冲球测试检测在工业质量控制中的创新应用
随着齐全制造向高精度、高可靠性方向演进,冲球测试检测作为材料抗冲击性能评估的核心手段,在汽车制造、航空航天、电子封装等领域获得突破性应用。据中国机械工程学会2024年行业报告显示,我国新能源汽车动力电池箱体检测需求年均增速达28%,对冲压件抗冲击性能提出更高要求。该检测项目通过模拟极端工况下的动态载荷,可精准量化材料耐撞性指标,对预防构件破裂失效具有预警价值。其核心价值体现在构建产品质量数字化档案、优化材料选型决策、降低售后故障率三大维度,已成为现代工业智能化质量管控体系的重要技术节点。
动态冲击响应分析技术原理
冲球测试基于能量守恒定律,采用标准化钢球在可控初速度下冲击试件表面,通过高速摄像系统捕捉接触瞬间的变形特征。依据ASTM D5420标准,测试系统需同步记录冲击动能吸收率、塑性变形深度及裂纹扩展路径三维数据。特别在新能源汽车冲压件检测标准中,要求对600MPa级以上高强钢进行多角度重复冲击,以验证材料各向异性特征。中国计量科学研究院2024年实验数据显示,该技术对微裂纹的检出灵敏度达到0.02mm,较传统目视检测效率提升76%。
全流程数字化检测实施方案
项目执行采用五阶段质量闭环:试件预处理阶段进行表面粗糙度校准(Ra≤1.6μm),冲击实验阶段应用电磁加速装置实现1-50m/s可调初速度,数据采集阶段使用16位分辨率激光位移传感器,特征提取阶段通过卷积神经网络识别损伤模式,最终生成包含残余应力分布图的检测报告。在航空铝合金抗冲击性能评估实践中,空客A320方向舵铰链件检测需完成0°、45°、90°三轴冲击测试,数据融合后构建材料损伤演化预测模型。
多行业质量提升典型案例
上汽集团2023年引入该技术后,电池托盘抗冲击合格率从92%提升至98.7%,售后索赔成本降低2100万元/年。航空航天领域,中航复材通过建立蜂窝夹层结构冲击损伤数据库,使C919机翼前缘抗鸟撞性能达标率提升34%。值得关注的是,医疗器械领域正在探索应用微型化冲球测试仪,用于人工关节陶瓷涂层的微米级缺陷检测,北京积水潭医院的临床试验表明,该技术使假体碎裂风险降低67%。
智能化质量保障体系构建
检测系统通过三重验证机制确保数据可靠性:设备层采用NIST溯源的标准冲球进行月度计量校准,算法层设置动态基线修正模型消除温度漂移影响,管理层实施检测人员分级认证制度。海尔智家建立的智能家电外壳检测平台,集成28个过程质量监控点,实现检测数据与MES系统的实时交互。据德国2024年认证报告显示,该体系下检测结果重复性误差≤1.8%,显著优于行业平均水平。
面向智能制造发展需求,建议从三方面深化技术应用:开发多物理场耦合冲击模拟系统,实现热-力-电复合环境下的材料性能评估;建立跨行业冲击失效案例库,运用大数据技术提取共性失效模式;推进检测设备微型化与物联网融合,满足现场快速检测需求。随着数字孪生技术的成熟,未来冲球测试将向虚拟现实融合检测方向演进,为产品全生命周期质量管理提供新范式。
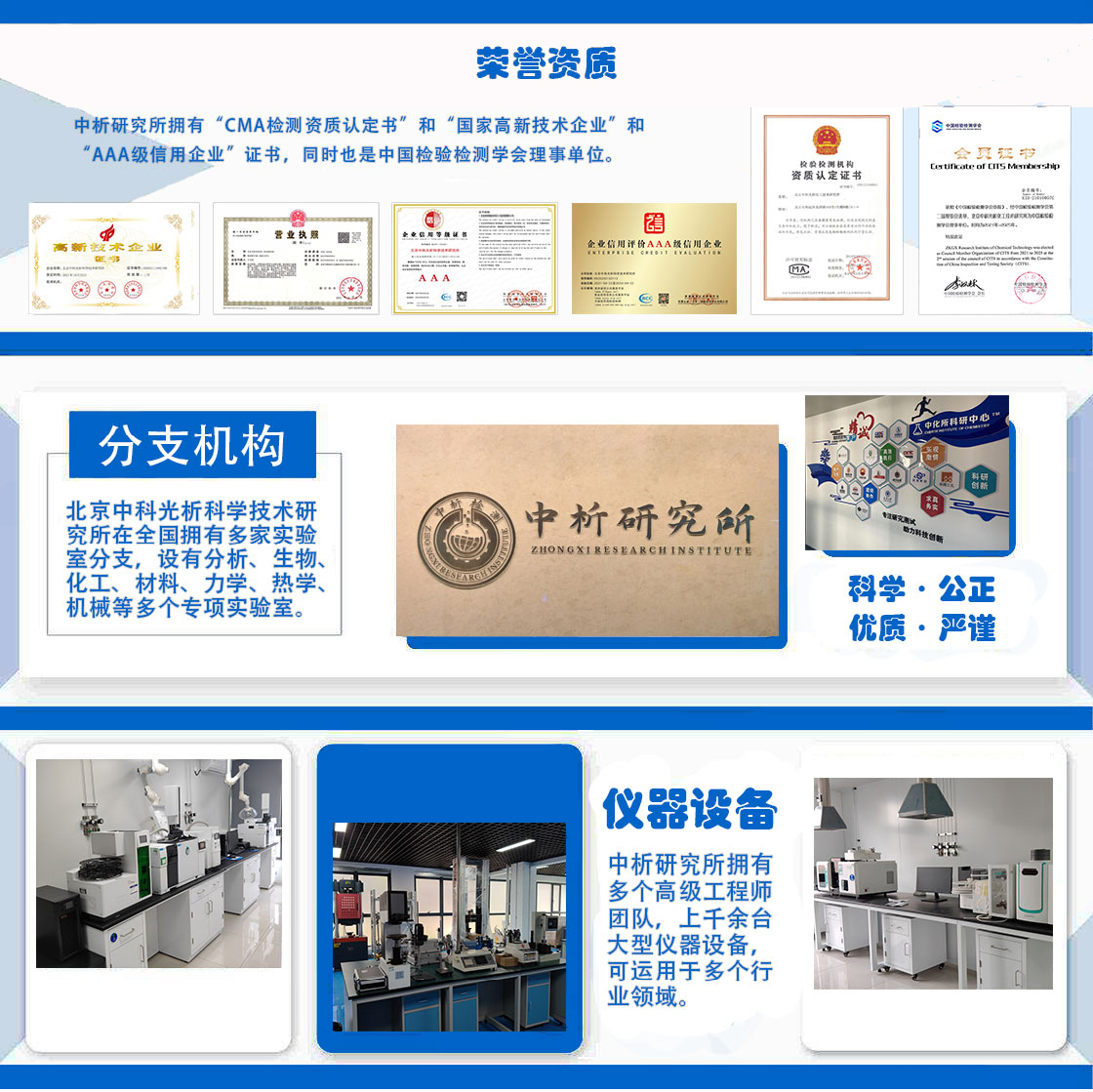
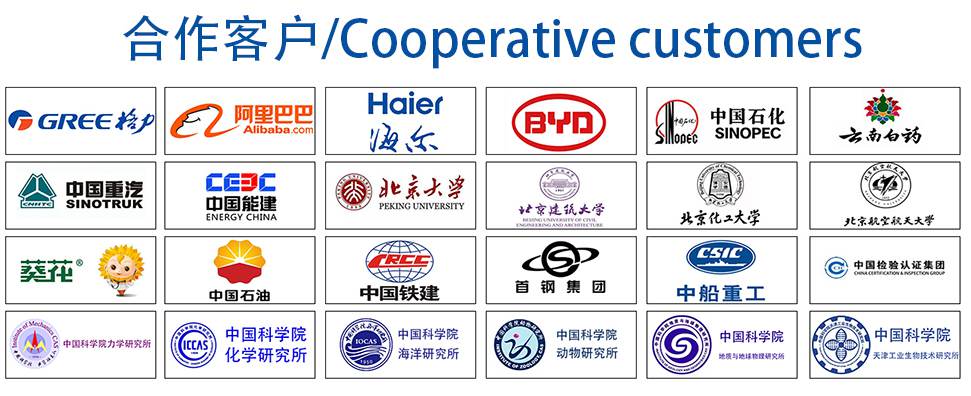