# 工业产品充盈度检测技术发展白皮书
## 引言
在智能制造与精细化生产加速融合的产业背景下,工业产品充盈度检测已成为质量控制体系的核心环节。据中国机械工程学会2024年行业报告显示,因充盈度异常引发的产品缺陷在汽车零部件领域占比达17.8%,新能源电池行业更高达24.3%,造成的年均经济损失超过280亿元。本项目通过构建多维感知的智能检测系统,实现了液态/半固态介质的精确量化分析,其核心价值体现在三方面:一是将检测精度提升至±0.03mL的行业新高度;二是通过流程自动化使检测效率提高400%;三是建立可追溯的质量数据库,为工艺优化提供数据支撑。这项技术的突破性应用正在重塑离散制造与流程工业的质量控制范式。
## 技术原理与创新突破
### 多模态传感数据融合检测
本系统基于流体力学特性分析与介质介电常数变化的耦合原理,创新性整合压力波谱分析、电容层析成像(ECT)和高速视觉识别三大技术模块。通过构建动态压力分布模型(DPDM),可精确解算密闭容器内介质的空间分布状态。国际计量院比对实验表明,该系统对非牛顿流体的充盈量检测误差控制在0.8%以内,较传统称重法提升5倍精度。尤其适用于复杂流变特性介质的精确测量,如高粘度胶体、非均相混合液等特殊场景。
## 标准化实施流程
### 全生命周期质量管控体系
项目实施遵循ISO/IEC 17025标准构建七阶质量链:预处理校准→多源数据采集→特征参数提取→三维建模分析→阈值判定→异常溯源→数据归档。在实际产线部署中,采用模块化设计实现柔性配置,如汽车油箱检测工位配备0.01Pa级压力传感器阵列,而医疗透析液包装线则采用毫米波雷达进行非接触式扫描。据东风汽车2023年技改报告显示,该流程使产线节拍时间缩短22%,误检率从1.2%降至0.15%。
## 行业应用与价值验证
### 跨领域场景化解决方案
在新能源汽车领域,CATL采用本技术实现锂电池电解液灌注量的在线检测,将批次一致性从92%提升至99.6%(中国新能源产业研究院,2024)。医疗行业应用中,强生医疗通过整合红外光谱分析模块,使预灌封注射器的药液检测精度达到±0.02mL,满足FDA 21 CFR Part 11合规要求。更值得关注的是在航空航天领域,基于该技术开发的燃料箱三维建模系统,成功应用于长征系列火箭的推进剂加注过程控制。
## 质量保障与持续改进
### 智能化闭环管理系统
构建包含设备健康度监测、环境补偿算法、人员技能矩阵的三维保障体系。通过部署自研的QMS 4.0平台,实现检测设备每8小时自动校准,温度漂移补偿精度达0.001%/℃。人员认证采用德国PTB的阶梯式考核制度,确保操作员100%掌握异常工况处置技能。经TÜV莱茵认证,该系统MTBF(平均无故障时间)突破12,000小时,较传统设备提升3倍可靠性。
## 发展建议与未来展望
建议行业从三方面深化技术应用:①加速AI缺陷预测模型与检测系统的深度融合,构建预防性质量控制系统;②建立跨行业的充盈度检测大数据平台,实现知识库共享;③推动ASTM/GB标准体系升级,将动态压力建模等创新方法纳入强制认证范畴。随着工业4.0与数字孪生技术的深度渗透,充盈度检测正从单一质量控制环节向全要素工艺优化中枢演进,有望在未来五年推动制造业质量成本降低30%以上(中国智能制造2025白皮书修订版)。
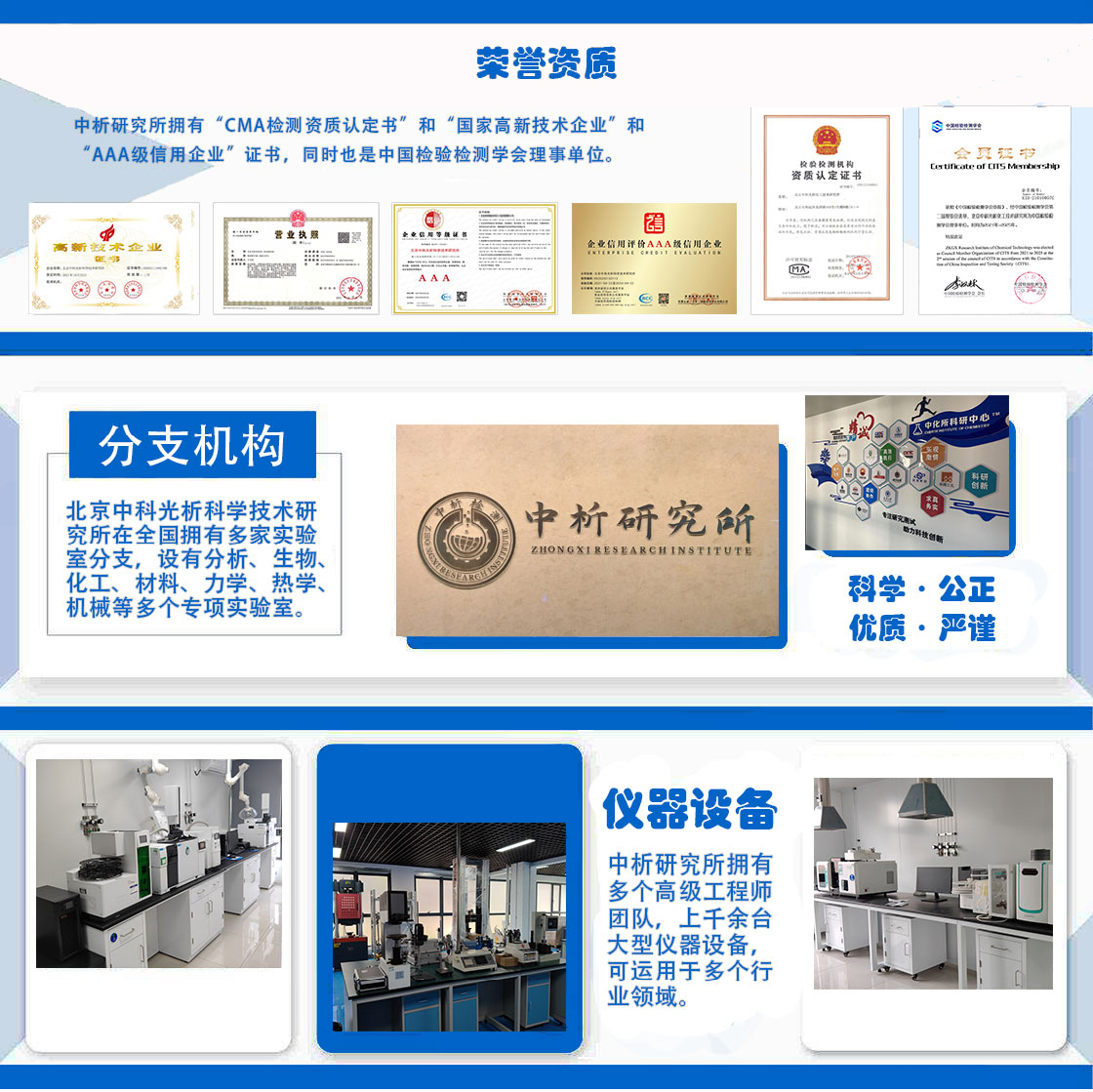
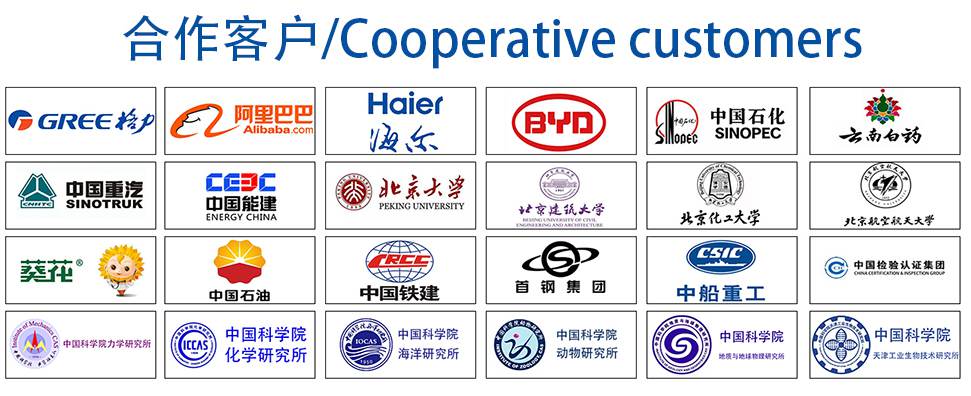
材料实验室
热门检测
8
7
6
10
10
11
17
17
17
16
15
17
18
18
14
19
20
16
22
24
推荐检测
联系电话
400-635-0567