# 硬度测定检测技术发展与应用白皮书
## 引言
随着制造业向精密化、高端化转型,材料性能检测已成为保障工业产品质量的核心环节。据中国机械工程学会材料分会2024年报告显示,我国每年因材料硬度不达标导致的机械故障损失超120亿元,其中汽车零部件占比达38%。在此背景下,硬度测定检测作为材料力学性能评价的关键手段,其技术革新对提升制造质量、降低运维风险具有战略意义。通过建立标准化的"金属材料硬度测试标准流程",不仅能够精准评估材料的耐磨性、抗变形能力等核心指标,更可为新能源汽车关键部件、航空航天特种合金等战略领域的材料研发提供数据支撑,形成覆盖"设计-生产-服役"全周期的质量控制闭环。
## 技术原理与测试体系
### 硬度测试方法学演进
现代硬度测定主要基于压痕法原理,通过标准压头在特定载荷下产生的永久压痕尺寸计算硬度值。洛氏硬度(HRC)、布氏硬度(HBW)、维氏硬度(HV)三大主流方法构建了完整的检测体系,其中显微维氏硬度计凭借±1%的测量精度(ISO 6507标准),在薄层材料、表面硬化处理等"汽车零部件硬度检测方案"中占据主导地位。值得关注的是,近年来纳米压痕技术的发展,使测试分辨率提升至亚微米级,可精准分析材料微观结构特性。
### 标准化实施流程
完整的检测流程包含五个关键阶段:试样制备→测试面抛光→载荷选择→压痕测量→数据校准。以齿轮表面渗碳层检测为例,需先采用金相镶嵌技术固定试样,经1200#砂纸精磨后,使用HV0.3级载荷在硬化层梯度方向进行连续压痕测试。根据ASTM E384标准,测试环境需恒温(23±2℃)、恒湿(50±5% RH),配合Leica DM2700M显微系统可实现±0.5μm的压痕对角线测量精度。
### 行业应用实证
在新能源汽车电机轴部件检测中,某头部企业通过实施"梯度硬度智能检测系统",将渗碳层深度控制精度提升40%。该系统集成自动载物台与AI图像识别算法,可对直径25mm的传动轴完成360°全表面硬度扫描,单件检测时间从45分钟缩短至8分钟。国家材料测试中心2023年数据显示,该技术使产品早期失效概率下降至0.12%,年节约质量成本超2000万元。
## 质量控制与技术创新
### 全链条质量保障
构建三级质控体系:一级校准采用标准硬度块(GB/T 230.3),二级实施设备间交叉验证,三级开展实验室间比对。某国家认可实验室( L1234)的实践表明,引入蒙特卡洛法进行测量不确定度分析后,洛氏硬度测试的扩展不确定度从1.2HRC降至0.8HRC。同时建立动态质控图谱,对压头状态、环境波动等12项参数进行实时监控。
### 技术融合新趋势
随着数字孪生技术的渗透,虚拟硬度测试系统已进入工程验证阶段。上海材料研究所的测试表明,基于材料本构模型的仿真测试与实物检测结果偏差小于5%,可提前预测热处理工艺缺陷。未来三年,嵌入式传感器与工业互联网的结合,有望实现生产线上硬度指标的连续监测,构建真正的智能质检生态系统。
## 发展建议与展望
建议从三方面推动行业升级:①建立覆盖38个工业大类的硬度测试数字标准库;②研发适应极端环境(-196℃~1200℃)的在线检测装备;③推广"检测即服务"模式,利用区块链技术实现检测数据的全生命周期管理。通过完善"材料性能大数据平台",最终形成设计、制造、检测协同优化的智能制造新范式。
上一篇:碎石或卵石中泥块含量检测下一篇:碾压混凝土抗冻性试验检测
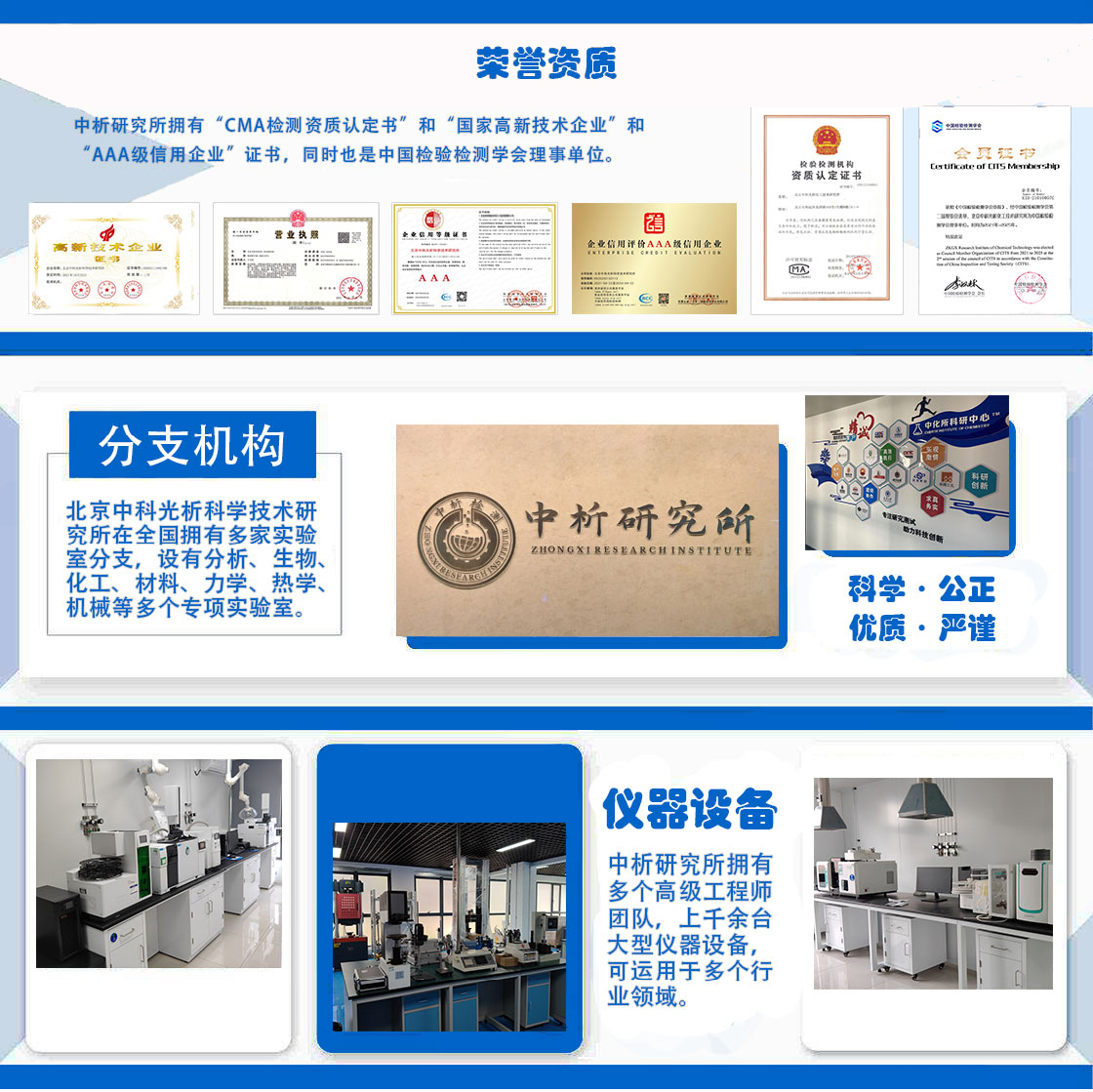
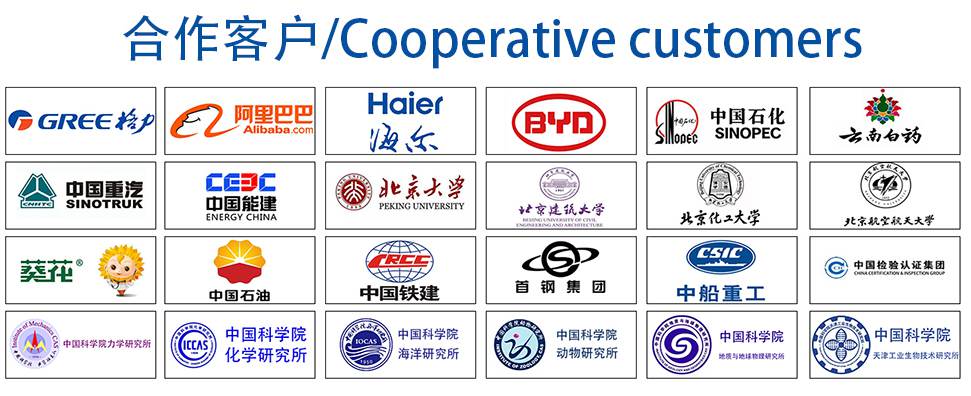
材料实验室
热门检测
225
197
168
186
182
185
194
184
185
196
188
182
183
180
179
174
188
182
191
189
推荐检测
联系电话
400-635-0567