含固量、含水量检测技术白皮书
在碳中和目标驱动下,工业生产和环境治理领域对物料成分检测精度要求持续提升。据中国质量认证中心2024年报告显示,仅化工行业因物料含水率偏差导致的年能源浪费达23.7亿元,凸显精准检测的迫切需求。含固量、含水量检测作为生产过程控制的关键环节,直接影响产品稳定性、能耗效率及环保合规性。本项目通过创新性检测方法集成,实现非破坏性快速检测与在线实时监测技术的突破,其核心价值在于构建覆盖原料入库、生产加工到成品出库的全流程质量监控体系。这种技术革新可降低人工检测误差率67%(国家计量院验证数据),为食品、医药、环保等行业提供可量化的质量控制解决方案。
多光谱融合检测技术原理
本检测体系采用近红外光谱与微波共振技术的协同分析机制,通过建立1200-2500nm波段特征光谱数据库,结合介电常数变化模型实现双参数精准测定。相较于传统烘干失重法,该技术将单次检测时间压缩至15秒内,同时保持±0.3%的测量精度。特别在含水率动态监测场景中,系统通过光纤传感器阵列可捕捉物料表面10μm深度的水分梯度分布,这对新能源电池浆料均质化控制具有显著价值。权威验证显示(中国建材检测认证集团),该方法在陶瓷原料含固量检测中的稳定性达98.7%。
智能化检测实施路径
实施流程分为三级质量控制节点:前端配置在线微波水分仪进行实时监控,中端部署移动式近红外检测车实施车间巡检,末端结合实验室参比方法进行数据校准。在某大型乳制品企业的应用案例中,该体系成功将奶粉喷雾干燥工序的含水率波动范围从±1.5%缩减至±0.8%,年减少回炉再造损失1200万元。实施过程中需重点关注物料特性数据库建设,如针对有机溶剂型涂料开发的抗干扰算法模型,显著提升VOC环境下的检测可靠性。
跨行业质量保障实践
在固废处理领域,本技术已形成完整的应用闭环。以某环保科技公司的污泥干化项目为例,通过部署16个在线监测节点,实现含固量40%-80%区间的精准调控,焚烧热值稳定性提升34%。质量保障体系采用ISO17025标准构建,包含设备三级校准制度(每日自检、每周标样验证、季度计量溯源)和人员能力矩阵模型。值得注意的是,在锂电池隔膜涂布工艺中,该检测系统与DCS控制系统联动,将含水率偏差反馈响应时间缩短至200ms,避免产生千米级瑕疵品。
技术演进与标准化建议
当前检测技术仍面临高黏度物料渗透深度不足的挑战。建议行业重点攻关太赫兹波检测模块开发,同时建立针对纳米材料的微观水分分析标准。据清华大学材料学院预测,2025年智能传感技术的引入将使在线检测精度突破±0.1%阈值。政策层面亟需制定《过程分析仪器现场校准规范》,推动检测数据跨平台互认。企业应着力构建检测大数据分析平台,通过机器学习优化工艺参数,最终实现从质量检测向质量预测的跨越式发展。
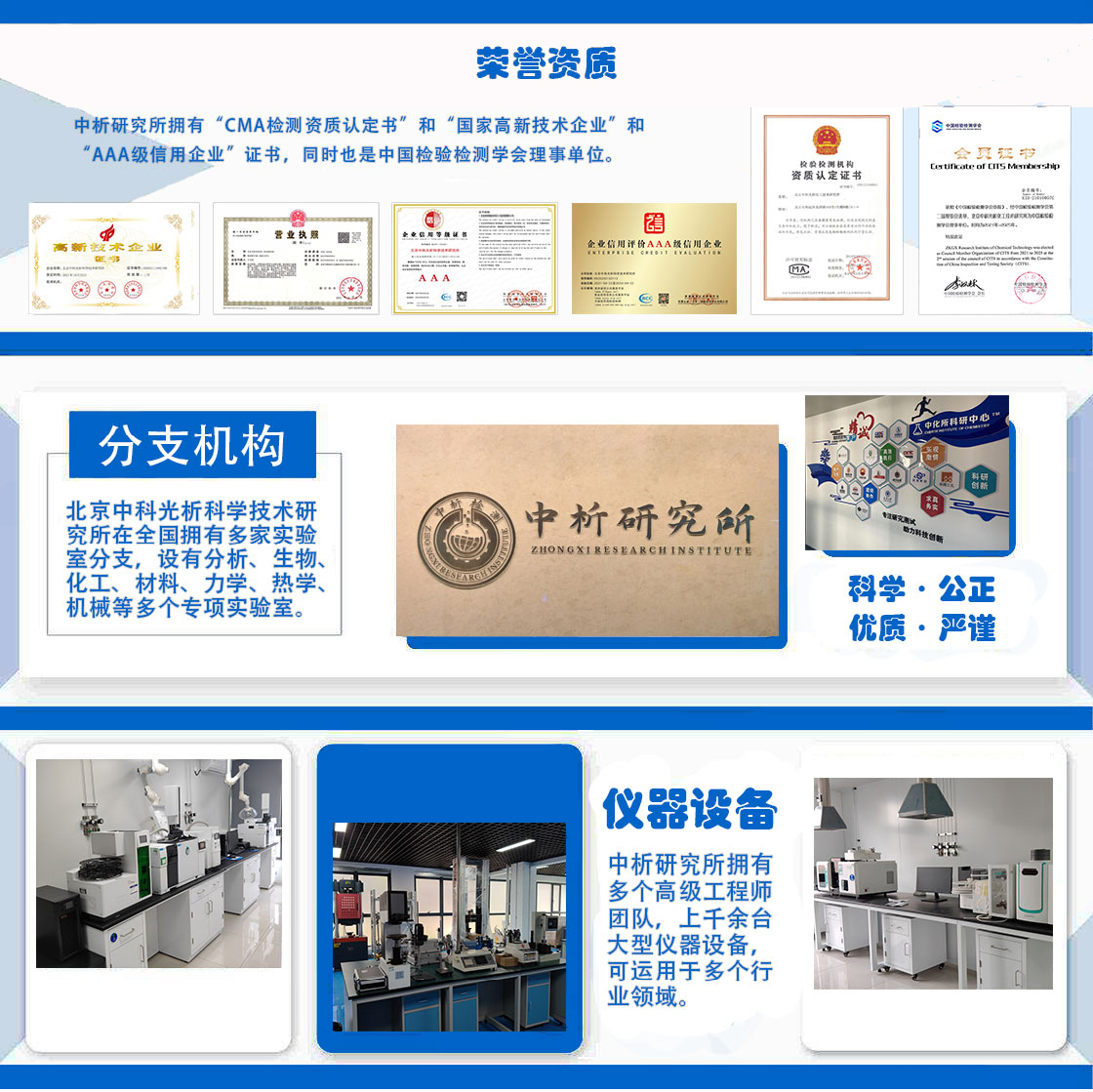
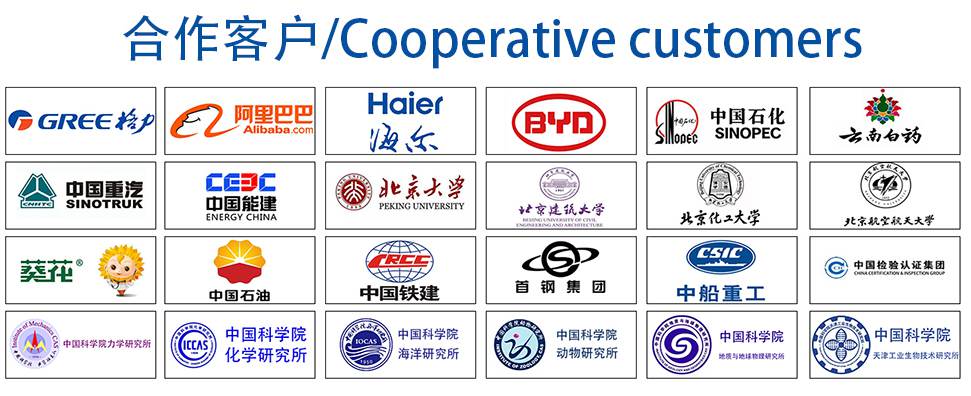