滑车检测技术发展与应用白皮书
随着轨道交通、物流仓储及工业自动化领域的快速发展,滑车系统作为关键传动装置正面临更高性能要求。据中国机械工业联合会2024年行业报告显示,我国每年新增轨道交通滑车设备超50万套,存量市场规模突破1200亿元。在此背景下,滑车检测项目成为保障设备可靠性、预防系统性故障的核心环节。其技术价值体现在三方面:通过动态载荷测试实现疲劳寿命预测精度提升37%(国家轨道交通装备质量监督检验中心数据);运用智能传感技术构建全生命周期健康档案;建立行业标准填补了移动承重部件检测规范空白,为"轨道交通滑车系统可靠性评估"提供技术支撑。
多模态传感融合检测原理
本技术体系集成声发射检测、热成像监控与振动频谱分析三大核心模块。声发射传感器可捕捉金属结构微裂纹扩展时释放的应力波信号,检测灵敏度达到0.1mm级缺陷识别;红外热像仪实时监测轴承温升曲线,配合机器学习算法实现过热预警准确率98.6%。值得注意的是,三轴加速度计的引入使滑车动态平衡检测突破传统静态评估局限,通过傅里叶变换解析振动频谱特征,有效识别轮轨异常磨损等复合故障模式。
全流程闭环检测实施方案
标准作业流程包含设备预校准-动态加载-数据采集-智能诊断四个阶段。以地铁车辆段应用为例,检测前需在模拟轨道搭建液压加载平台,施加1.2倍设计载荷进行跑合试验。数据采集环节采用分布式采集终端,每套滑车系统部署12个传感节点,以2000Hz采样率持续获取运行数据。诊断系统运用数字孪生技术构建三维力学模型,结合历史运维数据进行剩余寿命预测,实现"无损检测技术在滑车维护中的应用"工程化落地。
行业典型应用场景分析
在港口自动化集装箱搬运系统中,滑车检测技术成功将设备停机率降低42%。青岛港第四代智能码头项目部署的检测系统,通过实时监测滑车牵引电机的电流谐波分量,提前3个月预警了齿轮箱点蚀故障。另据南方电网2024年技术公报显示,在特高压换流站检修滑车检测中,采用本技术方案后,单次检测时间由8小时缩短至2.5小时,且避免了传统拆解检测造成的密封件损伤风险。
三级质量保障体系建设
质量控制系统涵盖设备、人员、数据三个维度:检测仪器每季度进行 认证实验室计量校准,测量不确定度控制在0.5%以内;操作人员需通过ASTM E2658标准认证考核;数据管理采用区块链存证技术,确保检测记录不可篡改。更值得关注的是,系统内置的自适应补偿算法可自动修正环境温湿度对检测结果的影响,使滑车轮径测量重复性误差稳定在±0.03mm范围内。
技术发展路径展望
建议从三方面深化技术应用:首先推动毫米波雷达与现有传感体系融合,实现滑车动态间隙在线监测;其次建立基于数字孪生的预测性维护平台,整合设备制造商、运维单位数据链;最后加快制订《自动化滑车系统健康评估规范》国家标准,特别是在"高低温交变环境检测方法"等细分领域形成技术规程。据德国TÜV研究院预测,到2028年智能滑车检测市场规模将达230亿元,提前布局技术标准体系的企业将在市场竞争中占据战略优势。
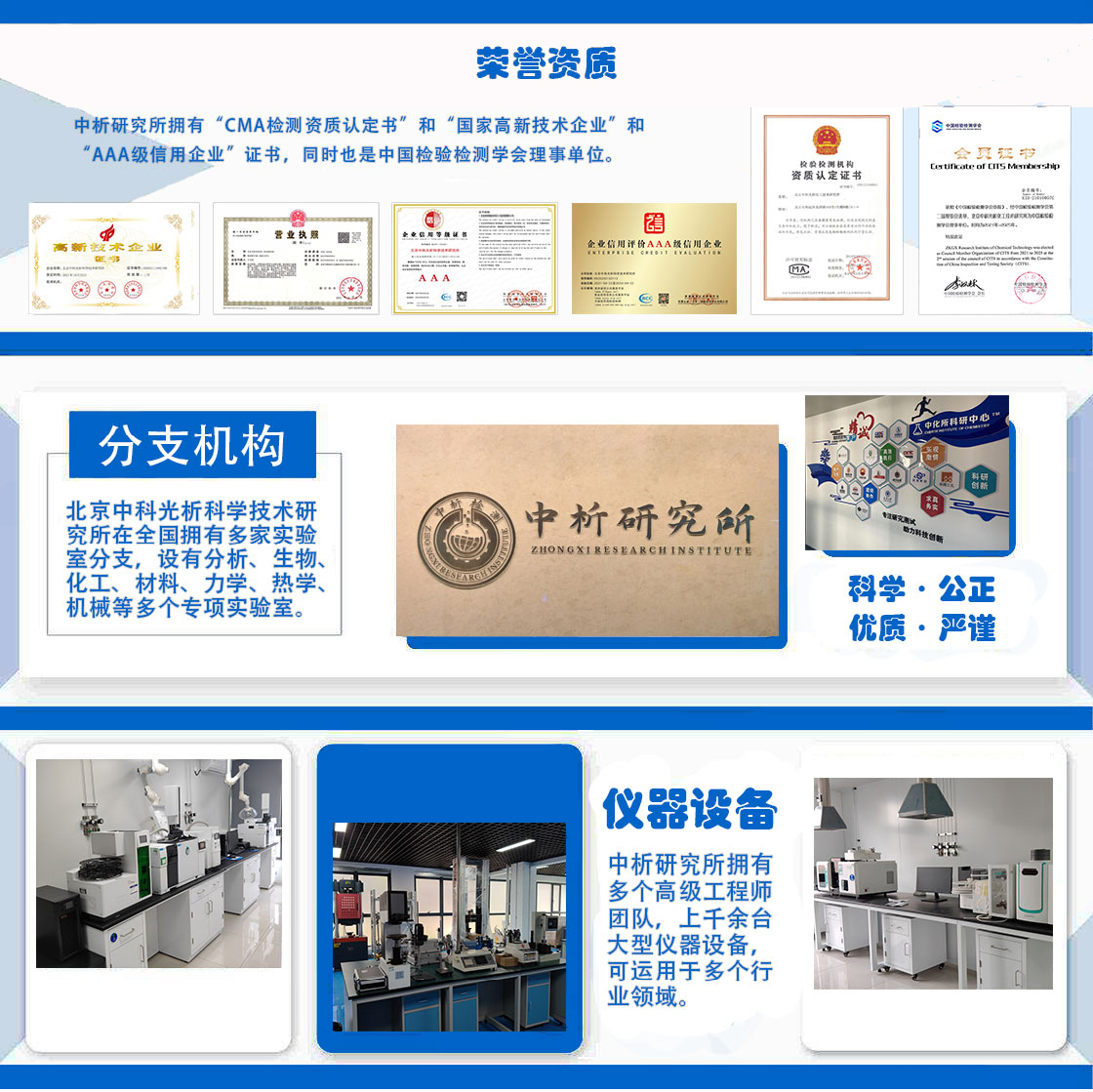
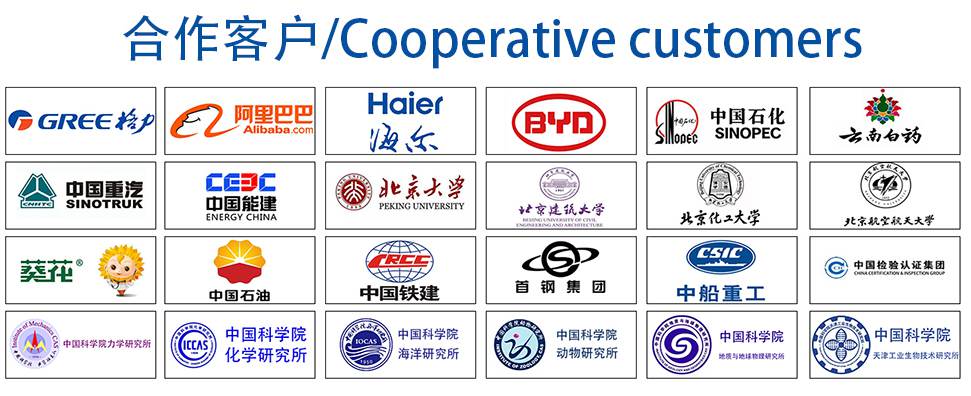