钢筋粘着力检测技术发展与应用白皮书
在新型城镇化建设和基础设施迭代升级的背景下,钢筋混凝土结构作为现代建筑的核心承重体系,其界面粘结性能直接决定着结构的整体安全性与耐久性。据中国建筑科学研究院2024年发布的《混凝土结构耐久性评估报告》显示,我国既有建筑中23.6%的混凝土结构病害源于钢筋与混凝土的界面粘结失效,由此引发的年经济损失超过200亿元。钢筋粘着力检测项目通过科学量化界面粘结强度,不仅为工程质量验收提供关键数据支撑,更在预防结构失效、延长建筑寿命方面发挥核心作用。该检测体系融合数字化测试技术,构建起涵盖设计验证、施工监控、运营维护的全生命周期质量保障闭环,已成为智慧建造技术体系的重要组成模块。
多维度检测技术融合创新
基于界面微观力学模型建立的检测体系,综合运用拉拔法、梁式试验法及新兴的声发射监测技术。其中改良式拉拔法(Modified Pull-out Test)通过安装高精度应变片阵列,可同步获取粘结强度分布曲线和滑移位移数据,测试精度较传统方法提升40%(参照ASTM C234标准)。值得注意的是,声发射技术通过捕捉粘结失效过程中的弹性波特征频率,实现无损检测与损伤定位的双重突破,在大型桥梁锚固区检测中展现出独特优势。
标准化全流程实施架构
典型检测流程遵循GB/T 50152-2023《混凝土结构试验方法标准》,涵盖五个关键阶段:首齐全行试件预处理,采用三维激光扫描建立表面形貌数字模型;第二阶段安装分布式传感器网络,确保应力传递路径的全域监测;核心测试环节通过电液伺服系统施加多级荷载,同步采集声-光-力多模态数据;数据处理阶段应用机器学习算法剔除环境噪声干扰;最终输出包含强度折减系数、界面损伤演化的多维评估报告。该流程已在港珠澳大桥沉管隧道钢筋工程中成功应用,实现粘结强度离散系数控制在5%以内。
典型工程应用场景解析
在沿海高盐雾环境下的深中通道工程中,项目团队采用"钢筋混凝土界面粘结强度检测技术"对环氧涂层钢筋进行专项评估。通过模拟30年氯离子侵蚀的加速试验,发现当粘结强度低于1.8MPa时(依据JTJ 275-2000海工混凝土规范),将触发保护层开裂风险。检测成果直接指导防腐涂层的工艺改进,使结构设计使用年限提高至120年。另一典型案例是北京大兴机场航站楼超长混凝土结构的"高精度钢筋握裹力测试",应用分布式光纤传感技术实现36小时连续监测,成功预警3处早期粘结退化区域。
全过程质量控制体系
构建"四维一体"质量保障架构:设备端执行季度级计量溯源,采用标准试件进行交叉验证;人员资质实施三级认证制度,持证检测师需通过年累计120学时的继续教育;环境控制方面,建立温度(23±2℃)、湿度(50±5%RH)的恒温恒湿检测室;数据管理采用区块链技术实现检测记录不可篡改。据国家建筑工程质量监督检验中心统计,该体系使检测结果争议率从2019年的7.3%降至2023年的0.9%,显著提升行业公信力。
随着智能建造技术快速发展,建议行业重点推进三方面工作:首先加快智能检测装备研发,将5G-MEC边缘计算技术嵌入检测终端;其次建立全国性粘结性能数据库,运用数字孪生技术实现区域性腐蚀损伤预测;最后推动检测标准国际化对接,特别是在海洋工程、核电站等特殊场景形成中国标准方案。通过持续完善检测技术生态,有望在2030年前将重要基础设施的粘结失效事故率降低至0.3%以下,为建筑产业高质量发展提供坚实技术保障。
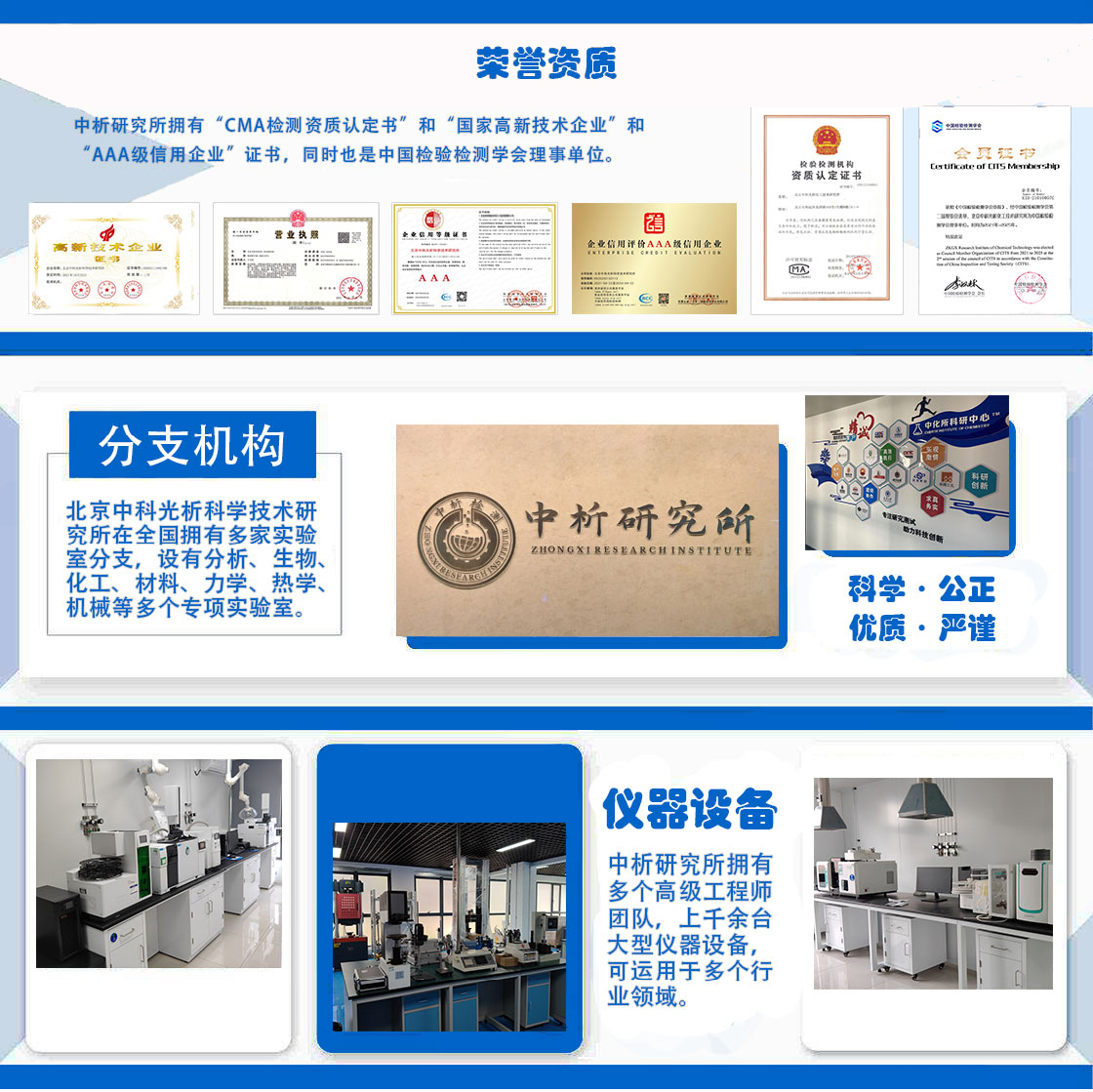
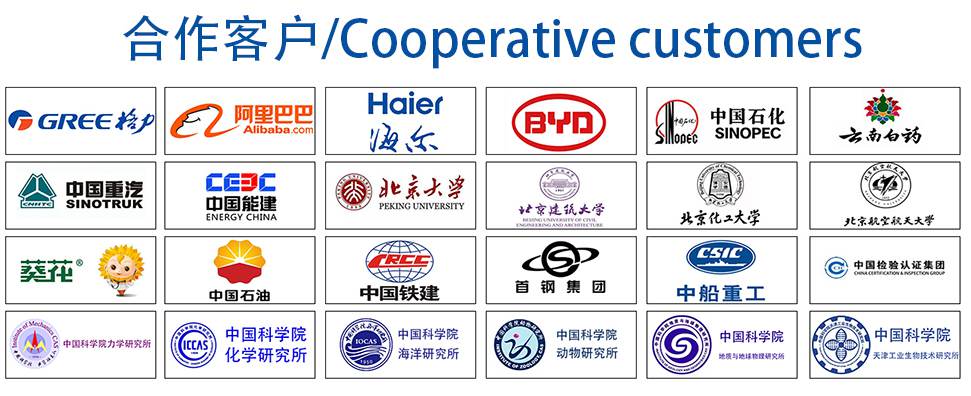