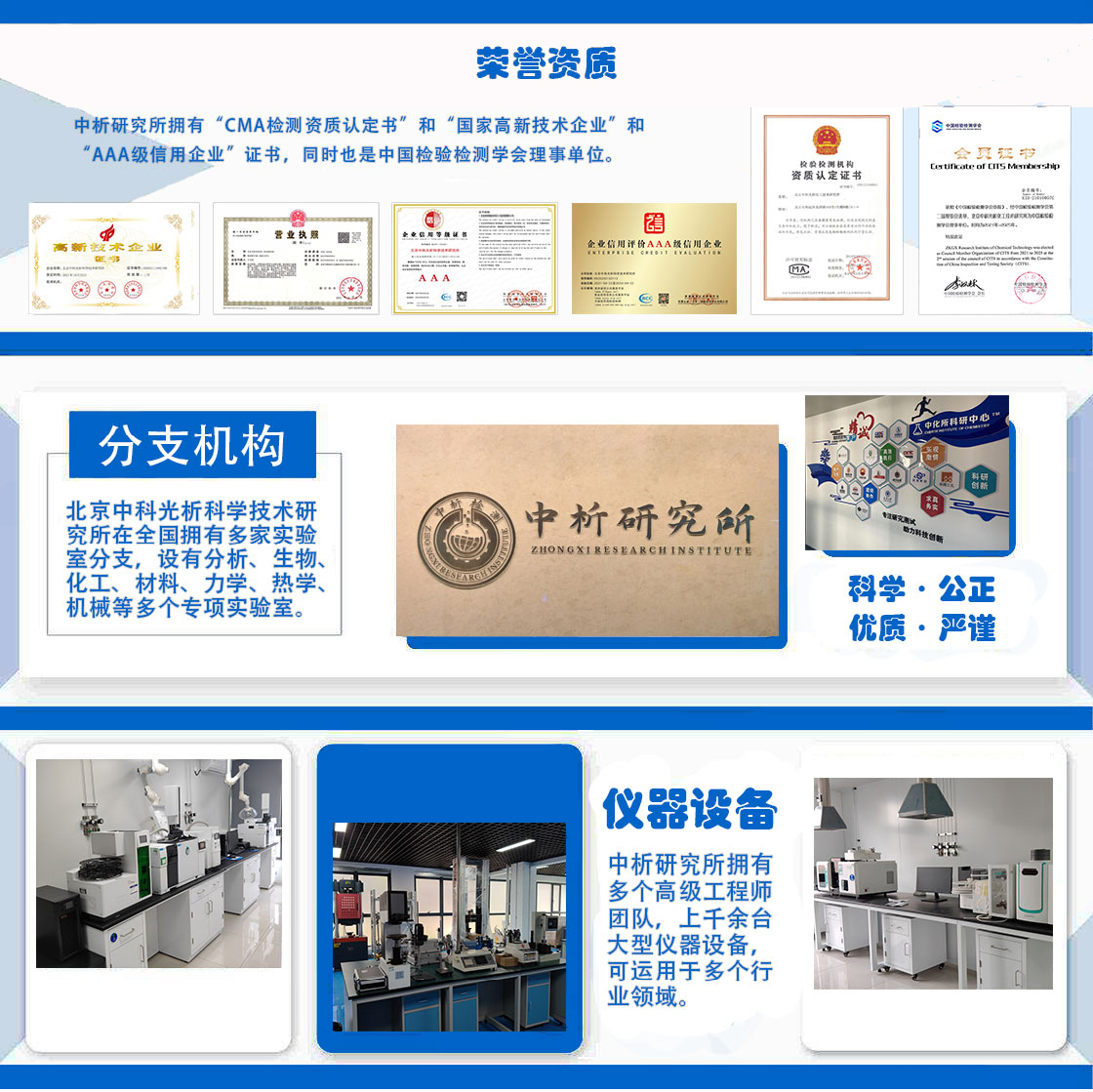
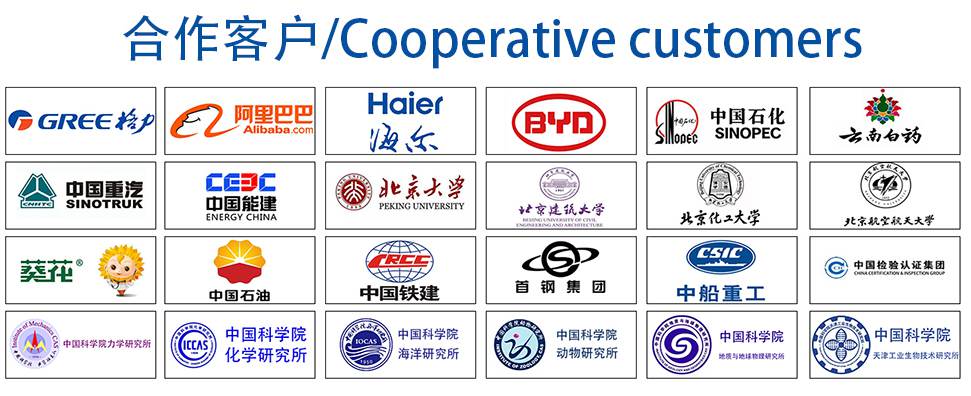