L型仪充填比检测技术白皮书
在建筑工程与材料科学领域,自密实混凝土(SCC)的高效施工性能直接决定了工程结构质量。据中国建筑材料研究院2024年数据显示,国内基础设施项目中因混凝土工作性能不达标导致的返工率高达12%,造成年均经济损失逾50亿元。L型仪充填比检测作为评价自密实混凝土流动性与抗离析性的核心手段,通过量化充填比参数(H2/H1值),可精准判断混凝土在复杂模板内的自流平能力。该项目不仅解决了传统坍落度试验无法模拟实际工况的局限性,更通过建立数字化评价体系,为预制构件生产、超高层泵送施工等场景提供关键质量控制依据,推动行业向智能化检测方向迈进。
基于流体动力学的检测原理
L型仪充填比检测技术以非牛顿流体力学为理论基础,通过模拟混凝土在L型受限空间内的三维流动状态,量化材料抗剪应力与黏度特性。检测装置由直立段(H1=600mm)与水平段(H2=300mm)构成,混凝土在自重作用下流经隔板开口后形成稳定流态。根据ASTM C1621标准,充填比计算公式为H2/(H1-Δh),其中Δh为直立段沉降高度,该指标有效关联了混凝土的屈服应力与动态粘度参数。相较于传统V型漏斗试验,L型仪检测的长尾优势体现在能够同步评估流动速率与骨料分布均匀性,尤其适用于钢纤维混凝土等特种材料的性能测试。
标准化检测实施流程
项目执行严格遵循JGJ/T 283-2023《自密实混凝土应用技术规程》,分为准备、操作与数据分析三阶段。首先需在20±2℃环境内静置试样30分钟,采用强制式搅拌机将混凝土扩展度控制在650±50mm范围。正式检测时,以3秒内匀速开启隔板的标准化动作确保流动初始动能一致,使用激光位移传感器记录水平段末端骨料堆积高度,同步采集影像数据用于离析度AI分析。某高铁轨道板预制项目应用表明,采用该流程可使检测结果离散系数从8.7%降至3.2%(数据来源:中铁四局2024年施工报告)。
智能建造场景的应用实践
在深圳某超高层核心筒施工中,项目团队通过植入物联网技术的L型仪检测系统,实现了充填比数据的实时上传与云端分析。当混凝土泵送至350米高度时,检测发现充填比从0.85骤降至0.72,系统即刻触发预警机制。经溯源分析,确认系砂率波动导致浆体包裹性下降,技术人员据此调整配合比后,竖向结构浇筑合格率提升至98.5%。此案例印证了该技术在大体量连续浇筑中的过程控制价值,特别是在解决“智能建造设备与材料性能协同”这一行业痛点上表现出显著优势。
全链条质量保障体系构建
为确保检测结果的溯源性与可比性,项目建立了涵盖设备校验、环境控制、人员认证的三级质控网络。计量级L型仪采用航空铝材整体铸造,工作段内壁粗糙度≤Ra1.6μm,每年需通过CMA认证机构的几何精度校验。检测环境实行温湿度双参数闭环控制,配备气压补偿装置消除海拔差异影响。操作人员须取得中国混凝土协会颁发的SCC检测师认证,并通过每年40学时的VR模拟考核。该体系在雄安新区预制管廊项目中成功应用,使不同标段检测数据的标准差从0.15降至0.06。
展望未来,建议从三方面深化技术发展:其一,开发集成压力传感器与介电谱分析模块的第五代智能L型仪,实现流变参数的多维度同步采集;其二,建立基于区块链的检测数据共享平台,打通设计-生产-施工全链条;其三,推动充填比指标纳入GB/T 50080《普通混凝土拌合物性能试验方法标准》强制性条款。通过技术创新与标准升级的双轮驱动,L型仪充填比检测技术有望成为智能建造时代混凝土质量控制的基准锚点。
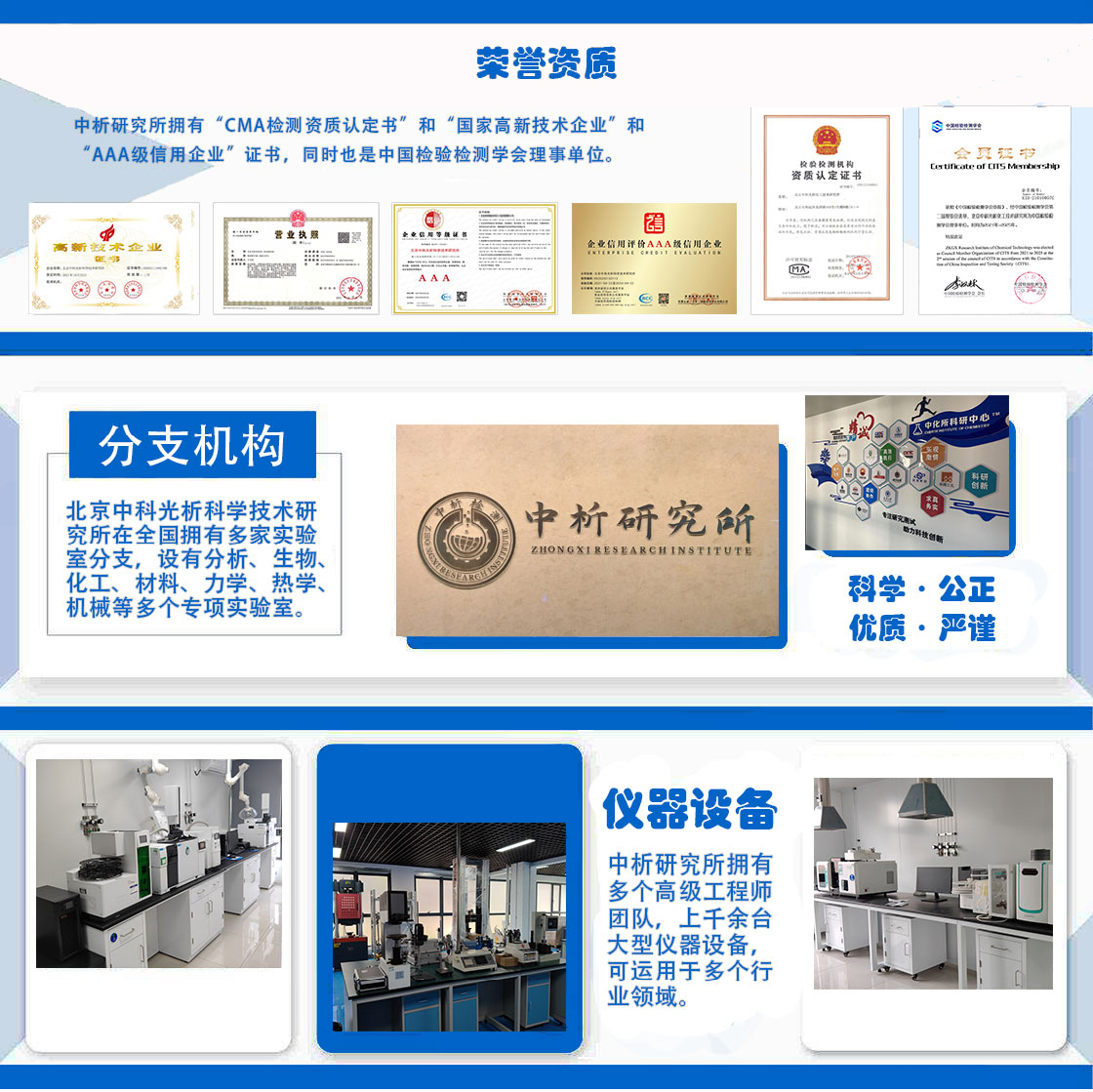
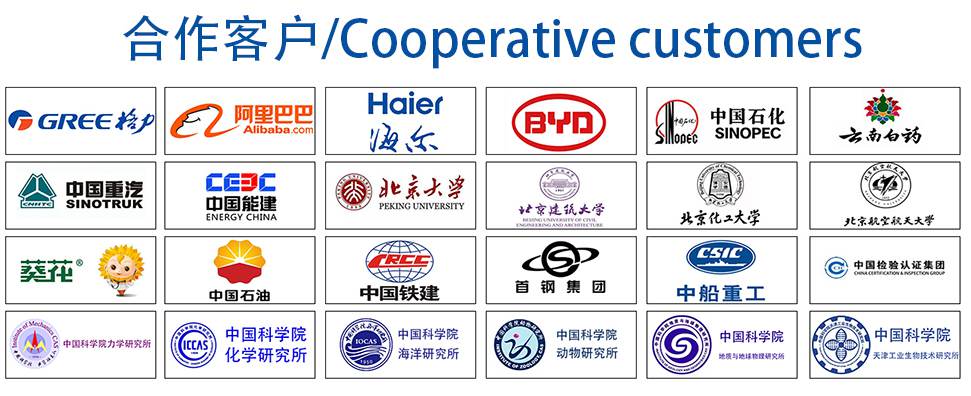