变位系数检测的核心项目与关键技术
一、变位系数的核心检测项目
-
- 检测内容:模数(�m)、齿数(�z)、压力角(�α)、分度圆直径等。
- 意义:计算理论变位系数的基础,确保后续检测结果的可靠性。
- 工具:卡尺、光学投影仪、齿轮参数分析仪。
-
- 关键指标:分度圆齿厚(�s)、固定弦齿厚或公法线长度(��Wk)。
- 方法:
- 使用齿厚千分尺直接测量分度圆齿厚;
- 通过公法线千分尺测量跨齿数�k的公法线长度,反推变位系数。
- 公式: ��=�cos�[(�−0.5)�+�⋅inv�]+2��sin�Wk=mcosα[(k−0.5)π+z⋅invα]+2xmsinα 其中�x为变位系数。
-
- 原理:通过测量齿轮两相对齿槽间标准量棒的间距,间接计算变位系数。
- 步骤:
- 选择适配量棒直径��dp;
- 测量两量棒外端距离�M;
- 结合齿数、压力角计算实际变位系数。
- 适用性:适用于内、外齿轮,精度可达±0.005 mm。
-
- 接触斑点分析:在啮合试验机上涂色运转,观察齿面接触区域形状和面积,判断变位系数是否合理。
- 中心距偏差检测:实际装配中心距与理论值(�=�(�1+�2)2+�1+�2a=2m(z1+z2)+x1+x2)的差异反映变位系数的匹配性。
-
- 检测意义:变位系数影响齿顶高和齿根高,进而改变齿顶圆(��=�+2�(1+�)da=d+2m(1+x))和齿根圆(��=�−2�(1.25−�)df=d−2m(1.25−x))的尺寸。
- 工具:三坐标测量机(CMM)或激光扫描仪。
二、检测设备与关键技术
-
- 采用数控系统,自动完成齿廓、齿向、齿距及变位系数的全参数分析,精度达ISO 1328标准1级。
-
- 通过放大齿形轮廓,对比理论设计图,快速识别变位导致的齿形畸变。
-
- 对未知变位系数的齿轮进行三维建模,通过软件拟合参数(如KISSsoft、GearTrax),反推出实际变位系数。
三、数据处理与标准对比
- 计算修正:考虑温度、材料变形等因素,对实测数据进行补偿。
- 标准依据:
- ISO 21771:2007(齿轮几何参数定义与检测);
- AGMA 915-1-A02(变位齿轮设计指南);
- GB/T 10095(中国齿轮精度标准)。
四、
上一篇:铜箔电阻检测下一篇:在温度和湿度条件下卡尺寸的稳定性和翘曲检测
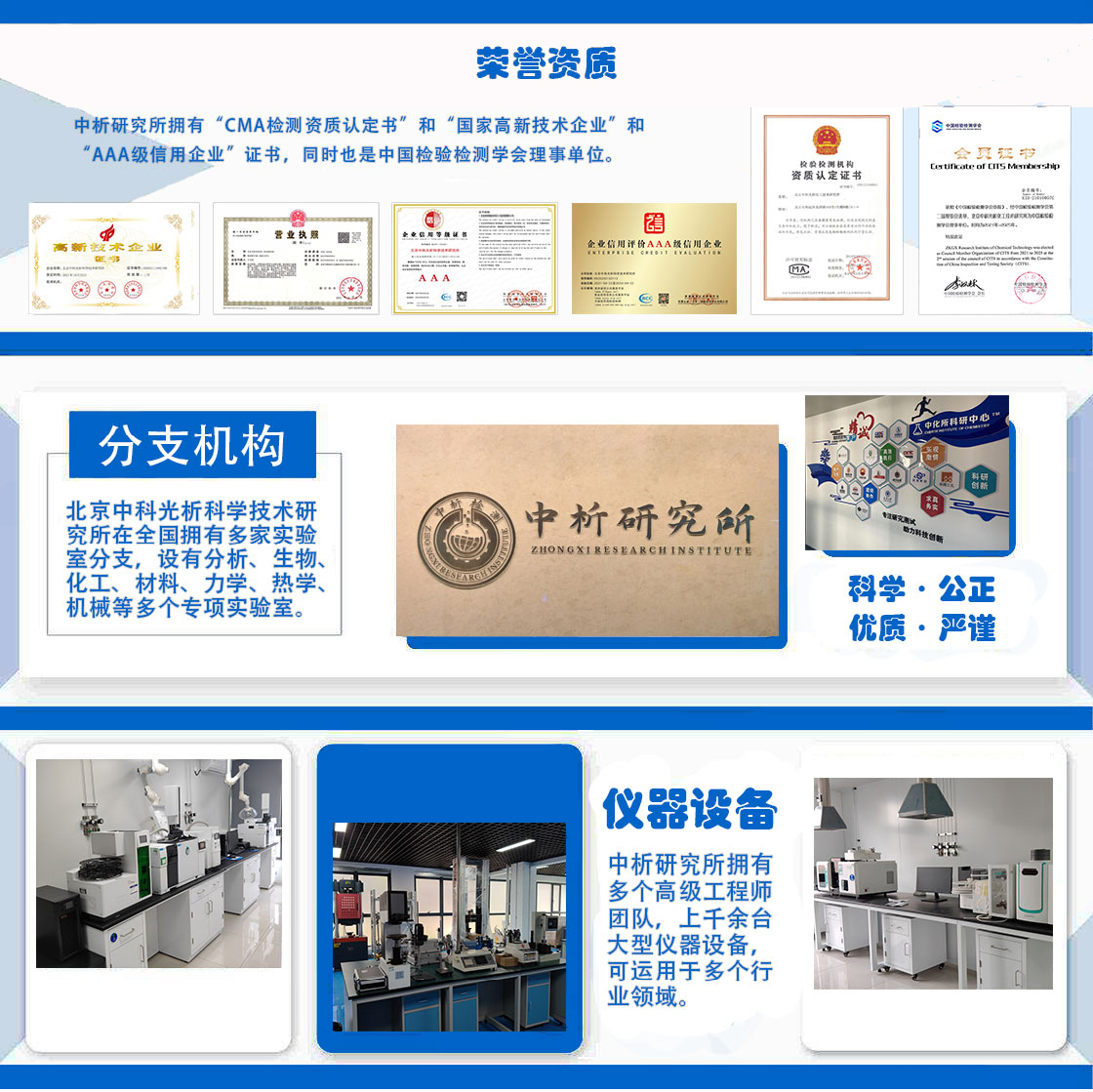
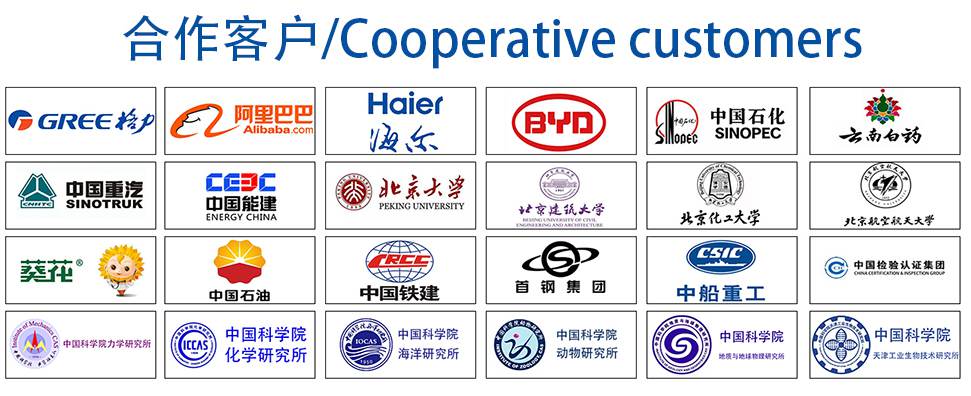
材料实验室
热门检测
276
233
208
217
215
220
230
223
233
233
220
219
222
219
213
210
227
212
224
218
推荐检测
联系电话
400-635-0567