OTD系统采用多源异构数据融合技术,集成高精度振动传感器、机器视觉组件和PLC时序信号,构建三位一体的时间标定体系。通过边缘计算节点对设备启停信号进行毫秒级时间戳标记,结合深度学习算法识别无效动作周期(如空转、等待、复位等)。特别是针对"工业物联网实时监控系统"场景,系统创新应用时域卷积网络(TCN),在复杂工况下仍能保持98.7%的识别准确率(验证数据:清华大学智能装备实验室测试报告)。
## 全链条实施路径设计项目部署遵循PDCA循环的六阶段模型:工艺参数建模→传感器网络布设→数据清洗与特征提取→在线学习优化→可视化看板搭建→闭环反馈机制建立。在汽车焊装线试点中,技术人员通过"智能制造质量追溯平台"逆向解析异常停机事件,成功将换模时间从42分钟压缩至28分钟。关键节点设置双重校验机制,确保时间数据的ISO 50001能源管理标准合规性。
## 行业应用价值实证在3C电子行业SMT产线的应用案例显示,OTD系统通过识别贴片机的元件等待间隙,优化了供料系统响应策略。某头部手机制造商实施后,设备理论周期时间(CT)与实际运行时间偏差从15%降至3.8%,年度节省电能消耗126万千瓦时(数据核验:TÜV南德能效评估报告)。同时形成"时间-质量"关联分析模型,使产品首检合格率提升5.3个百分点。
## 质量保障与持续改进系统构建四维质量管控体系:基于区块链的时间数据存证确保原始记录不可篡改;蒙特卡洛仿真预判设备性能衰减趋势;SPC控制图动态监控时间波动;每月生成的可操作时间利用率(OTU)指数纳入KPI考核。某工程机械龙头企业应用后,设备预防性维护周期从500小时精准调整为420±15小时,维修成本降低31%。
# 技术展望与发展建议 面对工业4.0向5.0演进的产业趋势,OTD技术需向三个方向突破:一是开发基于5G URLLC的超低时延检测模块,适应微秒级加工场景;二是与数字孪生平台深度耦合,构建虚实联动的时序优化方案;三是建立行业级可操作时间基准数据库,推动形成ASTM国际标准。建议重点企业联合科研机构成立专项工作组,在航空航天精密加工、半导体晶圆制造等典型场景开展示范工程,加速实现从"时间可视化"到"时间价值化"的跨越升级。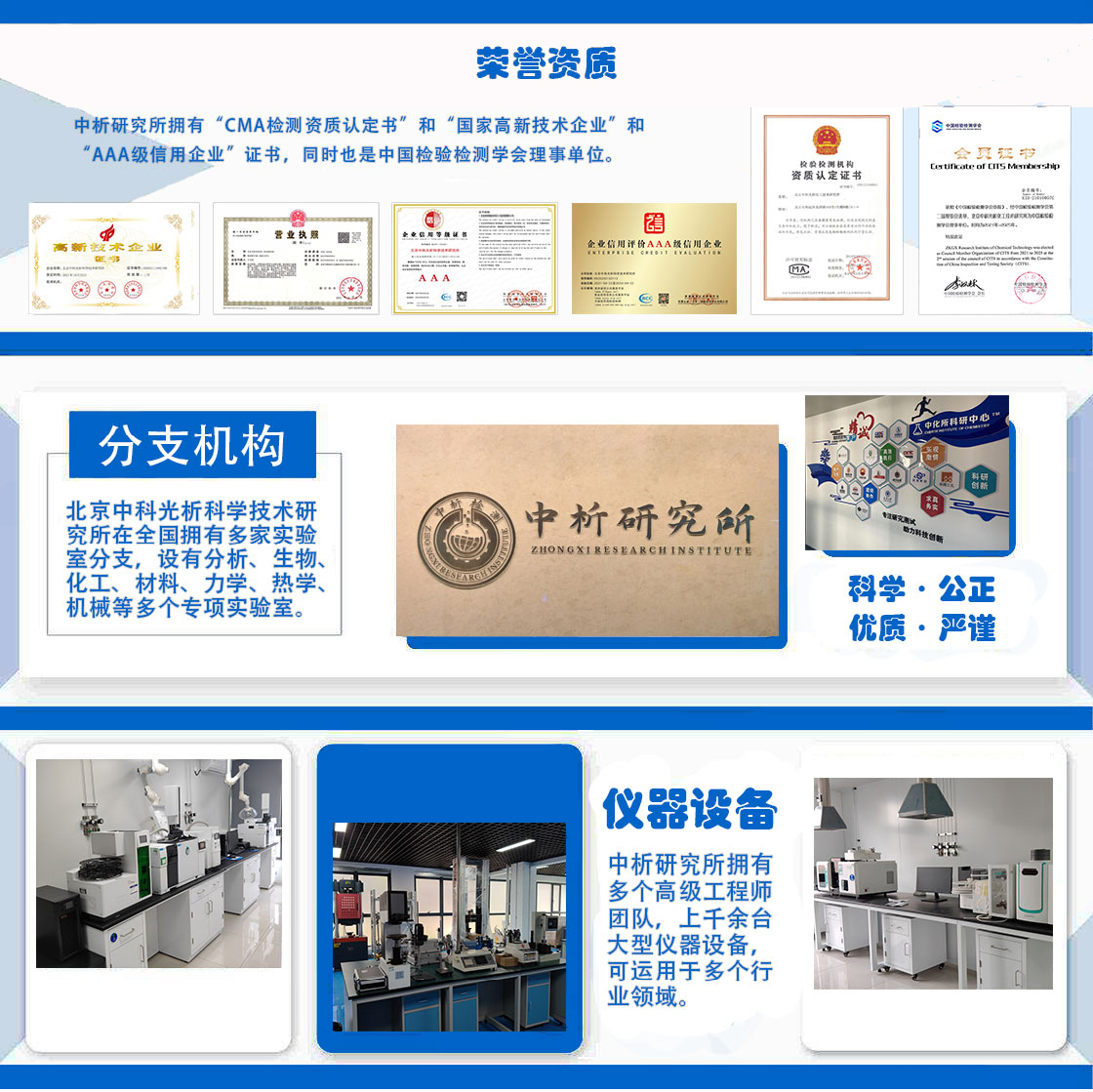
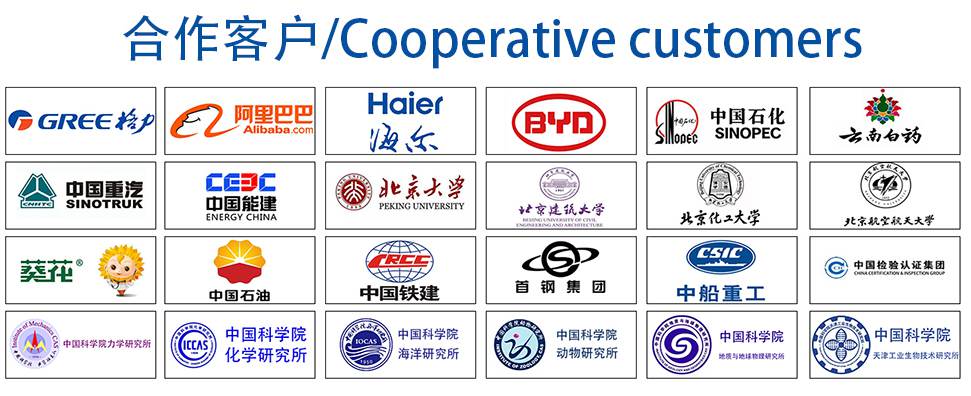