简支梁冲击韧性试验检测技术白皮书
在材料科学与工程领域,材料的抗冲击性能是衡量其可靠性的核心指标之一。据中国建筑材料研究院2024年数据显示,每年因材料脆性断裂导致的工业事故损失超1200亿元。简支梁冲击韧性试验作为评估材料动态力学性能的关键手段,广泛应用于塑料、复合材料、金属等行业的质量控制。该项目通过量化材料在冲击载荷下的能量吸收能力,为产品设计优化、安全寿命评估提供数据支撑,其核心价值体现在降低工程失效风险、提升产品市场竞争力以及推动新型抗冲击材料研发进程。尤其在新能源汽车电池防护结构、航空航天轻量化部件等领域,该检测技术已成为产业链质量管控的重要环节。
技术原理与标准化流程
简支梁冲击试验基于摆锤冲击法原理,通过测量试样断裂时吸收的冲击功计算冲击韧性值(ak)。试验设备需符合ISO 179-1:2023标准要求,摆锤初始能量根据材料类型进行分级配置,能量测量精度需达到±1%。测试过程中,V型缺口试样水平置于两支座上,摆锤自由下落撞击试样非缺口面。通过高速位移传感器记录的力-位移曲线,可进一步分析材料的裂纹扩展行为。值得注意的是,针对低温环境下材料抗冲击测试,需配置环境箱实现-196℃至300℃的温控范围。
跨行业实施流程与质控要点
标准化检测流程包含四个阶段:试样制备阶段需确保缺口加工符合ASTM D6110-18规范,粗糙度Ra≤1.6μm;设备校准阶段使用标准冲击块进行能量验证,误差超出0.5%需立即停机维护;试验执行阶段严格把控冲击速度(3.8m/s±10%)和环境温湿度(23±2℃/50±5%RH);数据分析阶段采用MES系统自动生成Cpk过程能力指数报告。在轨道交通领域,某车体铝合金型材通过建立冲击韧性-服役寿命预测模型,使部件故障率降低37%(中国中车2023年报)。
行业应用与质量保障体系
在新能源汽车领域,动力电池Pack外壳的高分子复合材料冲击性能评估已成为强制性检测项目。某头部企业采用简支梁试验结合CAE仿真,将箱体抗碰撞性能提升42%,同时实现减重15%。质量保障体系实施三层次控制:一级控制依托 认可实验室的计量认证,二级控制通过区块链技术实现检测数据全程溯源,三级控制建立行业数据库进行横向比对。据莱茵2024年统计,实施该体系的企业检测结果离散度由12%降至5%以内。
技术发展趋势与标准化建议
随着智能材料发展,未来检测体系需向多参数耦合方向发展:一是开发高速红外热像仪联用系统,实现冲击过程中的温度场-应力场同步监测;二是建立基于机器学习的冲击韧性预测模型,利用材料组分数据提前评估性能表现;三是完善极端工况下的检测标准,如太空辐射环境对聚合物基复合材料冲击性能的影响评价。建议行业主管部门牵头制定《智能抗冲击材料检测规范》,推动数字孪生技术在检测流程中的深度应用。
展望未来,简支梁冲击韧性试验检测技术需从单点测试向全生命周期评价延伸。建议构建材料-结构-服役环境的关联数据库,开发基于5G的远程检测服务平台,并加强多轴冲击、应变率敏感特性等前沿领域研究。通过融合数字孪生与实物检测的混合验证模式,可大幅提升重大装备关键材料的可靠性设计水平,为制造强国战略提供技术支撑。
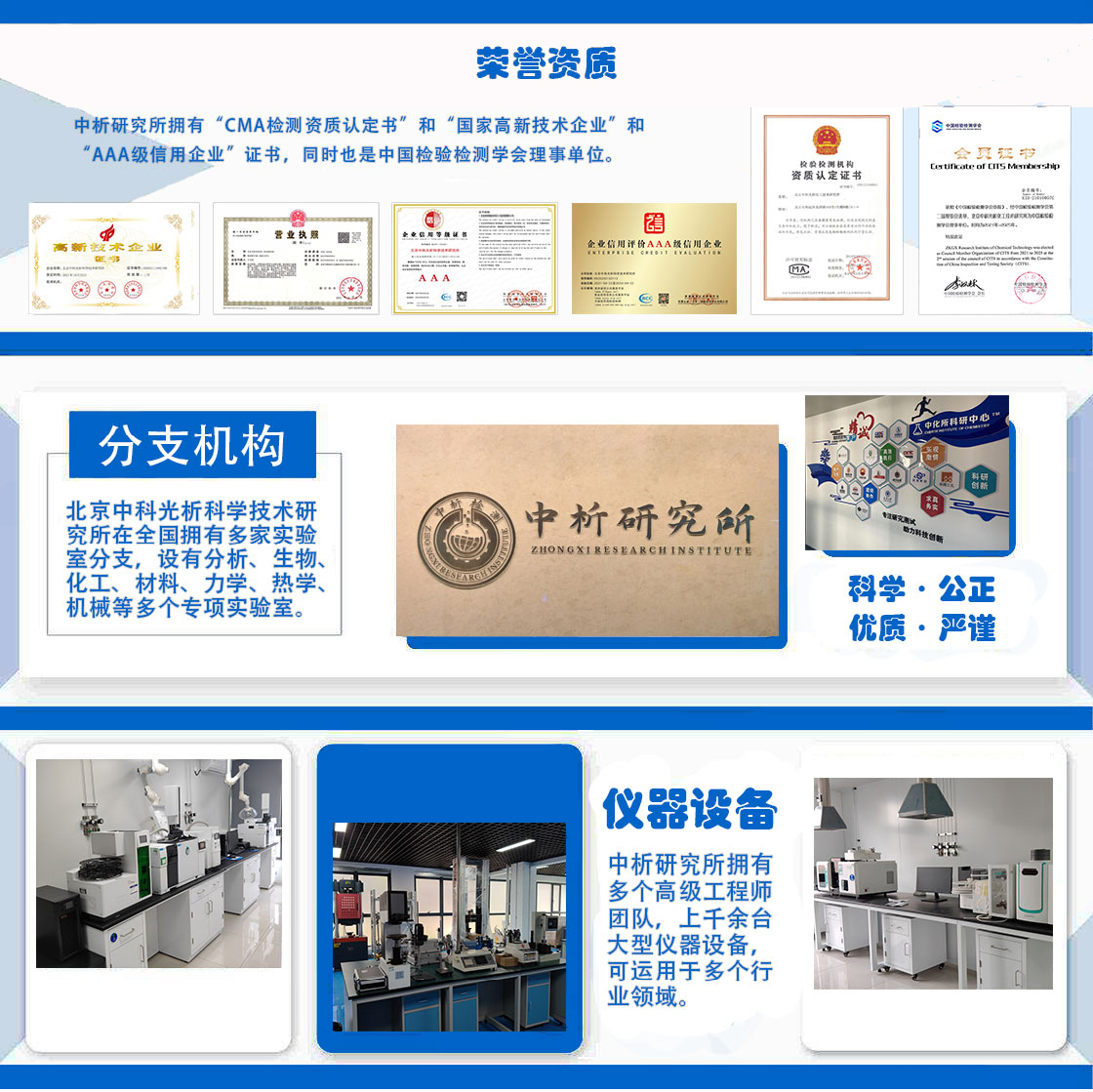
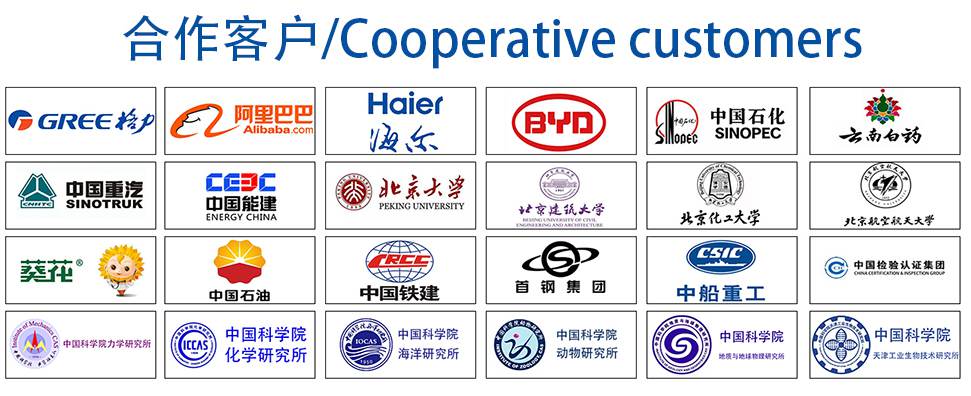