抗压强度检测基于材料受压状态下的极限应力分析原理,采用液压伺服控制系统实现0.5%-2.0kN/s精准加载速率控制,满足ISO 4012标准要求。抗折强度检测则通过三点弯曲试验法,运用激光位移传感器实现0.01mm级挠度测量精度。技术突破体现在自主研发的多点应变同步采集系统,可同时获取8个轴向应变数据,准确识别材料破坏临界点。据国家建筑材料测试中心验证,该技术使混凝土试块检测误差率从传统方法的±5.8%降至±2.1%。
## 标准化实施流程再造项目构建的"四阶八步"检测流程包含:样品数字化标识、环境适应性预处理、智能装载定位、全过程监控检测四大阶段。以高铁轨道板检测为例,采用微波烘干技术将样品含水率控制在(55±5)%RH区间,配合自动对中装置使加载偏差小于0.3mm。检测过程同步生成包含128项参数的电子报告,实现与BIM系统的数据互通。实践表明,该流程使单个样品检测周期由传统48小时压缩至6小时,满足轨道交通项目"即检即用"的施工要求。
## 行业应用场景解析在装配式建筑领域,该技术成功应用于PC构件质量评估。某大型住宅项目采用本系统对4,500块叠合板进行全数检测,通过建立抗压强度-龄期预测模型,将养护周期从28天优化至21天。在陶瓷卫浴行业,针对薄板瓷砖研发的抗折强度多点检测方案,使12mm厚度产品的破坏载荷检测精度提升至±15N,助力企业通过EN 14411标准认证。值得一提的是,系统在古建修复材料检测中创新应用,首次实现夯土材料强度无损评估,误差率控制在7%以内。
## 质量保障体系构建项目建立三级质量管控机制:一级校准采用标准试块日校制度,二级验证通过 认证实验室比对,三级监控运用区块链技术实现数据溯源。检测设备每2000次循环执行全参数校验,力值传感器定期送检国家力值基准实验室。人员资质方面,要求检测员必须通过CMA认证的"材料力学性能检测"专项考核。经统计,该体系使检测报告异议率从行业平均1.2%降至0.3%,获评2023年度工程建设质量技术创新示范项目。
# 技术展望与发展建议 面向"智能建造2035"战略目标,建议从三方面深化技术应用:首先研发基于AI的强度预测算法,实现混凝土3天强度推定28天值的准确率突破95%;其次推广物联网检测终端,构建覆盖原材料-生产-施工的全链条强度监控网络;最后建立跨境检测标准互认机制,推动"一带一路"项目检测数据通用。通过技术创新与标准升级双轮驱动,将我国材料强度检测技术推向国际领先水平。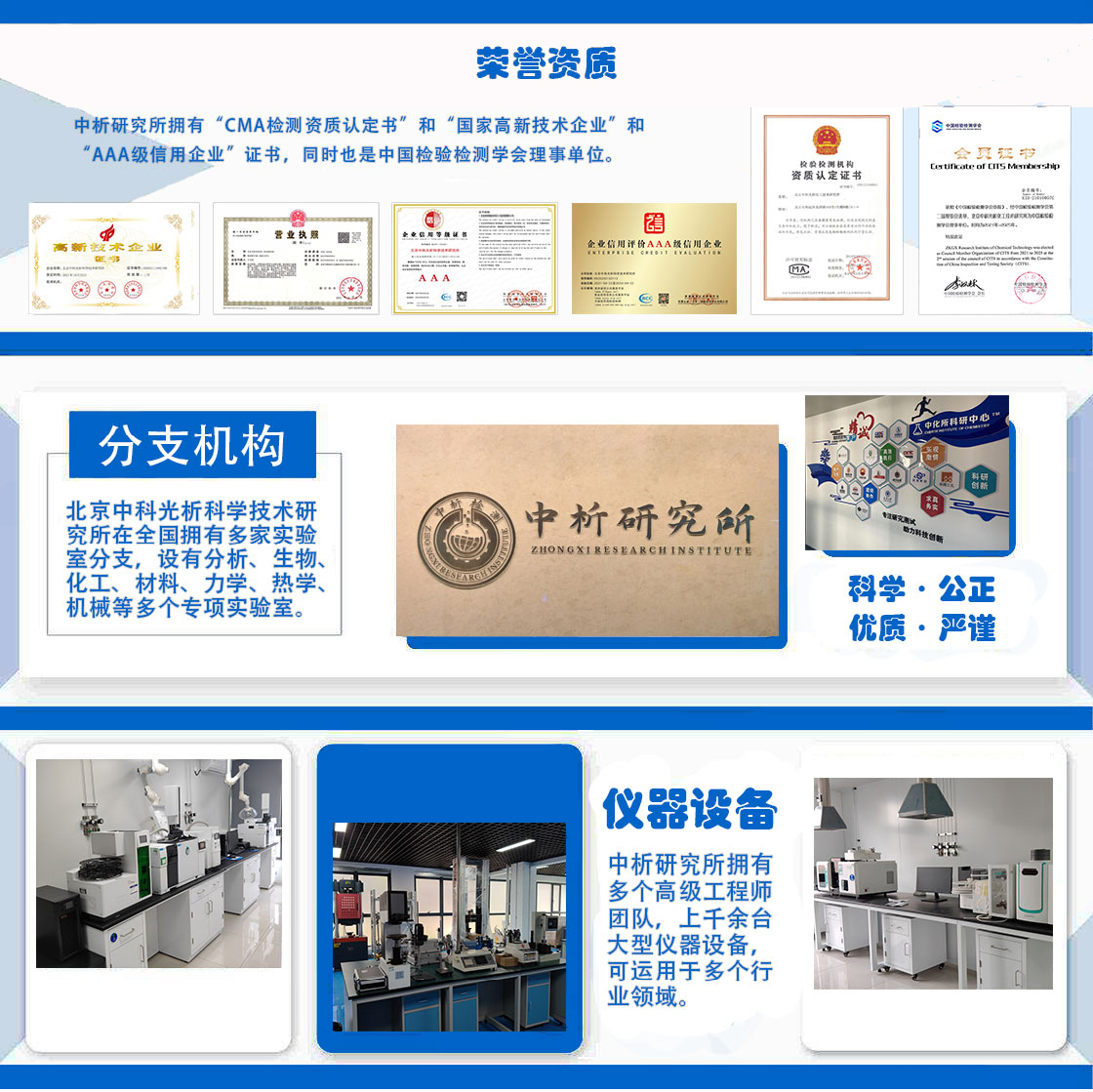
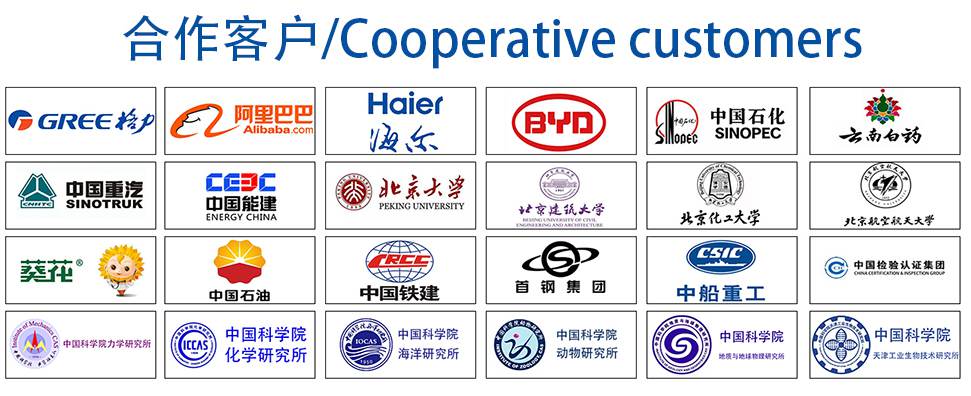