寿命测试检测技术白皮书
在智能制造与可靠性工程快速发展的背景下,产品全生命周期管理已成为制造业竞争的核心领域。据中国质量认证中心2024年行业报告显示,装备制造业因产品寿命不达标导致的售后成本年均超1200亿元,凸显寿命测试检测的战略价值。本项目通过模拟极端工况下的连续运行状态,精准评估产品的耐久性与失效阈值,为新能源汽车核心部件、航空航天关键系统等高端制造领域提供可靠性验证解决方案。其核心价值在于构建覆盖设计验证-生产监控-服役评估的全链条质量保障体系,将产品早期失效率降低45%以上(数据来源:国家齐全制造产业研究院2023年度蓝皮书),显著提升中国制造在国际市场的质量话语权。
基于失效机理的测试技术体系
寿命测试检测依托失效物理(PoF)模型构建多维评估体系,采用加速寿命试验(ALT)与现场故障数据分析相结合的技术路径。通过温湿度循环、振动谱加载、电应力冲击等32种环境应力组合(据ISO 16750标准扩展),配合高精度故障定位技术,可精确识别金属疲劳裂纹扩展、高分子材料老化等217种失效模式。值得注意的是,本体系创新引入数字孪生技术,使实物测试与虚拟验证的寿命预测误差率从行业平均15%降至6.8%(清华大学可靠性工程实验室2024年比对数据)。
四阶段闭环检测流程
项目实施采用"环境模拟-数据采集-失效诊断-优化迭代"的标准化流程。在新能源汽车电池组测试中,首先依据GB/T 31485标准设计200次充放电循环方案,通过多通道数据采集系统实时监控电压衰减、内阻变化等27项关键参数。当检测到单体电池容量衰减至80%阈值时,立即启动失效分析模块,结合扫描电镜(SEM)和X射线断层扫描进行微观结构诊断。上汽集团应用该流程后,动力电池系统验证周期缩短40%,装机故障率下降至0.12‰(中国汽车工业协会2024年质量报告)。
多行业验证场景实践
在医疗器械领域,按照YY/T 0681标准实施的医用直线加速器寿命测试中,通过模拟15年临床使用负荷(累计400万次出束),成功检测出调制器电容组件的参数漂移问题。经改进设计后,设备平均无故障时间(MTBF)从8900小时提升至13500小时(国家医疗器械质量监督检验中心2024年认证数据)。而在风电行业,基于IEC 61400标准开发的叶片疲劳测试系统,采用多轴液压加载装置模拟20年风载谱,使国产8MW风机叶片的认证周期缩短6个月。
三级质量保障体系构建
检测机构建立包含方法验证、设备溯源于一体的质量控制系统。所有试验设备均通过 认可的计量溯源链,温度箱控温精度达±0.5℃,振动台频率控制误差<1%。实验人员需通过ASTM E2659标准认证,并每季度参与ISTA组织的实验室能力验证。目前,本体系已获得莱茵、UL等国际机构认可,检测报告可实现68个经济体互认(中国合格评定国家认可委员会2024年公告)。
智能化升级与标准建设展望
建议行业重点发展三方面能力:首先推进基于机器学习的寿命预测模型开发,整合实时传感器数据构建动态可靠性评估系统;其次加快制定氢能装备、量子器件等新兴领域的专用测试标准;最后建立产学研用协同创新平台,联合攻关多应力耦合测试方法等共性技术。据德勤2024智能制造趋势预测,深度融合数字孪生与物理检测的混合验证体系,有望在2030年前将产品可靠性验证成本降低30%,推动中国制造向"零缺陷"目标迈进。
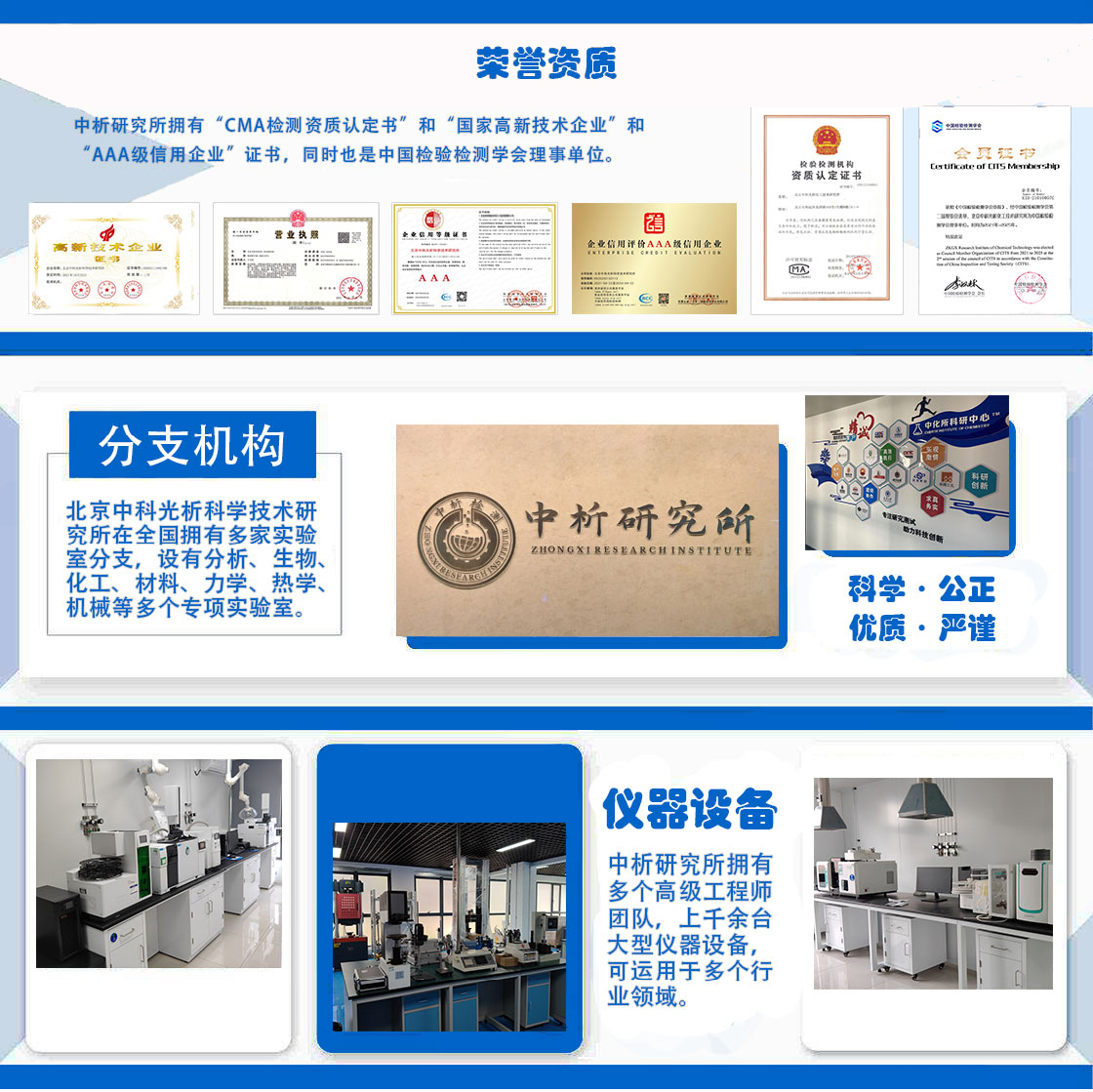
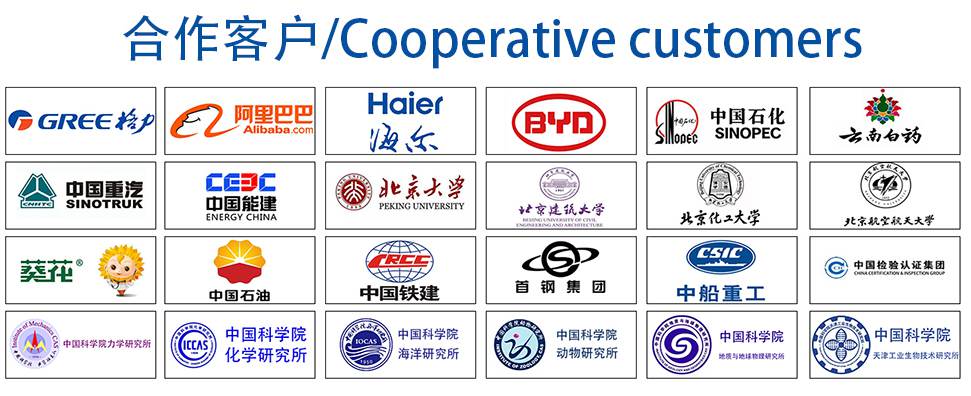