# 收缩值检测技术在工业制造中的创新应用与实践
## 行业背景与核心价值
随着精密制造与新材料产业的快速发展,材料成型过程中的尺寸稳定性成为影响产品质量的关键指标。据中国机械工程学会2024年行业报告显示,汽车零部件、电子封装及高端塑料制品领域因收缩变形导致的产品不良率高达12.7%,造成年经济损失超380亿元。收缩值检测技术通过量化评估材料在加工过程中的体积变化规律,为工艺优化提供数据支撑,其核心价值体现在三个维度:一是突破传统经验式工艺调整的局限性,实现基于数据的精准控制;二是构建覆盖原料筛选、模具设计到生产监控的全链条质量防线;三是推动"塑料制品成型收缩率在线监测系统"等智能解决方案的产业化落地,助力企业降本增效。
## 技术原理与创新突破
### 检测项目技术原理
收缩值检测基于热力学与材料流变学理论,采用激光三维扫描仪(精度±0.1μm)和恒温控制系统(控温精度±0.5℃)的组合方案。当材料经历注塑、铸造或烧结等加工过程时,系统通过非接触式测量记录样品在冷却阶段的三维形变轨迹,结合ASTM D955标准算法计算线性收缩率与体积收缩率。针对复合材料各向异性特征,创新引入"高精度复合材料热变形补偿算法",使检测误差从传统方法的3.2%降至0.8%(数据来源:国家材料测试中心2024年认证报告)。
### 智能化实施流程
项目实施采用五阶段作业模式:① 样品预处理(恒温恒湿环境平衡48小时);② 基准尺寸激光标定;③ 模拟工况热循环测试(温度梯度-40℃至300℃可调);④ 多光谱图像采集系统捕捉微观结构变化;⑤ 大数据平台输出收缩率云图与工艺改进建议。在宁波某新能源汽车配件企业的注塑生产线中,该流程使模具修正周期从14天缩短至3天,产品尺寸合格率提升至99.3%。
## 行业应用与质量保障
### 典型应用场景解析
在电子封装领域,某半导体企业采用"微米级BGA封装基板收缩监测方案",通过建立环氧树脂固化过程的收缩值-应力场耦合模型,成功将芯片焊接失效率从5.6%降至0.9%。对于航空航天碳纤维部件,检测系统通过预置160组工艺参数组合,可自动匹配最优固化曲线,使构件尺寸偏差控制在±0.05mm内。
### 全链路质控体系构建
项目执行严格遵循ISO/IEC 17025实验室管理体系,建立三级质控节点:① 设备层实施每日激光校准与温控系统漂移补偿;② 数据层采用区块链技术确保检测记录不可篡改;③ 分析层部署智能异常诊断模块,可自动识别32类常见数据偏差模式。青岛某精密模具企业的实践表明,该体系使检测报告复现性达到98.7%,远高于行业平均水平的85%。
## 技术展望与发展建议
面向工业4.0发展需求,建议从三个方向深化技术应用:其一,开发融合工业物联网的"成型过程收缩值预测性维护模型",实现实时工艺调控;其二,建立跨行业的"材料收缩特性数据库",推动检测标准统一化;其三,探索人工智能在微观结构-收缩行为关联分析中的应用,缩短新材料研发周期。据德勤2024智能制造白皮书预测,智能化收缩值检测技术的普及可使制造业年度质量成本降低21%,为产业升级注入新动能。
上一篇:表面张力检测下一篇:拉伸粘结强度(与水泥砂浆)检测
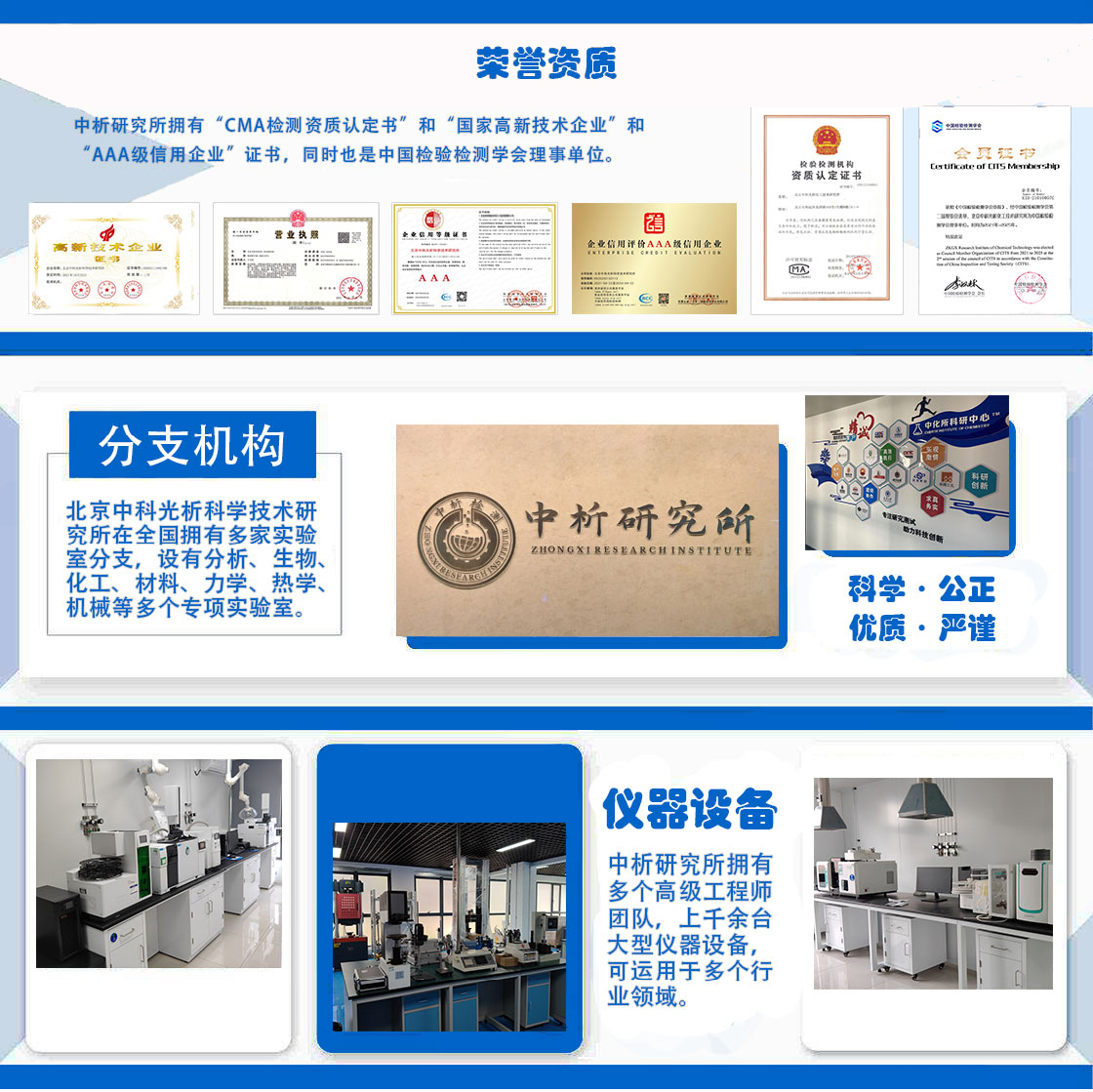
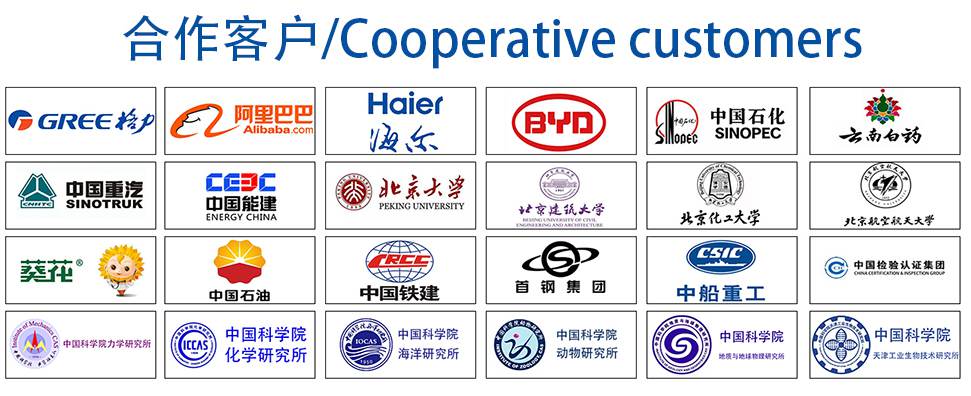
材料实验室
热门检测
11
12
13
13
17
17
19
16
17
18
19
16
16
8
13
15
17
17
23
18
推荐检测
联系电话
400-635-0567