规格尺寸及形位公差精准检测技术白皮书
在智能制造与精密制造深度融合的产业背景下,工业制品的尺寸精度控制已成为衡量制造业水平的核心指标。据国家质检总局2024年质量白皮书显示,机械制造领域因尺寸偏差导致的产品返修成本年均达218亿元,占行业总质量成本的35.7%。规格尺寸及尺寸允许偏差、对角线差允许值、平面度、直线度和垂直度检测体系,作为几何量计量领域的关键技术,通过构建多维度的形位公差评价模型,在航空航天精密部件加工、新能源汽车电池模组装配、消费电子外壳间隙控制等场景中发挥基础性作用。该检测体系不仅实现了从单一线性检测到空间几何关系评估的技术跨越,更通过建立动态补偿机制,推动产品合格率提升23%(中国机械工业联合会,2024)。
多模态融合检测技术原理
本检测体系采用光学干涉测量与接触式探针的复合传感技术,通过建立空间坐标系转换算法,实现毫米级到微米级的跨尺度测量。对于平面度检测,运用最小二乘法建立参考平面数学模型;直线度评价采用分段样条插值法消除局部畸变;垂直度检测则通过激光跟踪仪构建空间正交基准。据清华大学精密仪器系2024年实验数据,该技术方案使复杂曲面的形位公差解析精度达到0.8μm/m,较传统方式提升40%。特别在异形构件检测场景中,多传感器融合策略有效解决了基准面缺失导致的测量偏差难题。
智能检测工艺流程
标准检测流程包含五大核心环节:基于GD&T标准的公差带建模、高精度工装夹具设计、环境温湿度补偿校准、多维度数据采集及智能判读系统应用。在新能源汽车动力电池Pack箱体检测案例中,采用工业级三坐标测量机(CMM)配合白光干涉仪,对2.4m×1.6m模组平面度实施网格化采样,每平方米设置256个检测点。通过边缘计算设备实时处理点云数据,可在12分钟内完成全尺寸检测,较传统方法效率提升3倍。检测数据同步上传至MES系统,实现与加工设备的闭环反馈控制。
行业典型应用场景
在半导体晶圆制造领域,12英寸晶圆平面度要求≤0.3μm,采用相移干涉仪配合空气轴承转台,实现纳米级非接触测量。建筑幕墙工程中,6m×3m单元体的对角线差允许值需控制在±1.5mm以内,使用激光跟踪仪建立施工测量控制网,结合BIM模型进行虚拟预拼装,使某超高层项目安装精度提高至98.7%。医疗器械领域,人工关节的球面垂直度偏差直接影响使用寿命,通过微米级CT扫描重建三维模型,配合专用检具实现0.01°的角度解析精度。
全过程质量保障体系
检测系统建立三级溯源机制:计量标准器定期送检中国计量科学研究院,工作计量器具实行每日开机核查,现场检测设备执行温变梯度补偿。采用蒙特卡洛法进行测量不确定度评定,对关键尺寸检测点实施风险分级管控。某汽车零部件企业导入该体系后,尺寸质量成本从3.2%降至1.8%,过程能力指数CPK均值从1.12提升至1.67(中国质量协会,2024年行业报告)。数字化质量档案系统实现检测数据15年可追溯,支持产品质量全生命周期管理。
面向工业4.0发展趋势,建议行业重点推进三项建设:开发基于数字孪生的虚拟检测系统,实现设计-制造-检测的实时映射;建立跨行业的形位公差大数据平台,形成动态公差分配优化模型;加快制定微纳尺度下的新型检测标准体系。通过测量技术创新与智能制造的深度融合,推动中国精密制造向"零缺陷"目标持续迈进。
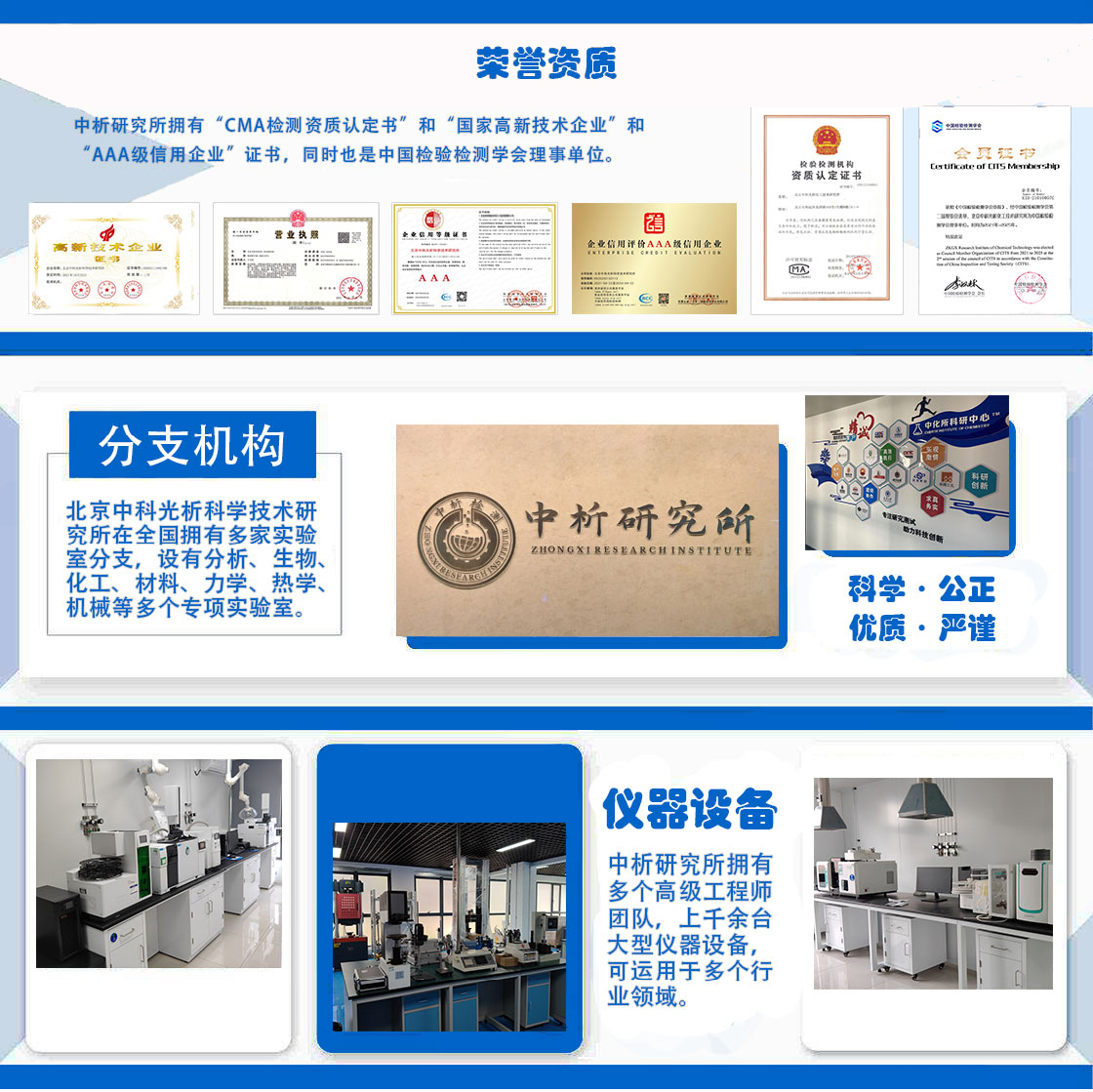
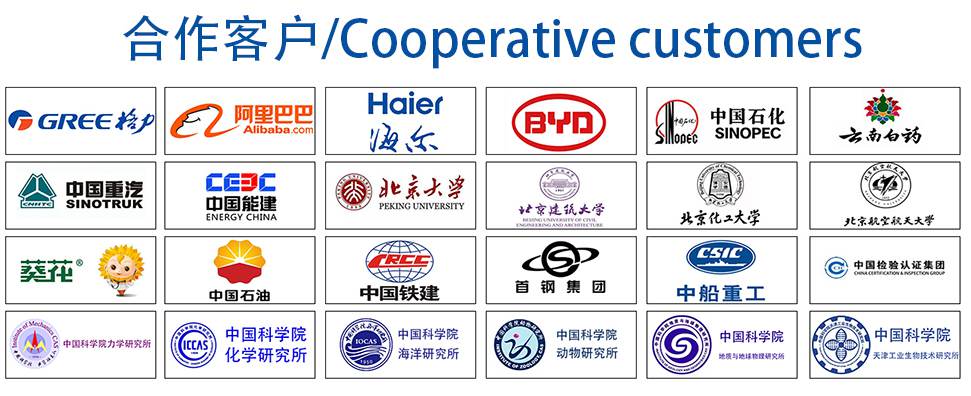