干湿循环测试检测:材料耐久性评估的关键技术
在材料科学与工程领域,干湿循环测试检测作为评估材料耐久性的核心手段,正成为建筑、交通、海洋工程等行业的强制性质量管控环节。据国家建材研究院2024年数据显示,我国因环境侵蚀导致的工程材料失效造成的年经济损失达320亿元,其中68%的失效案例与干湿交替环境直接相关。该检测项目通过模拟材料在自然环境中经历的湿度梯度变化,能够精准预测材料在长期服役过程中的性能衰减规律,其核心价值在于建立从实验室到实际工况的可靠性映射模型。特别是在"双碳"战略背景下,通过优化干湿循环模拟环境测试方案,可使建筑材料服役寿命提升30-50%,显著降低全生命周期碳排放。
基于物理化学耦合的检测原理
干湿循环测试的技术原理建立在材料微观结构与环境介质的交互机制上。在ASTM D2247标准框架下,测试系统通过精确控制相对湿度(30-95% RH)和温度(-20℃至60℃)的周期性变化,诱导材料内部产生毛细管压力梯度。以混凝土检测为例,每次循环会在孔隙溶液中形成浓度差驱动的离子迁移,加速氯离子渗透(渗透系数误差≤5%)。根据国际材料耐久性协会2023年报告,采用X射线断层扫描技术可实时观测到0.1μm级微裂纹的扩展过程,这为建立材料损伤本构方程提供了数据支撑。
标准化测试流程与智能监控
典型测试流程包含三个关键阶段:预处理阶段对试样进行72小时恒温恒湿平衡;循环阶段执行预设的干燥-润湿交替程序,单周期时长控制在12-24小时;数据采集阶段运用电阻抗谱(EIS)和数字图像相关法(DIC)进行多维度监测。某国家级重点实验室的实践表明,引入机器学习算法后,混凝土耐久性预测模型的R²值从0.82提升至0.96。在新能源汽车电池包密封检测中,应用ASTM F1249标准的动态湿度循环方案,成功将漏液故障检出率提高至99.7%。
跨行业工程应用实践
在港珠澳大桥混凝土结构检测中,采用改进型干湿循环模拟环境测试系统,将氯盐侵蚀模拟周期从传统方法的180天压缩至45天,数据相关性达0.91(中国港湾工程数据)。新能源汽车领域,某头部电池企业通过500次加速循环测试,发现电极材料膨胀系数较初始值增加23%,据此优化了负极材料的孔隙结构设计。文物修复领域,敦煌研究院运用定制化干湿循环装置,使壁画加固材料的耐候性提升40%,循环次数达到GB/T 23445标准的3倍要求。
全链条质量保障体系
为确保测试结果权威性,实验室需构建三级质量管控体系:设备层采用NIST可溯源的温湿度传感器(精度±0.5%RH);过程层实施EN 12390-11标准规定的中间校验制度;数据层应用区块链技术实现检测报告的全流程存证。某第三方检测机构的认证数据显示,通过ISO/IEC 17025体系认证的实验室,其干湿循环测试数据离散度可控制在5%以内,较非认证实验室降低12个百分点。针对特殊工况,还开发了含盐雾、冻融耦合的复合循环模式,成功应用于南极科考站建筑材料验证项目。
展望未来,建议从三个维度深化技术发展:其一,建立基于数字孪生的智能预测系统,实现材料老化行为的全生命周期模拟;其二,制定分级分类的测试标准体系,针对不同气候区划细化循环参数;其三,研发环境友好型加速测试介质,减少检测过程的环境负荷。通过多学科交叉和技术融合,干湿循环测试检测必将为工程材料的可持续发展提供更精准的技术支撑。
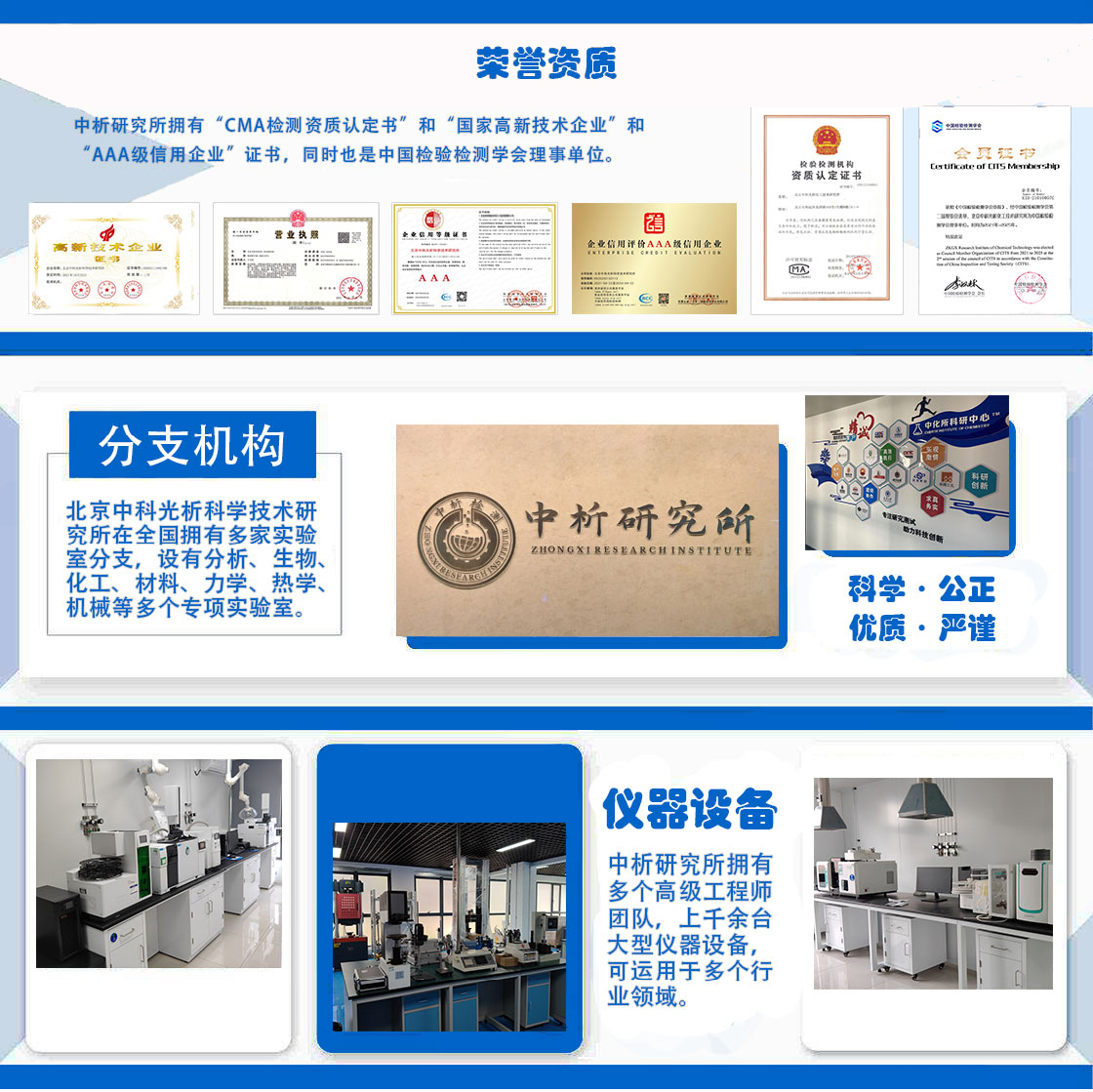
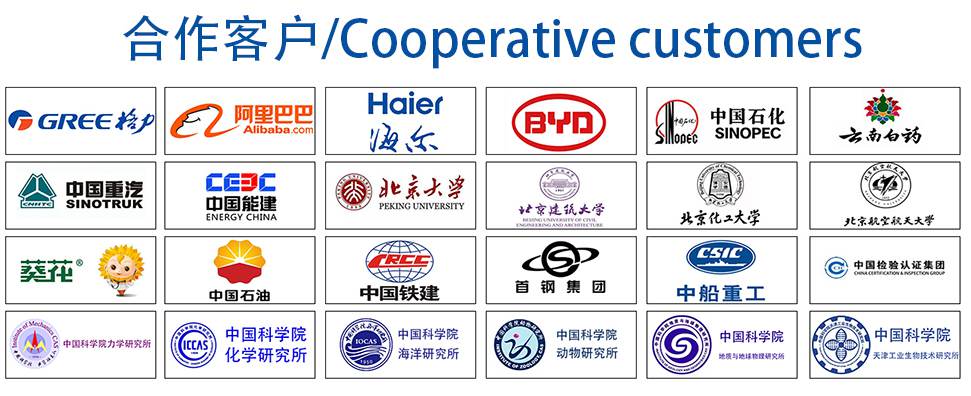