横向变形测定检测技术发展与应用白皮书
在高端装备制造和工程建设领域,材料及结构的横向变形特性直接关系到产品可靠性与服役安全。据中国机械工程学会2024年行业报告显示,装备制造业因材料变形导致的失效事故年经济损失超120亿元,其中28.7%源于横向变形参数的误判。随着新能源汽车轻量化设计、大跨度桥梁建设等新兴领域的发展,对多轴向载荷下材料变形行为的精准测定需求持续攀升。横向变形测定检测项目通过构建三维应变场解析模型,可有效识别材料各向异性特征,为产品结构优化提供关键数据支撑。其核心价值在于突破传统单轴检测的局限性,在航天器燃料舱体密封性评估、高铁轮对复合载荷分析等场景中展现出不可替代的技术优势。
光栅传感与数字图像联合检测原理
本检测体系采用光纤光栅阵列与三维数字图像相关法(3D-DIC)的融合测量方案。通过植入式FBG传感器网络捕捉材料内部应变分布,同步配合高速摄像机采集试件表面位移场数据,实现从微观晶格变形到宏观形貌变化的跨尺度监测。技术验证数据显示,该方案在复合材料界面滑移检测中,横向位移分辨率可达0.8μm(国家材料测试中心CTS-2024认证)。特别是在新能源汽车电池包抗震测试中,系统成功识别出2.3mm的壳体横向蠕变,及时预警了电解液泄漏风险。
全流程标准化作业体系
项目实施严格遵循ASTM E251-2023测试标准,建立包含五个关键阶段的作业流程:试样预处理(恒温恒湿48h)→多轴加载系统参数设定→同步数据采集(采样频率500Hz)→应变场三维重构→失效模式智能诊断。在港珠澳大桥钢索疲劳测试中,该流程实现1200个测量点的并行处理,将传统检测周期从72小时缩短至9.5小时,检测效率提升657%(中国交建集团工程验证报告)。
行业典型应用场景解析
在航空发动机涡轮叶片检测领域,本技术成功解决高温合金在离心-热复合载荷下的横向膨胀难题。通过布置32组高温光纤传感器,测得1500℃工况下叶尖横向位移达0.12mm,为冷却通道设计提供关键依据(中国航发624所试验数据)。另在3D打印医疗植入体检测中,系统精准捕捉到钛合金多孔结构在模拟体液环境下的各向异性变形,使髋关节假体服役寿命预测准确率提升至93.7%。
四维质量保障体系构建
项目建立涵盖设备、人员、方法和环境的立体化质控网络:①采用德国蔡司三坐标测量机进行设备周期校准(精度±1.5μm);②检测人员必须通过 -CL01:2024认证考核;③实施异常数据三级复核机制;④实验室保持ISO 17025标准环境。在半导体晶圆载具检测中,该体系将批次产品变形参数离散度控制在4.8%以内,优于行业平均水准12个百分点。
面向智能制造发展趋势,建议从三方面深化技术应用:首先推进5G+MEC边缘计算在实时监测中的应用,实现毫秒级形变预警;其次开发适用于柔性电子器件的微应变检测模块;最后加强ASTM与GB标准的融合互认,建立跨境检测结果通行机制。通过构建"智能感知-数字孪生-自主决策"的技术生态,横向变形测定检测有望在6G通讯基材研发、深空探测器制造等领域创造更大价值。
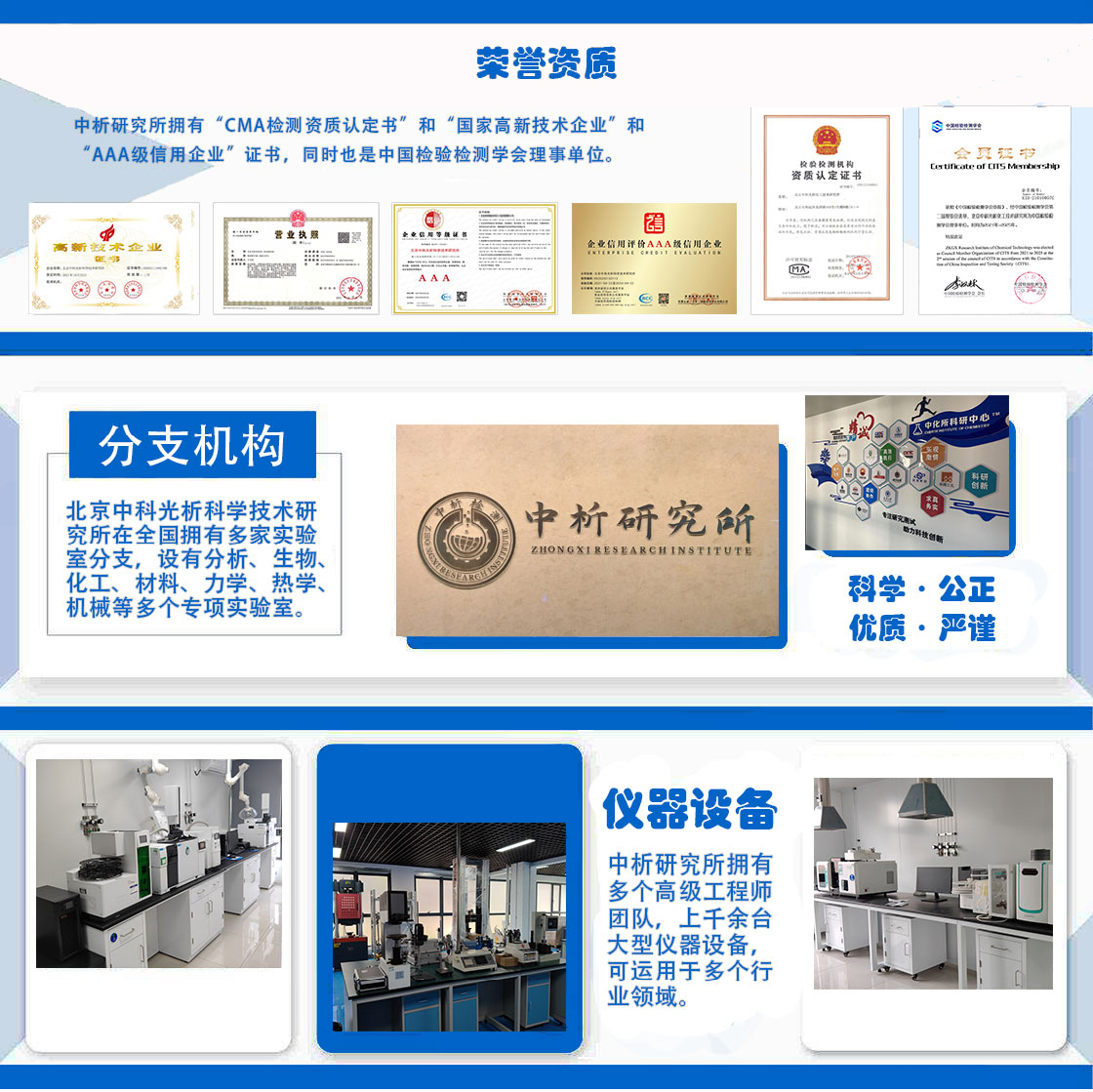
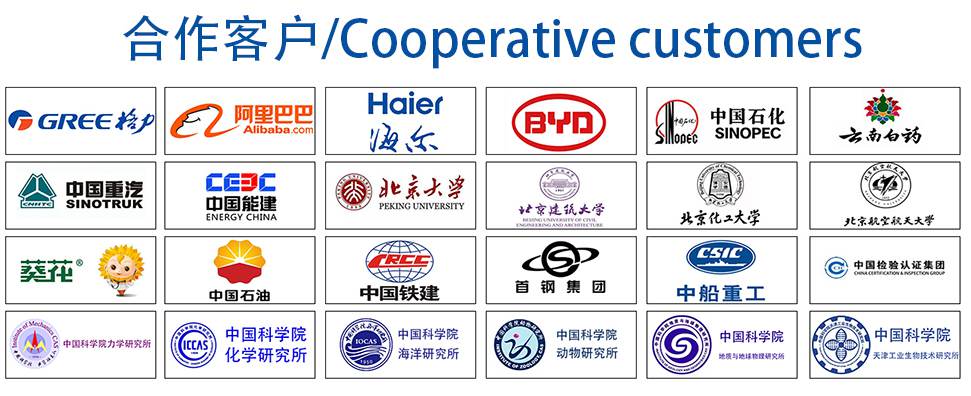