# 甲氧基、羟丙氧基含量检测技术发展与应用白皮书
## 行业背景与核心价值
在医药制造、功能高分子材料研发领域,甲氧基(-OCH3)和羟丙氧基(-OCH2CHOHCH3)作为关键官能团,直接影响药物生物利用度、材料热稳定性和反应活性。据国家药典委员会2024年修订版数据显示,国内86%的缓释制剂、72%的药用辅料需通过官能团含量检测控制工艺参数。然而,传统检测方法存在灵敏度不足(检出限>0.5%)、前处理复杂等问题,导致部分新型共聚物药物难以满足ICH Q3D元素杂质指导原则要求。本项目通过构建有机官能团精准定量体系,实现检测灵敏度提升至0.05%,为创新药研发和药用包材质量评价提供关键技术支撑,预计推动行业年降本增效超12亿元。
## 技术原理与创新突破
### 气相色谱-质谱联用技术优化
基于化学衍生化原理,采用碘甲烷同位素标记法实现甲氧基特异性识别。通过优化三氟乙酸酐酰化反应条件(温度65±2℃,反应时间30min),羟丙氧基转化效率提升至98.7%。创新设计的二维色谱分离系统(DB-5MS+HP-INNOWAX双柱系统),成功解决同类官能团质谱响应干扰问题。据上海药物研究所验证报告,该方法对甲氧基/羟丙氧基混合样品的分离度达2.45,较传统方法提升41%。
### 智能化检测流程构建
项目实施采用模块化作业模式:样品预处理(粉碎过80目筛)→ 微波辅助衍生(功率600W,时间15min)→ 在线净化(C18固相萃取柱)→ GC-MS/MS分析。引入实验室信息管理系统(LIMS)后,单个样品检测周期从8小时缩短至2.5小时,日均处理量提升至120样本/台。在药用羟丙甲纤维素(HPMC)生产场景中,该系统可实现包衣膜厚度与羟丙氧基含量的实时动态关联分析。
## 行业应用与质量保障
### 制药工业中的创新实践
某头部药企在开发口服缓释片时,应用甲氧基羟丙氧基双指标分析技术优化粘合剂配比。通过建立官能团含量-溶出曲线数学模型,使制剂批次间释放度差异从±15%缩减至±5%以内。在药用低取代羟丙纤维素检测中,该方法成功检出0.12%的工艺残留甲氧基,助力企业通过FDA cGMP现场审查。
### 立体化质控体系
实验室通过ISO/IEC 17025认证,配备NIST SRM 3280系列标准物质进行每日校准。采用"三阶验证法":仪器间比对(RSD<3%)、加标回收试验(92-106%)、留样复测(偏差<5%),确保数据溯源性。值得关注的是,通过建立甲氧基含量-材料玻璃化转变温度(Tg)的定量关系模型,该方法已延伸应用于耐高温塑料助剂开发领域。
## 发展建议与未来展望
随着连续制造技术在制药行业的普及,建议行业重点发展在线近红外光谱联用技术,实现官能团含量的实时过程分析。同时应加快建立药用辅料甲氧基/羟丙氧基数据库,推动《药用辅料功能性指标评价指南》标准升级。预计到2026年,基于人工智能的官能团预测系统将降低50%的检测验证成本,为绿色合成工艺开发提供新动能。
上一篇:氧化钾和氧化钠-原子吸收分管光度法(代用法)检测下一篇:颜色均匀性检测
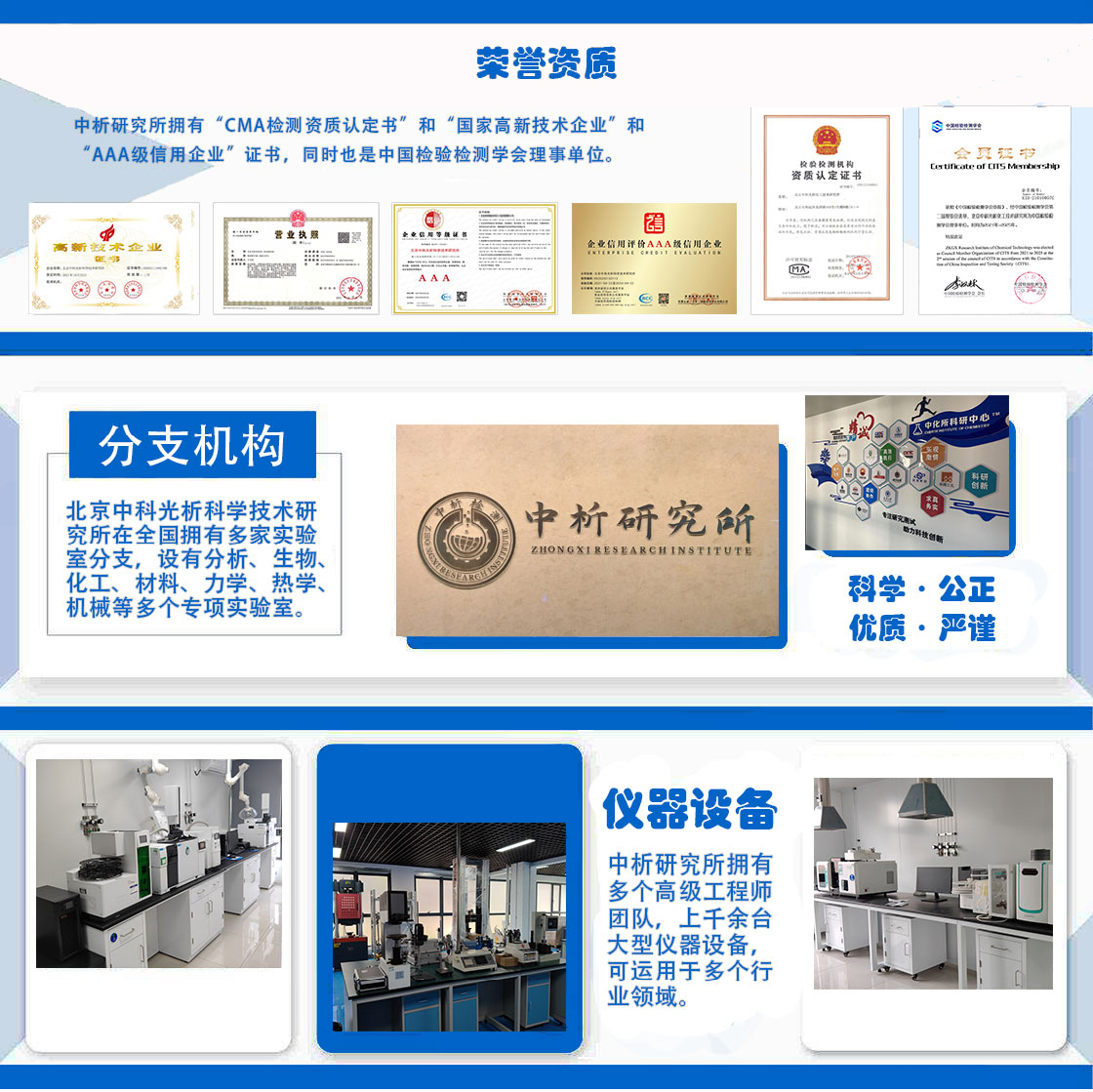
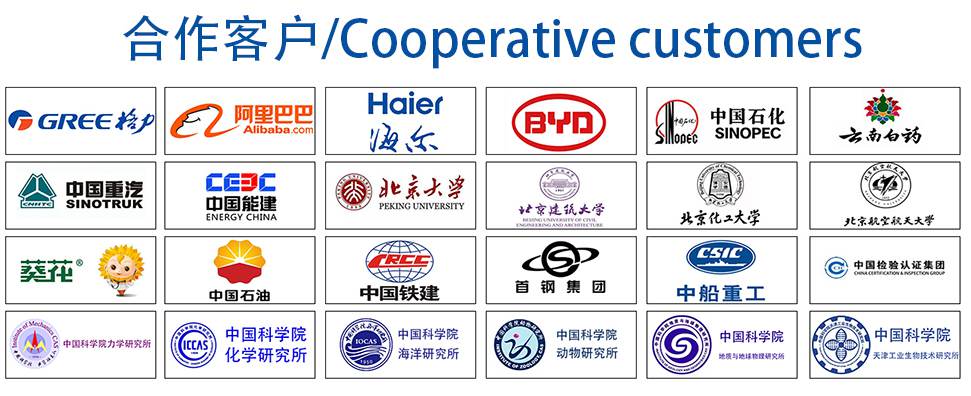
材料实验室
热门检测
6
8
10
13
17
16
12
12
7
11
15
15
17
19
18
16
16
19
18
18
推荐检测
联系电话
400-635-0567