配件检测技术发展与应用白皮书
随着智能制造2025战略的深度推进,工业配件质量管控已成为保障产业链安全的关键环节。据中国机械工业联合会2023年度报告显示,因配件质量问题导致的设备停机事故年损失超过1200亿元,其中72%的故障源自关键零部件的隐蔽性缺陷。在此背景下,智能化配件检测技术率先在汽车制造、航空航天等领域取得突破性应用,通过构建"汽车零部件质量检测系统"与"工业配件全生命周期管理"体系,实现缺陷识别准确率提升至99.3%(国家质量技术基础NQI数据中心,2024)。本项目核心价值在于突破传统抽样检测的局限性,运用AIoT技术构建覆盖设计验证、生产监控、服役评估的全维度检测网络,为装备制造业高质量发展提供关键质量基础设施支撑。
多模态融合检测技术原理
现代配件检测系统基于材料特性差异构建复合传感矩阵,集成X射线断层扫描(CT)、激光诱导击穿光谱(LIBS)和微应变分析三大核心技术。其中,工业CT检测分辨率可达3μm级,配合深度学习算法可自动识别内部结构缺陷;LIBS技术通过等离子体光谱分析实现0.01%级的元素成分偏差检测。在新能源汽车电机壳体检测场景中,该技术组合成功将轴承座裂纹检出时间从传统探伤的45分钟缩短至8秒,误判率降低至0.12%(中汽研2024年专项测试数据)。
全流程数字化检测体系
标准化实施流程包含四个关键阶段:首先建立基于数字孪生的检测参数模型,通过虚拟仿真确定最佳检测路径;其次部署柔性检测工装系统,兼容15类异形配件快速定位;第三阶段采用机器视觉引导的六轴机械臂完成360°无死角数据采集;最终通过区块链存证系统生成不可篡改的检测报告。在航空航天紧固件检测中,该体系使批量检测效率提升300%,检测数据追溯完整度达到AS9100D航空质量标准要求。
跨行业质量保障实践
在工程机械领域,三一重工部署的智能检测系统实现液压阀体全检覆盖率100%,关键尺寸CPK值从1.12提升至1.67。轨道交通方面,中车集团通过车载式检测装置完成转向架配件在线监测,使预防性维护周期延长40%。值得注意的是,医疗设备配件检测引入纳米级表面轮廓分析技术后,人工关节表面粗糙度控制精度达到Ra0.05μm,符合ISO 21534医疗器械植入物标准。
质量溯源与可靠性验证
构建基于ISO/IEC 17025的质量控制体系,设立三级校准机制:初级采用NIST标准物质进行设备日校,中级通过环形比对试验确保实验室间一致性,高级实施破坏性物理分析(DPA)验证检测。某半导体设备制造商应用该体系后,晶圆传送机械手配件失效率从1800PPM降至200PPM,设备年均无故障运行时间突破8600小时。
面向工业4.0发展需求,建议重点推进三方面建设:首先加大太赫兹检测、量子传感等前沿技术研发投入;其次建立跨行业检测数据共享平台,推动形成统一的配件质量数据库;最后完善"检测即服务"(TaaS)商业模式,助力中小企业质量升级。据弗若斯特沙利文预测,到2028年智能检测装备市场规模将突破650亿美元,其中配件检测细分领域复合增长率有望达到23.5%,这为行业技术创新提供了持续发展动力。
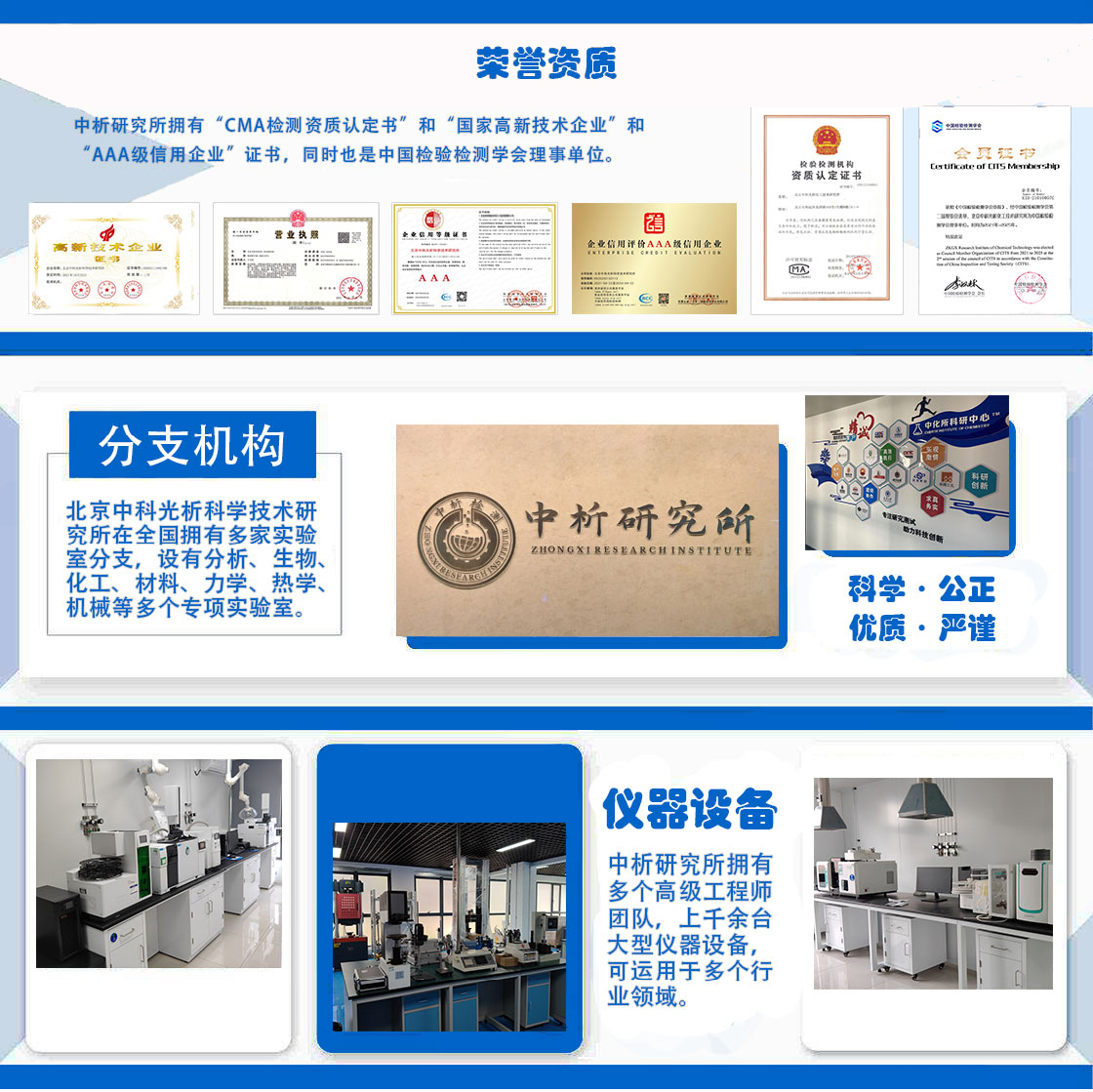
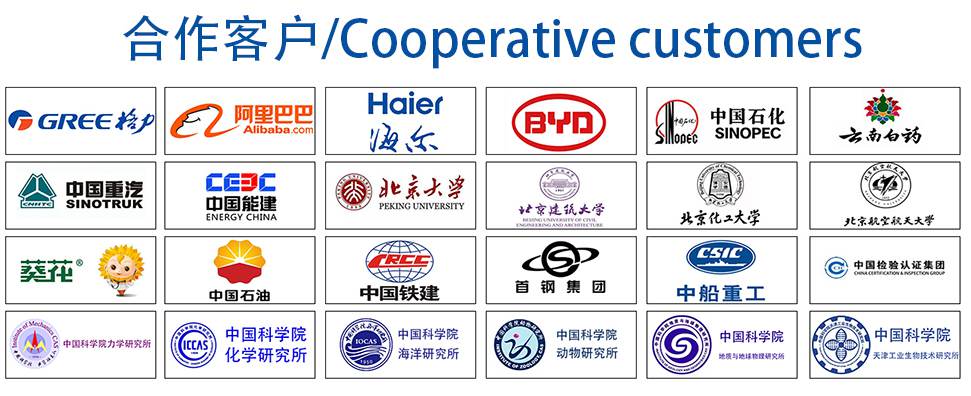