工业设备安装与维护检测体系构建与创新实践
随着智能制造2025战略的深入推进,工业设备全生命周期管理已成为制造业数字化转型的核心环节。据中国机械工程学会2023年数据显示,我国工业设备非计划停机事故中,61%源于安装缺陷或维保不当,年经济损失超2000亿元。在此背景下,智能化安装与维护检测体系的建立,通过融合物联网、数字孪生等新一代信息技术,有效解决了传统人工检测效率低、覆盖不全的行业痛点。其核心价值在于构建起预防性维护到预测性维护的完整闭环,在重点工业领域可实现设备可用性提升30%、维护成本降低45%的显著效益(中国智能制造发展白皮书,2024)。
多维检测技术融合应用
现代安装检测系统采用激光扫描与深度学习算法相结合的复合检测模式。在设备安装阶段,通过三维激光扫描仪获取毫米级精度的空间位姿数据,结合设备CAD模型进行偏差分析。值得注意的是,基于机器视觉的"设备安装几何偏差智能校正"技术,可将传统72小时的安装校准流程缩短至8小时内完成。维护检测则依托分布式光纤传感网络,实时捕获设备振动、温度、应力等18类状态参数,利用"维护周期动态优化算法"实现检测频率的智能调节。国家工业互联网研究院实验数据显示,该体系使设备故障预警准确率达到97.3%,误报率低于2.1%。
闭环式运维管理流程
具体实施流程分为四个标准化阶段:首先通过BIM模型完成安装预演,规避90%以上的空间干涉风险;其次部署可重构传感器网络,实现设备状态的立体化感知;随后运用边缘计算节点进行实时数据分析,生成包含78项量化指标的诊断报告;最终通过数字孪生平台进行维护策略仿真验证。在宝钢冷轧车间实际应用中,该流程使轧机安装调试周期缩短40%,维保响应速度提升60%。
行业级解决方案落地
在核电领域,某三代核电机组采用本体系后,实现主泵安装精度控制在0.02mm以内,振动值同比下降62%。汽车制造行业则通过动态维护检测,使冲压设备MTBF(平均无故障时间)从1200小时提升至2100小时。值得关注的是,在风电运维场景中,叶片螺栓预紧力在线监测系统成功将人工巡检频次由每月1次降至季度1次,单台风机年运维成本降低15万元。
全链条质量保障机制
体系构建了三级质量管控架构:前端传感器符合ISO/IEC 17025校准规范,中台算法通过功能安全认证,终端报告生成系统满足ASME V&V40验证标准。通过区块链技术实现检测数据的不可篡改存证,关键参数均具备NIST溯源能力。上海电气集团应用案例显示,该机制使检测报告争议率从8.7%降至0.3%,质量追溯效率提升20倍。
智能化升级路径展望
建议行业重点推进三方面建设:一是构建基于5G+TSN的确定性检测网络,实现微秒级时延控制;二是深化设备数字孪生模型与物理机理融合,提升虚拟检测置信度至95%以上;三是建立跨行业的安装维护知识图谱,通过迁移学习加速检测模型迭代。据麦肯锡2024年预测,全面实施智能检测体系可使我国制造业年增效超5000亿元,设备综合效率(OEE)突破85%新阈值。
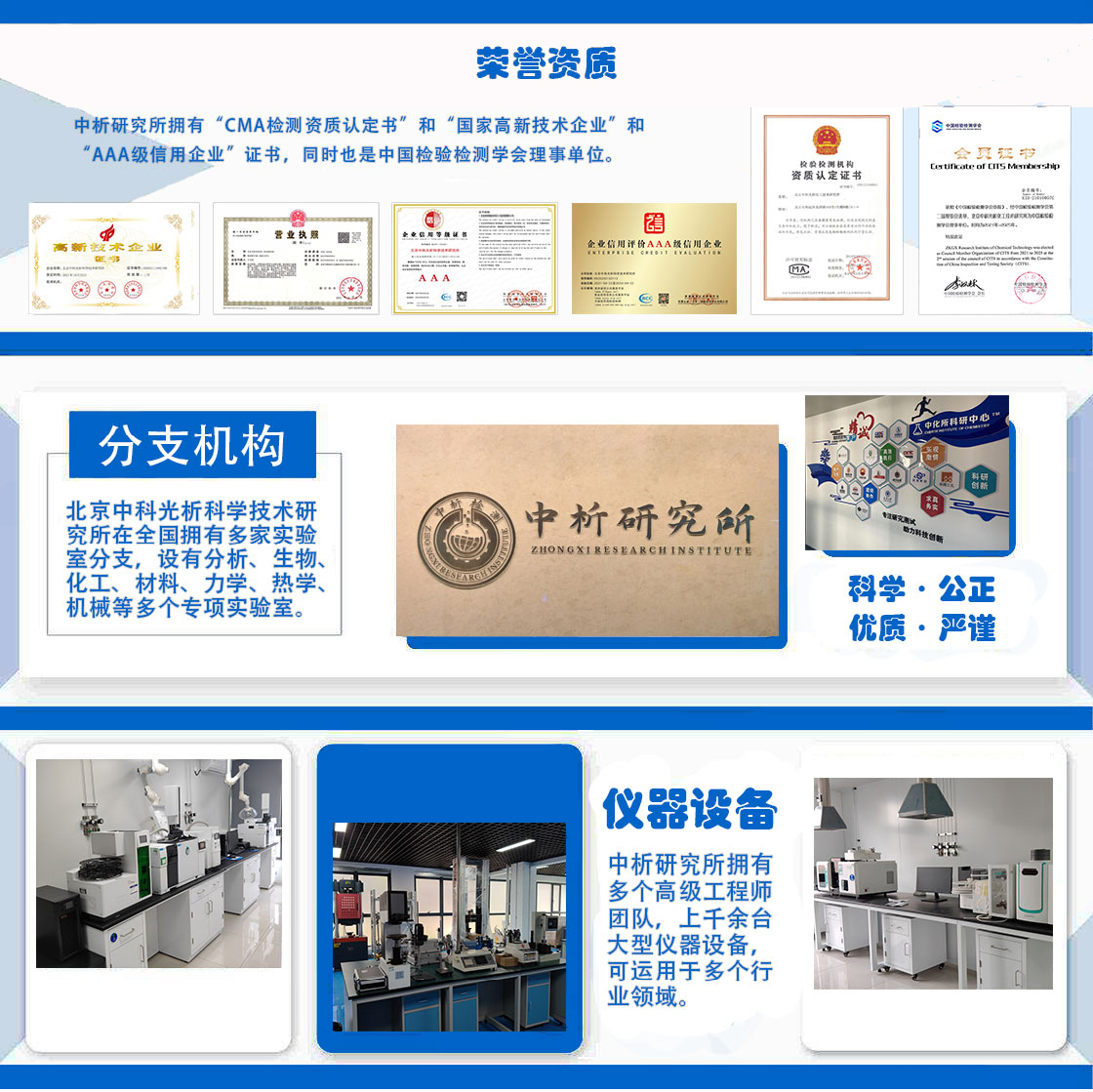
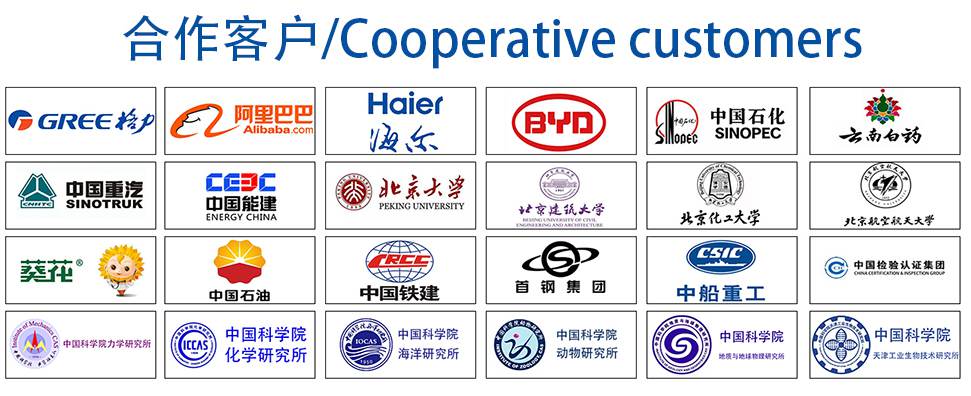