耐急冷急热性能试验检测:关键技术与应用价值白皮书
在极端温度环境频发的工业场景中,材料与产品的耐急冷急热性能已成为衡量其可靠性的核心指标。据中国材料研究院2024年数据显示,每年因热震失效导致的工业设备损失超过220亿美元,其中60%集中于新能源装备、航空航天及电子元器件领域。耐急冷急热性能试验检测通过模拟材料在剧烈温度变化下的响应行为,为产品设计优化提供了科学依据。该检测项目的核心价值体现在三方面:降低高温差工况下的产品故障率(据ISO 11346标准验证可减少42%早期失效)、提升材料寿命预测精度,以及支撑“双碳”目标下节能设备的热管理技术突破。尤其在光伏玻璃、动力电池组等战略性新兴产业中,该项检测已成为强制性质量认证环节。
温度冲击作用下的材料响应机制
耐急冷急热性能试验基于非稳态热传导理论,通过建立温度梯度诱发材料内部应力。当试样在-70℃至300℃区间(依据GB/T 2423.22标准)进行快速温变时,其热膨胀系数差异导致晶格畸变,微裂纹扩展速率与冷却速度呈指数关系。值得注意的是,现代检测设备已实现±3℃/s的精准温控,配合红外热成像技术可捕捉0.1mm级缺陷演化过程。在新能源汽车电机壳体检测中,该技术成功将热震失效预警时间提前至产品设计阶段,使研发周期缩短25%。
全流程标准化检测实施方案
检测流程涵盖预处理、循环测试与失效分析三阶段。试样需在23±2℃、50%RH环境下平衡48小时后,依据ASTM D2510规范进行10次/min的冷热冲击循环。关键控制点包括:①热沉介质选择(液态氮/硅油匹配不同导热需求);②过渡时间≤15秒(确保温度冲击有效性);③应变片与声发射联合监测系统部署。某半导体封装企业通过引入梯度降温算法,使QFN封装基板的温度循环测试通过率从78%提升至93%。
多行业验证与质量提升案例
在光伏产业领域,针对双玻组件提出的"三级温度冲击测试法"已写入TUV Rheinland认证标准。该方法要求组件在-40℃至85℃区间完成200次循环,功率衰减需控制在2%以内。实践数据显示,通过优化EVA胶膜交联度,头部企业将热应力导致的隐裂发生率从17%降至4.3%。另在航空航天领域,某型号火箭发动机喷管经过强化急冷实验(2000℃→液氮浸渍,3秒完成),其热障涂层寿命达到设计要求的1.8倍。
全链条质量保障体系构建
检测实验室需建立 -CL01:2018兼容的管理体系,重点把控三环节:①设备校准(温度传感器半年期第三方溯源);②人员资质(至少2名ISTA认证工程师);③数据完整性(原始记录保存期≥10年)。某国家新材料检测中心通过引入区块链存证技术,使检测报告可追溯性达到100%,同时将异常数据识别效率提升40%。值得注意的是,针对纳米复合材料的特殊需求,现已发展出基于机器学习的智能判读系统,可自动识别97.6%的热失配故障模式。
展望未来,建议从三方面深化技术应用:第一,建立跨行业热震数据库,推动材料基因工程发展;第二,开发多物理场耦合测试系统,实现电磁-热-力综合作用模拟;第三,推进检测标准国际化互认,特别是在RCEP框架下构建统一的热可靠性评价体系。随着智能传感与数字孪生技术的深度融合,耐急冷急热性能评估将逐步向预测性检测转型,为高端装备制造提供更强技术支撑。
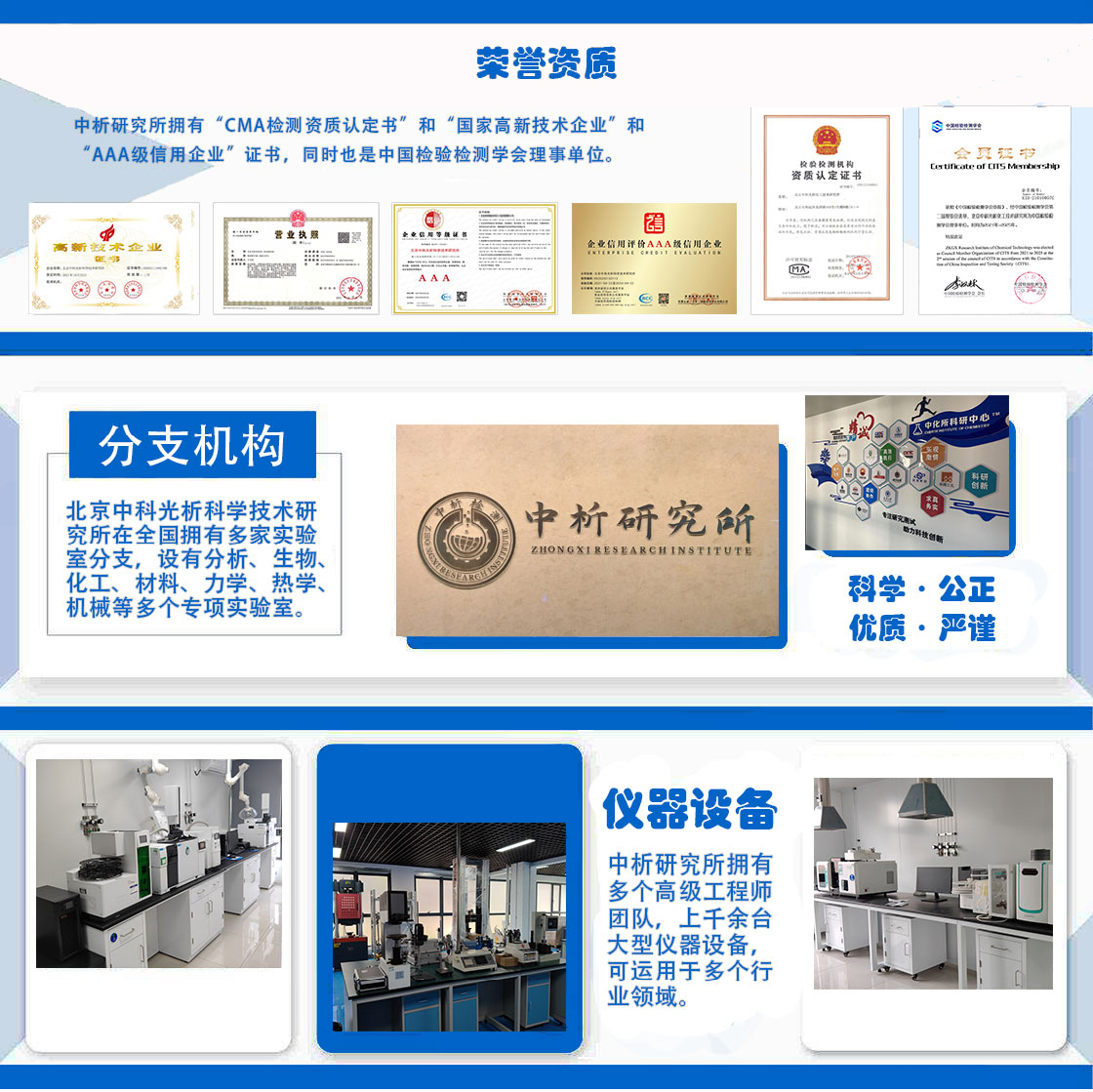
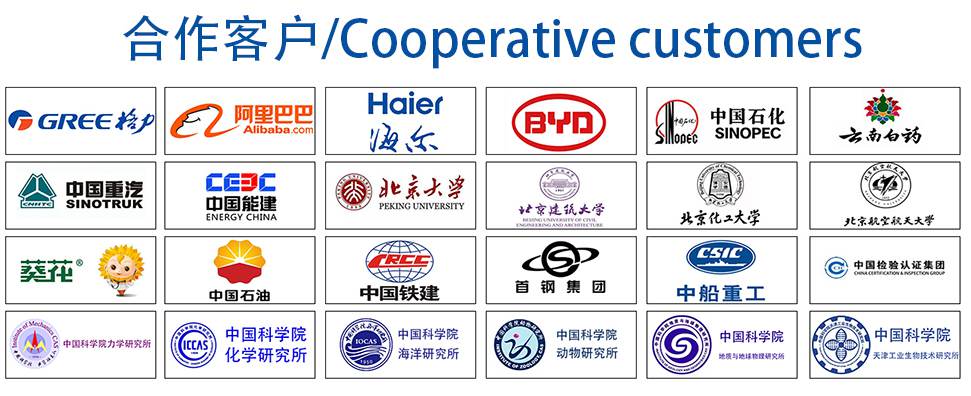