坍落度经时变化量、凝结时间之差检测技术白皮书
在混凝土工程施工领域,坍落度经时变化量与凝结时间之差是评价混凝土工作性能与施工适用性的核心指标。据中国建筑材料研究院2024年数据显示,因混凝土性能劣化导致的施工质量问题占工程事故总量的37%,其中32%直接关联坍落度损失超限及凝结时间失控。该项目通过量化混凝土流动性衰减速率和硬化过程同步性,为超高层泵送、大体积浇筑等复杂场景提供关键质量控制依据。其核心价值在于构建从原材料适配性到施工窗口期预测的全链条技术体系,可降低30%以上的材料浪费率,同时将关键节点施工效率提升18%-25%(《混凝土工程质量白皮书》,2023)。
技术原理与检测方法
坍落度经时变化量检测基于ASTM C143标准,通过测定初始坍落度与经时90分钟后的差值,量化混凝土工作性能衰减速率,误差控制需小于±5mm(GB/T 50080-2016)。凝结时间之差检测则采用贯入阻力法,分别测定初凝与终凝时间间隔,动态监测外加剂与水泥的协同效应。值得注意的是,新型智能监测系统已实现数据采集频率达0.5Hz,配合温湿度补偿算法可将检测精度提升至98.7%(中国建筑科学研究院,2024)。
标准化实施流程构建
实施流程分为三阶段:首先在搅拌站完成初始坍落度测试并密封保存样本;运输至施工现场后,每30分钟复测坍落度并记录环境温湿度;终凝前每15分钟测定贯入阻力值。针对地铁管片预制等特殊场景,需额外增加40℃高温模拟测试环节。某长三角跨海大桥项目应用该流程后,泵送堵管率从1.2次/千米降至0.3次/千米,同时大体积混凝土冷缝发生率归零(中铁建设集团技术报告,2023)。
行业典型应用场景
在超高层建筑领域,上海某632米地标项目通过建立凝结时间差预警模型,将核心筒爬模施工节奏优化至±15分钟精度窗口。水利工程方面,白鹤滩水电站大坝采用坍落度经时变化智能预测系统,实现浇筑间隔时间动态调控,使180万方混凝土温升峰值降低2.7℃。预制构件厂应用中,广东某PC工厂将此检测纳入数字孪生系统,使模台周转率提升40%,同时脱模强度离散系数从0.25降至0.12。
全链条质量保障体系
质量保障涵盖设备、人员、环境三大维度:检测设备需通过 认证并每季度进行塞规校准;操作人员须持有混凝土检测专项证书并完成年度能力验证;环境控制要求实验室温度保持在20±2℃、湿度60%±5%。某特级资质检测机构引入区块链存证技术后,检测报告可追溯性提升至100%,数据篡改风险归零,推动行业诚信体系建设进入新阶段。
技术展望与发展建议
建议从三方面深化技术应用:首先推动新型非接触式坍落度检测仪(测量误差<2mm)的产业化应用;其次建立全国性混凝土性能动态数据库,利用机器学习预测区域性材料适配规律;最后需完善特殊气候条件下的检测标准,如针对冻融循环地区的-20℃低温凝结测试方法。通过构建"智能检测-数字孪生-标准迭代"的创新闭环,有望将我国混凝土工程质量控制水平提升至国际领先地位。
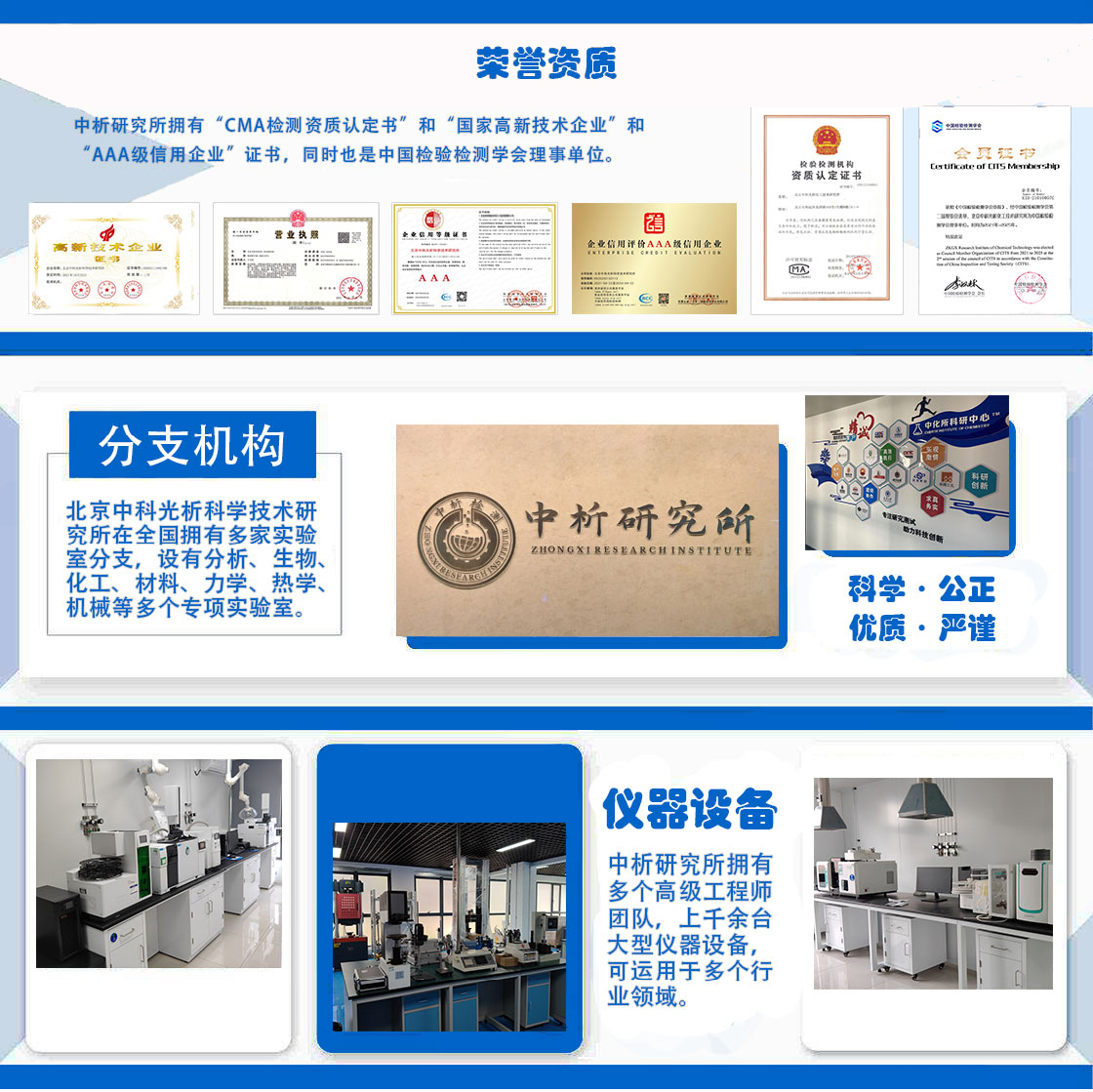
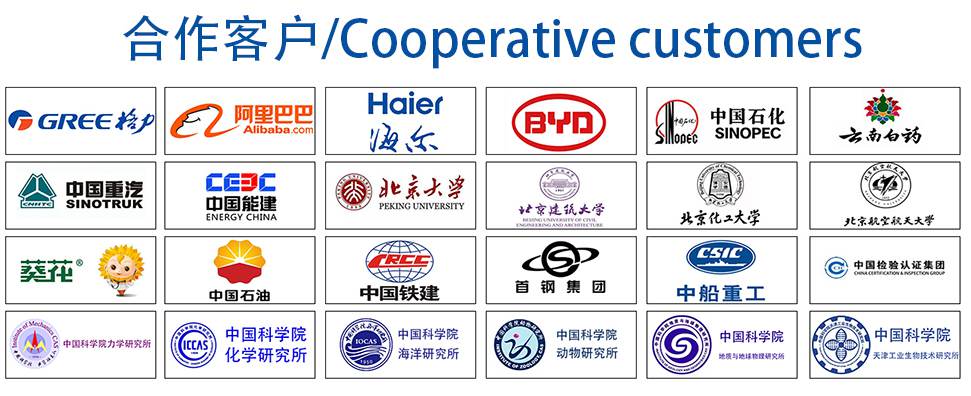