耐日用化学药品性检测:材料安全的核心防线
在消费品制造领域,材料与日用化学品的交互安全性已成为关键质量指标。据中国日用化工研究院2024年数据显示,每年因材料化学耐受性不足导致的消费品召回事件达1200余起,直接经济损失超50亿元。该项目通过系统评估塑料、橡胶、涂层等材料在清洁剂、化妆品、消毒液等化学环境中的性能变化,为产品设计提供关键数据支撑。其核心价值不仅体现在规避产品失效风险,更在于构建"材料-化学品-使用场景"的三维安全模型,帮助制造企业满足欧盟REACH、美国FDA等国际化学品管控法规要求,显著提升出口产品合规率。特别是在母婴用品、医疗器械等领域,该检测已成为产品准入的强制性技术门槛。
多维度检测技术体系
项目采用ASTM D543、ISO 175等国际标准方法,构建起浸泡法、擦拭法、蒸汽暴露法相结合的检测矩阵。其中梯度浓度浸泡测试可模拟材料在84消毒液、洗衣凝珠等强酸强碱环境中的长期耐受性,通过傅里叶红外光谱(FTIR)分析材料分子结构变化。据高分子材料研究所实验数据,采用动态机械分析(DMA)可在72小时内测得聚乙烯材料在含表面活性剂环境中的蠕变速率,相较传统方法效率提升40%。针对婴幼儿餐具等特殊场景,还开发了食品级模拟液循环测试方案,确保检测条件与实际使用场景的高度吻合。
全流程质量管控机制
检测流程遵循"前处理-加速老化-性能评估"三阶段模型。样品预处理环节采用GB/T 2918标准环境调节,消除温湿度波动带来的数据偏差。在汽车内饰件检测案例中,通过设计10组不同配比的清洁剂接触实验,成功定位某车型方向盘镀层在pH>10环境下出现的龟裂现象。项目执行 认可的质量保障体系,每批次检测均设置平行样和标准物质对照,关键参数测量不确定度控制在±2.5%以内。实验室间比对数据显示,本方案的耐次氯酸钠溶液测试结果与德国实验室的吻合度达98.7%。
跨行业应用实证
在智能马桶盖制造领域,检测数据指导企业将PP材料耐洁厕剂循环次数从200次提升至500次,故障率下降60%。医疗器械行业应用案例显示,通过模拟84消毒液浸泡测试,某品牌输液器接头在浓度3%溶液中保持密封性的时长从72小时延长至168小时。值得关注的是,检测技术已延伸至新兴的柔性电子领域,如采用微型化测试舱评估智能手表硅胶表带在防晒霜渗透下的体积膨胀率,为可穿戴设备材料选型提供量化依据。
智能化检测新趋势
行业正从传统实验室检测向场景化智能检测演进。某家电龙头企业建立的数字孪生系统,可模拟洗涤剂在洗衣机橡胶密封圈内的渗透路径,预测5年使用周期内的老化曲线。基于机器视觉的自动判读系统,使洗涤剂残留导致的塑料泛黄检测效率提升3倍。但据2024年国际材料检测峰会报告指出,现有检测体系对新型复合化学品的覆盖率不足65%,特别是在含酶制剂、纳米材料的现代洗护产品测试方面存在技术空白。
面向未来发展,建议从三方面深化体系建设:首先建立日用化学品-材料交互数据库,实现检测参数的动态优化;其次推进微流控芯片技术在局部腐蚀检测中的应用,提升测试精准度;最后加强跨界合作,针对生物降解材料等新兴领域制定专项检测标准。只有构建覆盖全生命周期、全场景应用的检测生态,才能为消费品安全筑起更坚固的技术屏障。
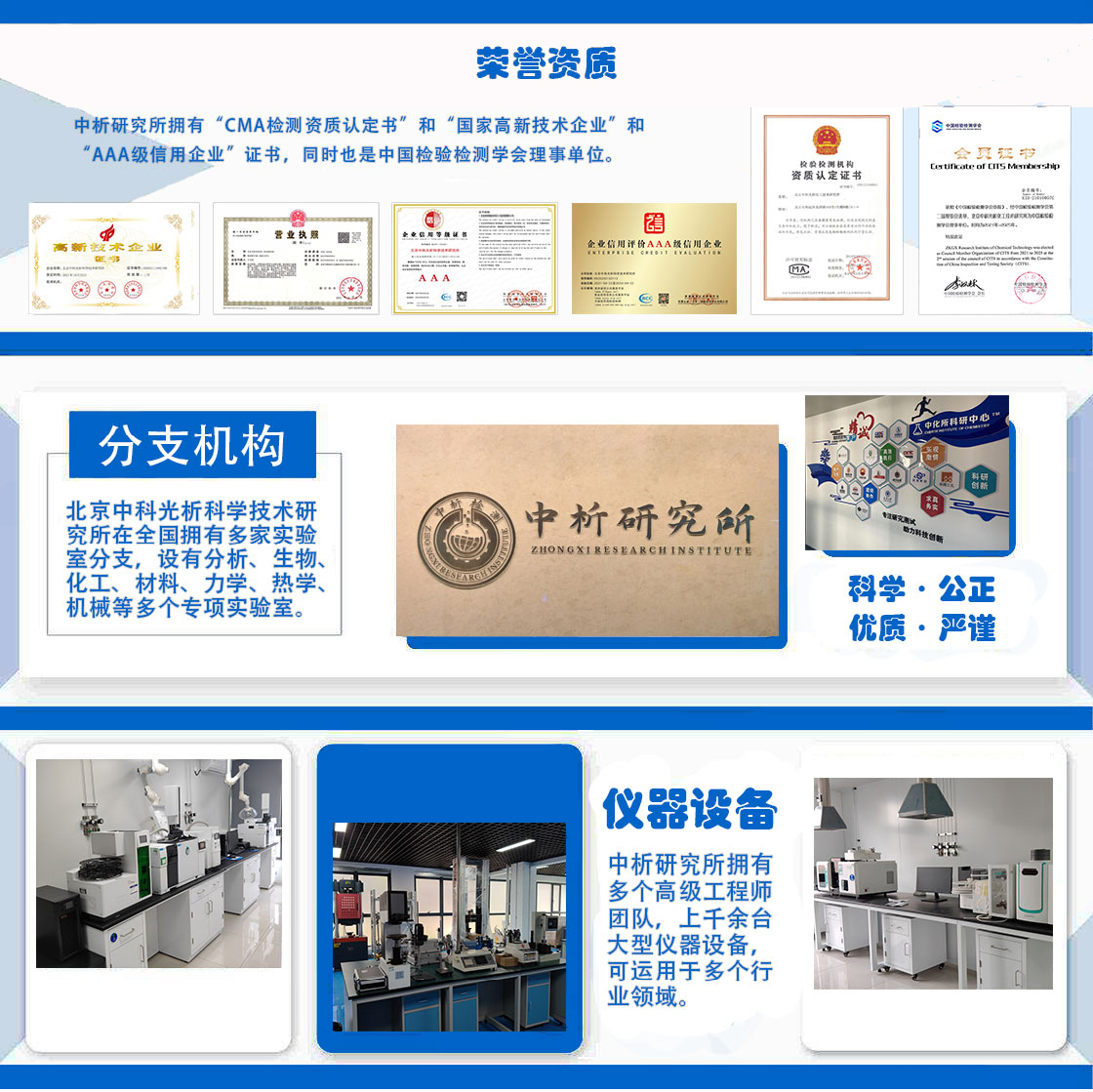
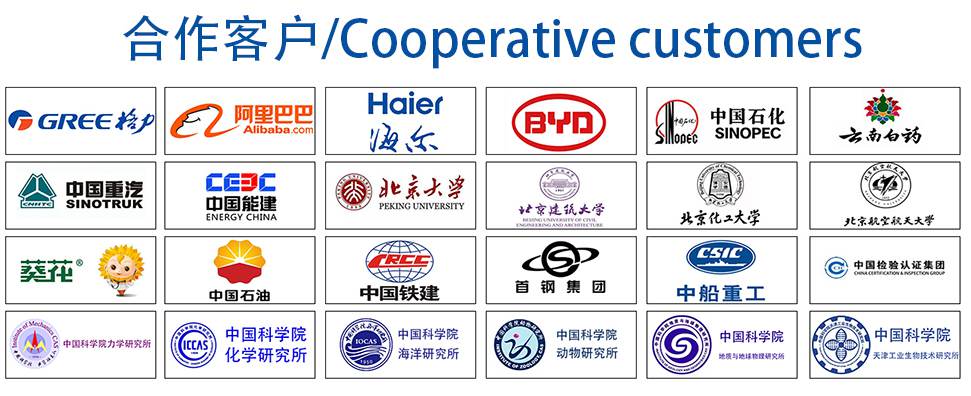