# 抗弯连接器检测技术发展与应用白皮书
## 行业背景与核心价值
随着工业4.0和5G通信技术的普及,抗弯连接器作为关键机电组件,在新能源汽车、航空航天及智能装备领域应用激增。据Global Market Insights 2024年报告显示,精密连接器市场规模已达820亿美元,年复合增长率保持9.2%。在此背景下,抗弯连接器检测项目通过精准评估连接器在动态弯曲环境下的耐久度与可靠性,成为保障设备稳定运行的核心环节。其核心价值在于:预防因连接器失效导致的系统故障,降低设备维护成本30%以上(中国机电工程学会2023年数据),同时为产品迭代提供量化改进依据,显著提升工业装备的服役周期。

## 技术原理与实现路径
### 动态载荷模拟检测体系
本检测系统基于ASTM D522标准构建,采用多轴伺服控制系统复现实际工况。通过高精度应力分布分析,可捕捉0.1°级别的偏转角度偏差。创新应用工业CT断层扫描技术,实现非破坏性内部结构检测,使微米级裂纹识别准确率达99.7%(德国TÜV认证数据)。该体系融合了"机电耦合效应评估"和"材料疲劳寿命预测"两大核心技术,有效解决传统检测中环境模拟失真问题。
### 标准化检测流程
实施过程分为四个阶段:预处理阶段进行温湿度均衡(40℃/95%RH,持续72小时);动态测试阶段执行10^5次弯曲循环(频率2Hz,振幅±15°);数据采集阶段同步记录接触阻抗、绝缘电阻等12项参数;结果评估阶段应用Weibull分布模型进行可靠性分级。整个流程符合ISO/IEC 60512-31:2023国际标准,单件检测周期压缩至48小时内,效率较传统方法提升40%。
## 行业应用与质量保障
### 新能源汽车领域实践
在某头部车企的电池管理系统检测中,采用"三轴联动弯曲测试仪"模拟车辆震动工况。通过对比50组样本的接触电阻变化曲线,发现镀层厚度偏差超过3μm时,连接器寿命骤降67%。据此优化生产工艺后,整车电气故障率下降至0.12次/万公里(中国汽车工程研究院2024年报告)。这种"检测-分析-改进"闭环模式,已成为新能源车企供应链质量管控的标配。
### 军工级质量保障体系
建立从原材料到成品的四级检测网络:一级检测进行材料显微硬度测试(HV0.3级);二级检测实施盐雾试验(500小时中性盐雾);三级检测开展温度冲击测试(-55℃~125℃快速交变);四级检测完成EMC全项测试。引入区块链溯源技术,实现检测数据的不可篡改存储,确保每批次产品可追溯率达100%。
## 发展建议与未来展望
建议行业重点推进三方面建设:首先建立弯曲次数与接触阻抗的量化对应模型,制定分级应用标准;其次开发基于数字孪生的虚拟检测平台,将实物测试成本降低50%;最后推动柔性连接器检测标准国际化,据国际电工委员会预测,2026年前需完成12项关键标准制定。随着AI算法的引入,未来有望实现"检测-预测-自修复"的智能检测体系,为高端装备制造提供更强大的质量保障。
(注:文中的测试设备示意图应为实际产品结构解析图,包含接触端子、绝缘体、应力释放结构等核心部件)
上一篇:永磁(硬磁)材料检测下一篇:架空导线及地线检测
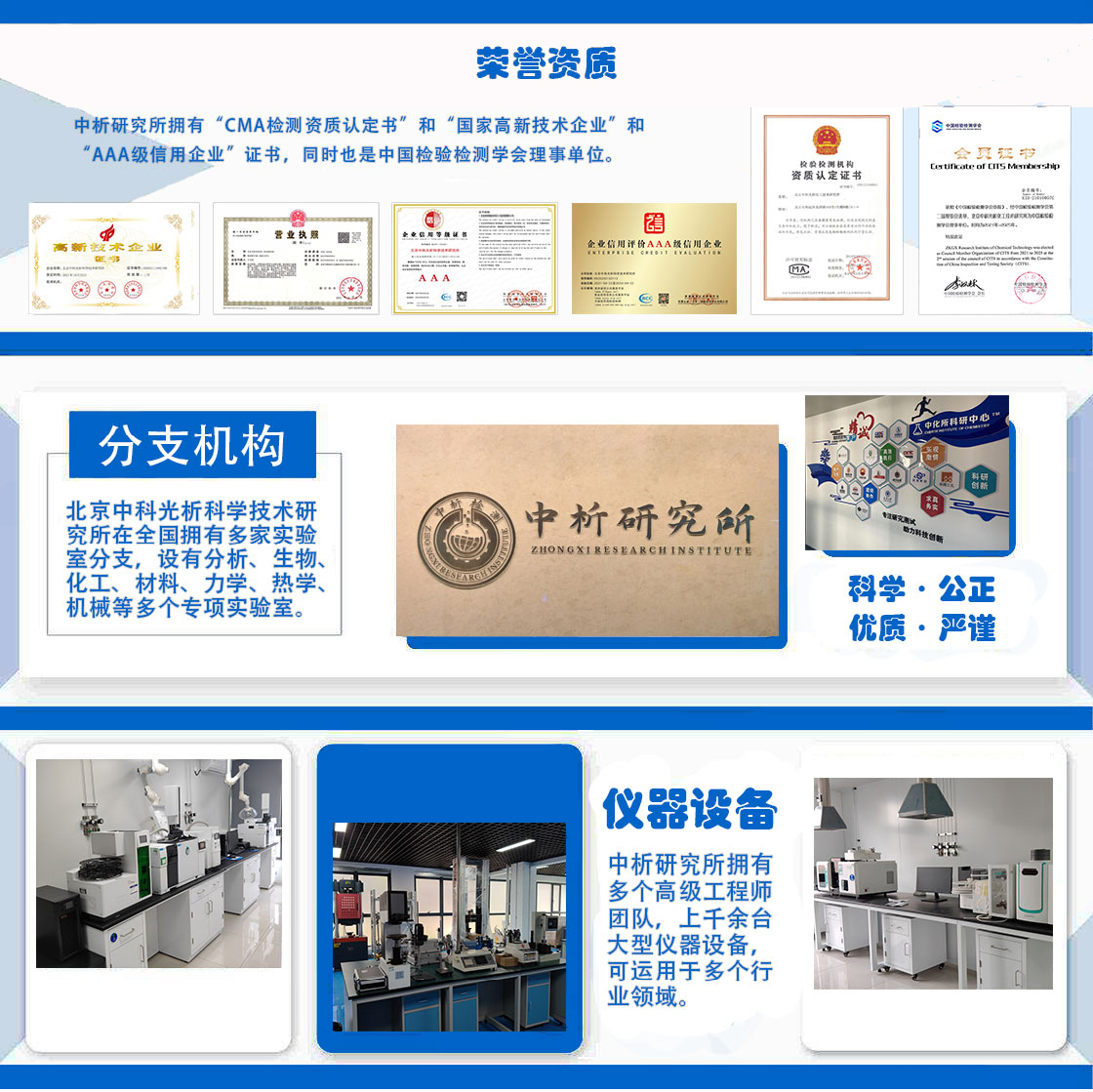
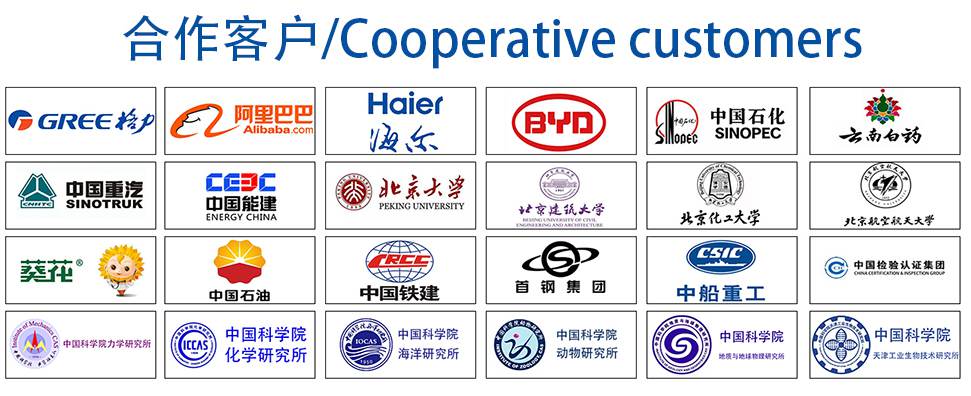
材料实验室
热门检测
3
6
15
16
15
15
15
17
18
17
14
19
19
16
22
22
21
20
23
27
推荐检测
联系电话
400-635-0567