温度循环试验检测:核心检测项目详解
一、温度循环试验的核心检测项目
1. 温度适应性测试
- 目的:验证产品在温度梯度变化下的功能稳定性。
- 方法:
- 设定温度范围(如-40℃至+125℃),以指定速率(如10℃/min)进行高低温循环。
- 记录产品在极端温度点及过渡阶段的性能参数(如电压输出、信号传输)。
- 判定标准:
- 功能参数偏差≤±5%(如精密传感器);
- 无死机或逻辑错误(如车载控制器)。
2. 材料热膨胀系数(CTE)匹配性
- 问题焦点:多层材料(如PCB基板与芯片封装)因CTE差异导致分层、裂纹。
- 测试方法:
- 显微观察(SEM/CT扫描)检测界面结构;
- 结合热机械分析仪(TMA)量化CTE差异。
- 典型案例:某功率模块因陶瓷基板与铜层CTE不匹配,经500次循环后出现焊点断裂。
3. 密闭性测试(防潮/防尘)
- 适用产品:户外设备、汽车电子外壳。
- 测试流程:
- 温度循环后立即进行IP67等级测试;
- 使用氦质谱检漏法检测微米级缝隙。
- 失效表现:内部结露导致电路短路(如5G基站射频单元)。
4. 机械结构稳定性
- 关键指标:
- 螺丝扭矩衰减率(如车载ECU安装点);
- 塑料壳体形变(卡扣结合力下降≥30%判为失效)。
- 加速测试方案:在高温阶段施加振动载荷(复合应力试验)。
5. 焊点/连接器可靠性
- 检测技术:
- 扫描声学显微镜(SAM)检测BGA焊点空洞;
- 导通电阻监测(连接器接触电阻变化率>20%为异常)。
- 行业标准:IPC-9701(电子组件机械应变测试)。
6. 涂层/镀层附着力
- 测试方法:
- 交叉划格试验(ASTM D3359);
- 胶带剥离后涂层脱落面积<5%为合格。
- 典型失效:盐雾+温度循环导致铝合金外壳阳极氧化层剥落。
7. 寿命预测与加速模型
- 模型应用:
- 阿伦尼乌斯公式推算激活能(Ea);
- 科芬-曼森方程关联温度变化幅度与疲劳寿命。
- 示例:某LED驱动器通过1000次循环(-40℃~85℃)等效于10年户外使用寿命。
二、试验参数设计要点
参数 | 典型值 | 影响维度 |
---|---|---|
温度范围 | -65℃~+150℃(军工级) | 材料玻璃化转变温度(Tg) |
循环次数 | 50~1000次 | 疲劳累积损伤效应 |
驻留时间 | 30min~2h(确保热平衡) | 蠕变应力释放程度 |
温变速率 | 5℃/min~15℃/min | 热冲击强度(陡变易导致脆裂) |
三、行业应用差异分析
-
- 重点检测:屏幕LCM模块的胶材黄变、电池充放电性能。
- 测试条件:-20℃~+60℃/300次循环(GB/T 2423.22)。
-
- 焦点问题:IGBT模块的散热基板与DBC层剥离;
- 强化测试:温度循环+功率循环复合试验(AQG 324)。
-
- 特殊要求:真空环境下温循(抑制对流散热);
- 材料级测试:碳纤维复材与钛合金螺栓的热匹配性。
四、失效根因分析流程
- 失效定位:红外热成像锁定过热部件;
- 材料分析:EDS能谱分析腐蚀产物成分;
- 工艺审查:回流焊曲线是否导致焊点微裂纹。
五、标准与规范参考
- 国际标准:IEC 60068-2-14(温循)、MIL-STD-883(军品)
- 国内标准:GB/T 2423.22、GJB 150.5A
- 行业规范:JESD22-A104(电子器件)、SAE J1211(汽车电子)
六、
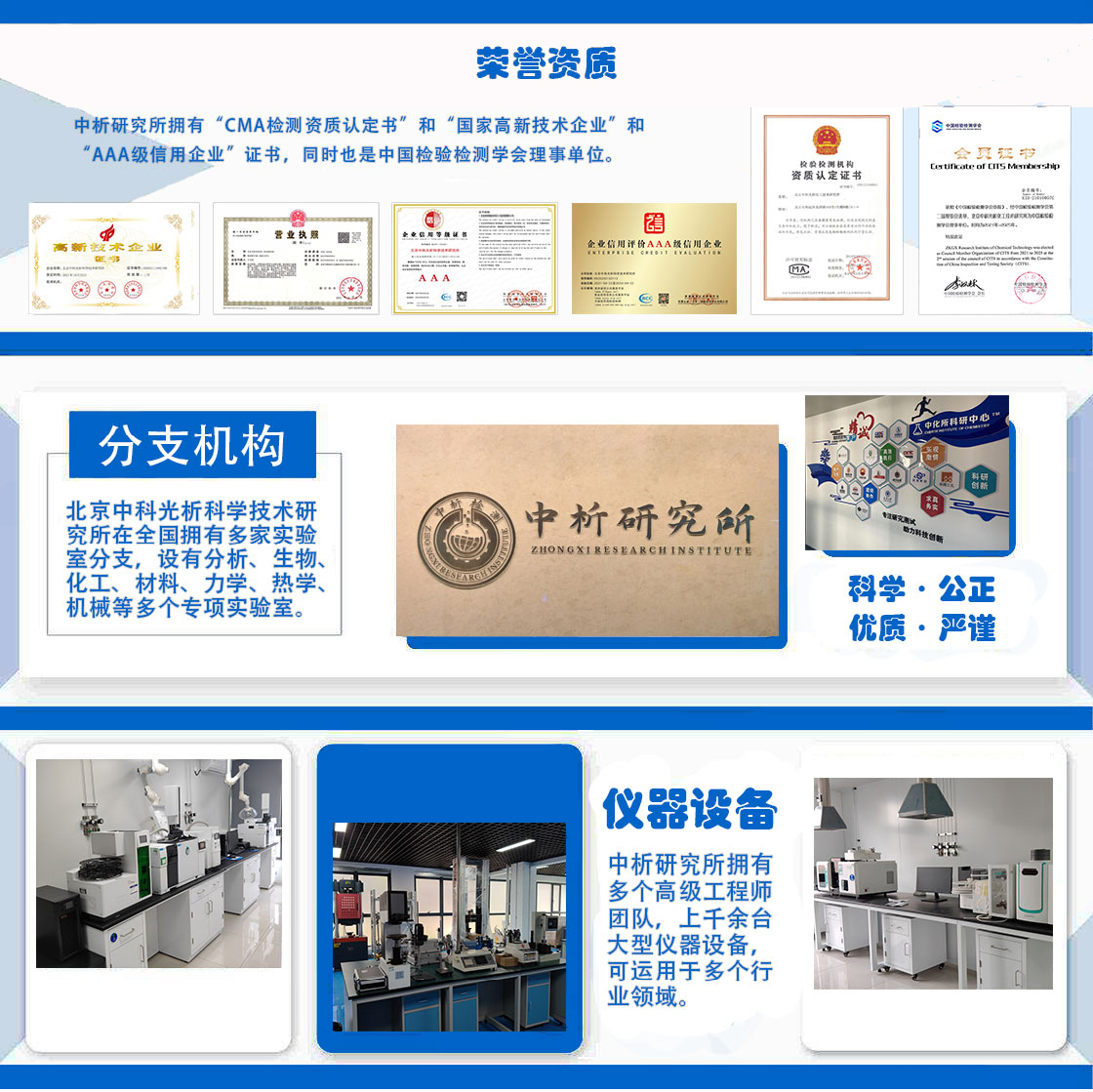
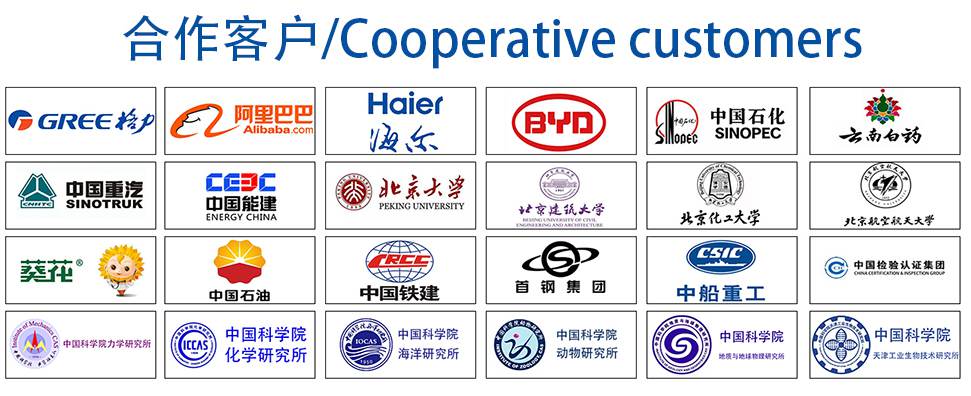
材料实验室
热门检测
254
215
190
203
198
204
210
202
207
217
204
199
204
203
198
195
210
199
209
202
推荐检测
联系电话
400-635-0567