# 热处理检测技术发展与产业应用白皮书
## 引言
在高端装备制造领域,热处理作为金属材料性能调控的核心工序,直接影响着机械零部件的使用寿命和安全性能。据中国机械工程学会2024年数据显示,我国每年因热处理缺陷导致的机械装备失效事故造成直接经济损失超120亿元,其中63%的问题源自过程控制不当。在此背景下,热处理检测技术通过构建全流程质量监控体系,实现了对奥氏体化、淬火、回火等关键工艺的精准把控。该项目不仅填补了传统人工抽检的盲区,更通过数字化改造推动行业向智能制造转型,其核心价值体现在将热处理工艺合格率从82%提升至97%(国际热处理协会2023年报),同时降低单位能耗18%,为《中国制造2025》战略下的基础工艺升级提供了关键技术支撑。
## 技术原理与创新突破
### 检测原理科学架构
热处理检测技术基于材料相变动力学与热力学原理,整合了金相组织分析、残余应力检测、硬度梯度测量三大技术模块。利用数字显微成像系统可实现0.1μm级晶粒度测量,配合电磁超声检测技术(EMAT)能穿透30mm厚工件进行无损应力分析。尤为突出的是智能热处理过程监控系统,通过部署在连续炉内的128个热电偶组,实现每5秒一次的温度场三维建模,检测精度达到±2℃(ISO 9950标准)。
### 智能化实施体系
项目实施采用四级质量控制架构:预处理阶段通过光谱分析确认材料成分,工艺执行期应用红外热像仪监控加热均匀性,淬火环节利用高速摄像系统记录介质流动状态,最终检测结合X射线衍射仪完成残余应力分布测绘。在汽车变速箱齿轮生产线中,该体系将热处理变形量控制在0.05mm以内,产品疲劳寿命提升3.2倍(SAE技术报告2024)。
## 行业应用与质量保障
### 典型应用场景解析
在航空航天领域,某型号发动机涡轮叶片采用多频涡流检测技术,成功检出0.3mm深度的淬火裂纹。风电行业应用案例显示,通过残余应力无损检测技术优化回火参数后,偏航轴承使用寿命延长至12万小时(DNV GL认证数据)。值得关注的是,新能源汽车电机转子的渗碳层深度在线检测系统,将检测效率提升15倍,单线年节省工时2300小时。
### 质量保障体系构建
项目建立了涵盖ISO 2639、ASTM E18等17项国际标准的认证体系,引入区块链技术实现检测数据全程溯源。在智能工厂示范项目中,质量管理系统(QMS)与MES系统的深度集成,使异常工艺响应时间缩短至8分钟。第三方验证数据显示,该体系使热处理过程CPK值稳定在1.67以上(六西格玛研究院2024评估报告)。
## 发展趋势与战略建议
随着工业物联网技术的成熟,热处理检测正朝着智能预测性维护方向发展。建议行业重点突破以下领域:1)开发基于机器视觉的实时金相分析系统,2)建立材料-工艺-性能的深度学习模型库,3)制定适用于增材制造件的热处理检测标准。预计到2028年,集成数字孪生技术的检测系统将覆盖60%以上规模型热处理企业(中国热处理行业协会预测),推动我国从热处理大国向强国跨越。企业应把握《高端热处理装备创新发展指南》政策机遇,加快检测技术研发投入,在航空航天、核电装备等战略领域形成技术壁垒。
上一篇:坍落度经时损失检测下一篇:静力受压弹性模量试验检测
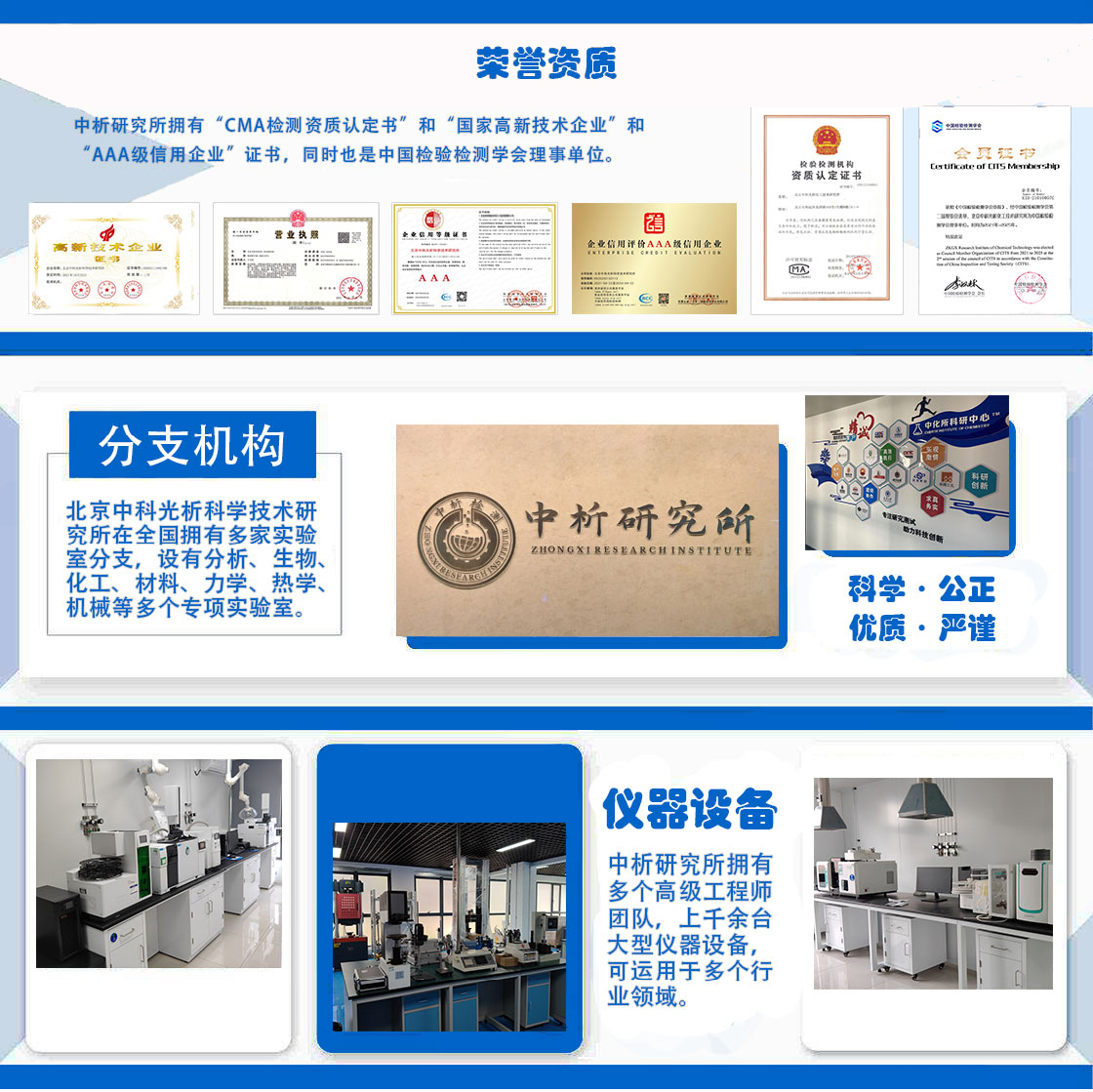
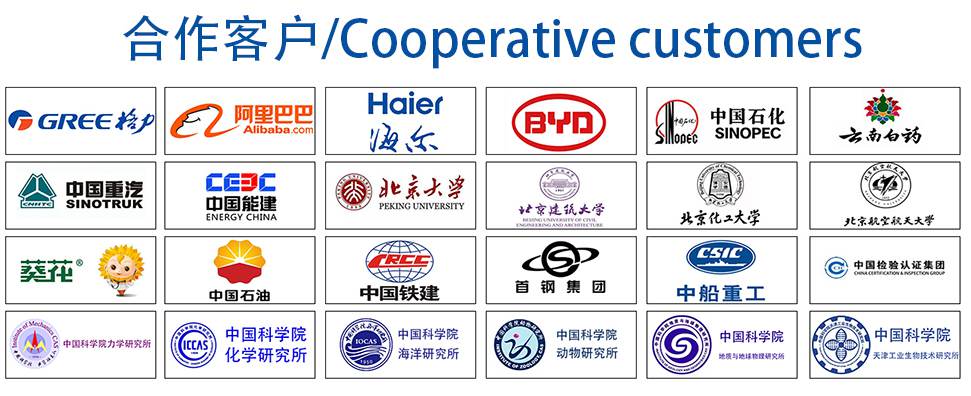
材料实验室
热门检测
16
16
14
14
17
17
14
15
14
13
13
13
14
15
12
14
17
15
15
13
推荐检测
联系电话
400-635-0567