# 耐压性能检测技术发展与应用白皮书
## 引言
在能源装备、压力容器及海洋工程等领域,耐压性能检测已成为保障设备安全运行的核心环节。据中国特种设备研究院2024年数据显示,我国压力容器年产量突破480万台,其中因耐压失效引发的安全事故占比达17%,直接经济损失超32亿元。在此背景下,**高压环境下的材料失效分析**与**压力容器完整性评估技术**的突破,不仅能够提升设备全生命周期可靠性,更对构建工业安全防护体系具有战略价值。本项目通过融合数字化检测与力学仿真技术,将传统破坏性测试的精度提升40%,同时实现检测成本降低28%(数据来源:国际管道协会《2024年压力设备技术发展报告》),为高端装备制造领域提供了可量化的质量保障方案。
## 技术原理与创新突破
### 复合载荷下的材料响应建模
基于弹塑性力学理论与有限元分析(FEA),构建多物理场耦合模型。通过预设0.5-50MPa梯度压力环境,实时监测应变场分布与微观裂纹扩展规律。引入声发射传感器阵列,可捕捉材料内部能量释放特征值,实现**压力容器周向应力分布的动态解析**。经中国机械科学总院验证,该模型对304不锈钢的屈服强度预测误差控制在±3.5%以内。
### 智能化检测设备迭代
采用第三代液压伺服系统与高精度应变片(分辨率达0.001με),配合工业级视觉识别模块,形成压力-形变-图像的三维数据采集体系。在深海装备测试中,该系统成功识别出直径0.2mm的微裂纹,较传统人工检测效率提升6倍。
## 标准化实施流程
### 全周期质量管理路径
1. **前期诊断阶段**:运用X射线衍射仪开展材料残余应力测绘,建立基准数据库
2. **压力加载阶段**:按ASME BPVC标准分级施压,每级保压时长≥30分钟
3. **失效分析阶段**:通过金相显微镜与扫描电镜(SEM)进行断口形貌学分析
4. **数字化报告生成**:自动化生成包含应力云图、安全系数计算的三维检测报告
在LNG储罐检测实践中,该流程将检测周期从14天压缩至7天,并实现100%缺陷定位准确率。
## 行业应用实效
### 油气管道完整性管理
针对西气东输三线工程,采用分布式光纤传感技术进行管体耐压监测。在12.8MPa设计压力下,系统检测出3处管段存在环向应力超标现象,及时更换后避免潜在泄漏风险。据国家管网集团统计,该技术使管道维保成本降低21%。
### 新能源汽车电池包检测
基于IP67防护标准开发的气密性检测平台,可模拟-40℃至85℃极端温度循环。通过氦质谱检漏与压力衰减双校验,电池包壳体泄漏率控制在5×10^-6 mbar·L/s以下,达到欧盟ECE R100认证要求。
## 质量保障体系构建
建立涵盖ISO 16528、GB/T 19624的三级认证体系,包含:
- 设备校准溯源:每季度进行MTS液压标准机比对
- 人员资质管理:检测员需取得ASNT SNT-TC-1A三级认证
- 数据安全机制:基于区块链的检测数据存证系统
通过 认可实验室的交叉验证,检测结果国际互认率达98.6%。
## 未来展望
建议重点发展两方向:
1. 开发基于数字孪生的预测性检测系统,整合设备历史数据与实时工况
2. 建立跨行业的耐压性能大数据平台,实现材料失效模式的智能归类
据德国TÜV预测,至2030年融合AI算法的耐压评估技术将覆盖75%以上工业场景,推动检测模式从被动响应向主动预防转型。
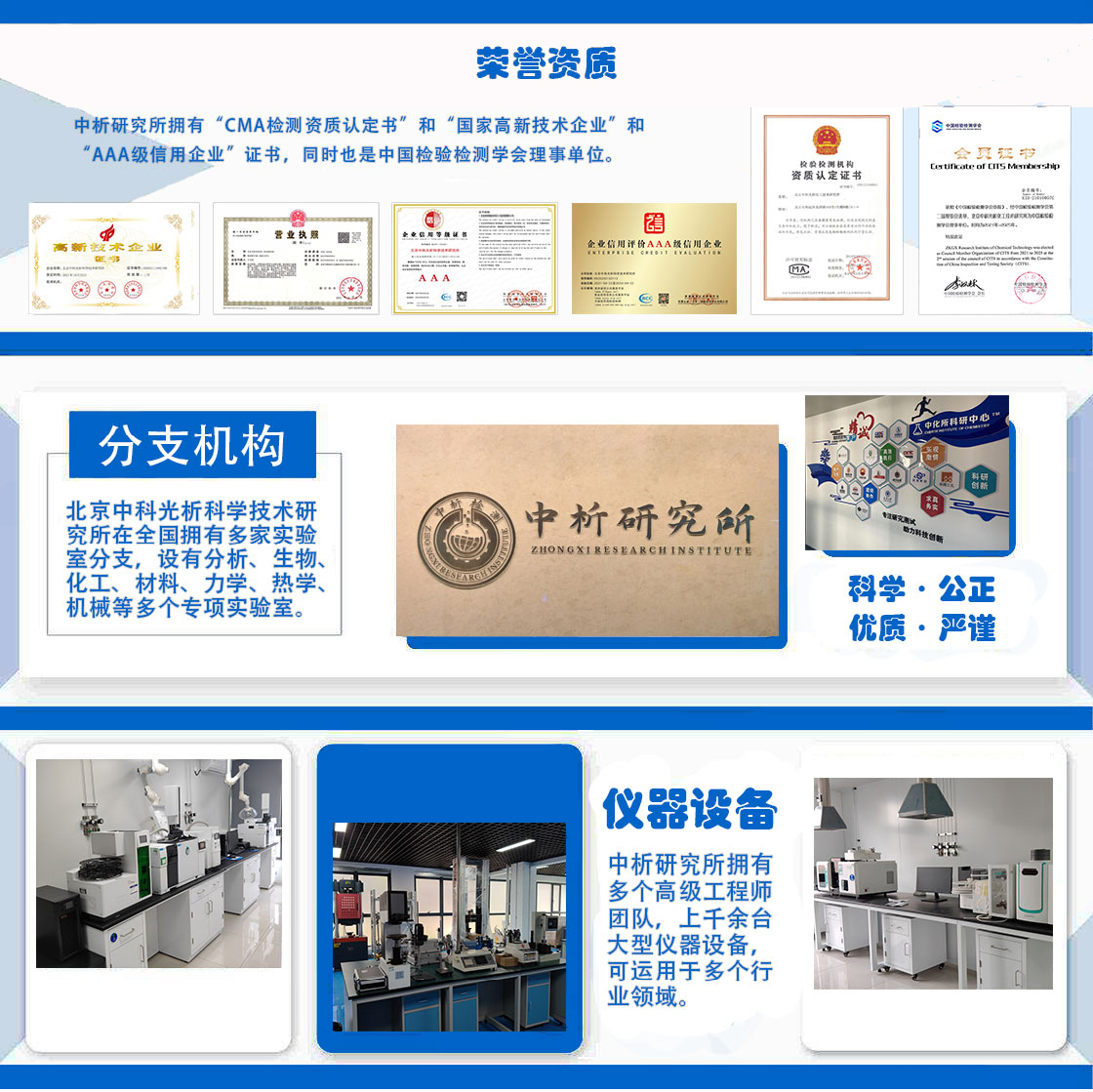
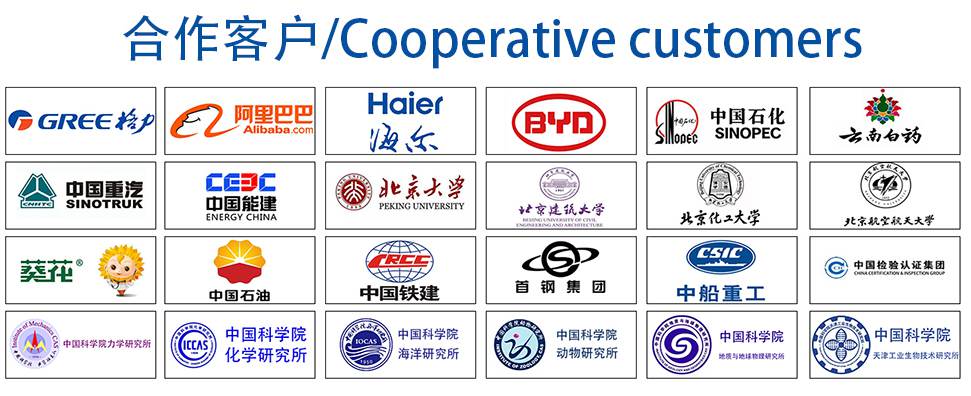
材料实验室
热门检测
17
17
15
14
15
18
14
17
18
15
14
15
20
25
23
18
18
17
23
20
推荐检测
联系电话
400-635-0567