镀覆孔镀层厚度检测:核心检测项目解析
引言
一、镀层厚度检测的意义
- 电气故障:电流承载能力下降,引发过热或断路。
- 机械失效:孔壁镀层裂纹或脱落,导致层间连接失效。
- 环境腐蚀:镀层孔隙率增加,耐腐蚀性降低。
二、主要检测方法
-
- 原理:切割镀覆孔截面,显微镜下直接测量。
- 精度:±0.5μm(行业最高精度)。
- 适用场景:实验室抽样检测、失效分析。
-
- 原理:通过X射线激发镀层元素特征谱线,计算厚度。
- 优势:快速(10秒/点)、支持多点自动扫描。
- 局限性:仅适用于平面区域,无法检测孔内深度方向变化。
-
- 原理:利用镀层电阻与厚度的反比关系推算厚度。
- 应用:适用于铜镀层的快速在线检测,精度±1μm。
-
- 功能:非接触式测量孔壁镀层3D形貌,评估均匀性。
- 分辨率:亚微米级,适合高密度互连(HDI)板检测。
三、核心检测项目详解
-
- 标准要求:IPC-6012 Class 2规定通孔铜厚≥20μm,Class 3(航空航天)要求≥25μm。
- 检测方法:XRF用于批量抽检,金相切片法用于校准验证。
-
- 关键性:确保高电流区域(如电源层过孔)的载流能力。
- 行业案例:汽车ECU板要求最小铜厚≥18μm(IATF 16949)。
-
- 评价指标:孔壁镀层厚度极差(最大值-最小值)≤8μm。
- 检测技术:激光共聚焦显微镜扫描孔壁,生成厚度分布云图。
-
- 方法:热应力试验(288℃浸锡10秒,循环3次),镀层无起泡或剥离。
- 标准依据:JIS C 6481 6.8节结合力测试。
-
- 目的:检测镀层杂质(如有机物残留)对可靠性的影响。
- 仪器:EDS能谱分析镀层元素组成,确保铜纯度≥99.7%。
-
- 硝酸蒸汽试验:将样品暴露在硝酸蒸汽中15分钟,显微镜下计数孔隙(每cm²≤5个孔隙)。
- 电化学法:通过阳极溶解电流曲线推算孔隙密度。
-
- 条件:-55℃~125℃循环500次,镀层电阻变化率≤5%。
- 应用标准:MIL-PRF-31032 4.8.3节环境适应性要求。
四、检测流程优化
- 智能取样策略:基于统计过程控制(SPC),对高纵横比(>8:1)孔位增加检测频次。
- 自动化检测系统:集成XRF与AOI(自动光学检测),实现100%关键孔位扫描。
- 数据管理:MES系统实时记录厚度数据,AI算法预测镀液寿命。
五、行业应用差异
-
- 高频信号完整性:要求镀层表面粗糙度Ra≤1.2μm(减少趋肤效应损耗)。
- 检测技术:白光干涉仪测量孔壁粗糙度。
-
- 极端环境适应:镀层需通过48小时盐雾试验(ASTM B117)。
- 材料升级:采用化学镀镍钯金(ENEPIG)工艺,金层厚度检测精度需达0.05μm。
-
- 动态弯曲要求:镀层延展性检测(ASTM E8标准,延伸率≥15%)。
- 微孔检测:聚焦离子束(FIB)切片分析20μm以下微孔镀层。
六、前沿技术趋势
- 太赫兹波检测:非接触式穿透检测多层板内部镀层缺陷。
- 机器学习模型:基于历史数据预测镀层失效模式,实现预测性维护。
- 纳米压痕技术:评估镀层微观力学性能(硬度、弹性模量)。
上一篇:双极型电路传输时间检测下一篇:物理特性检测
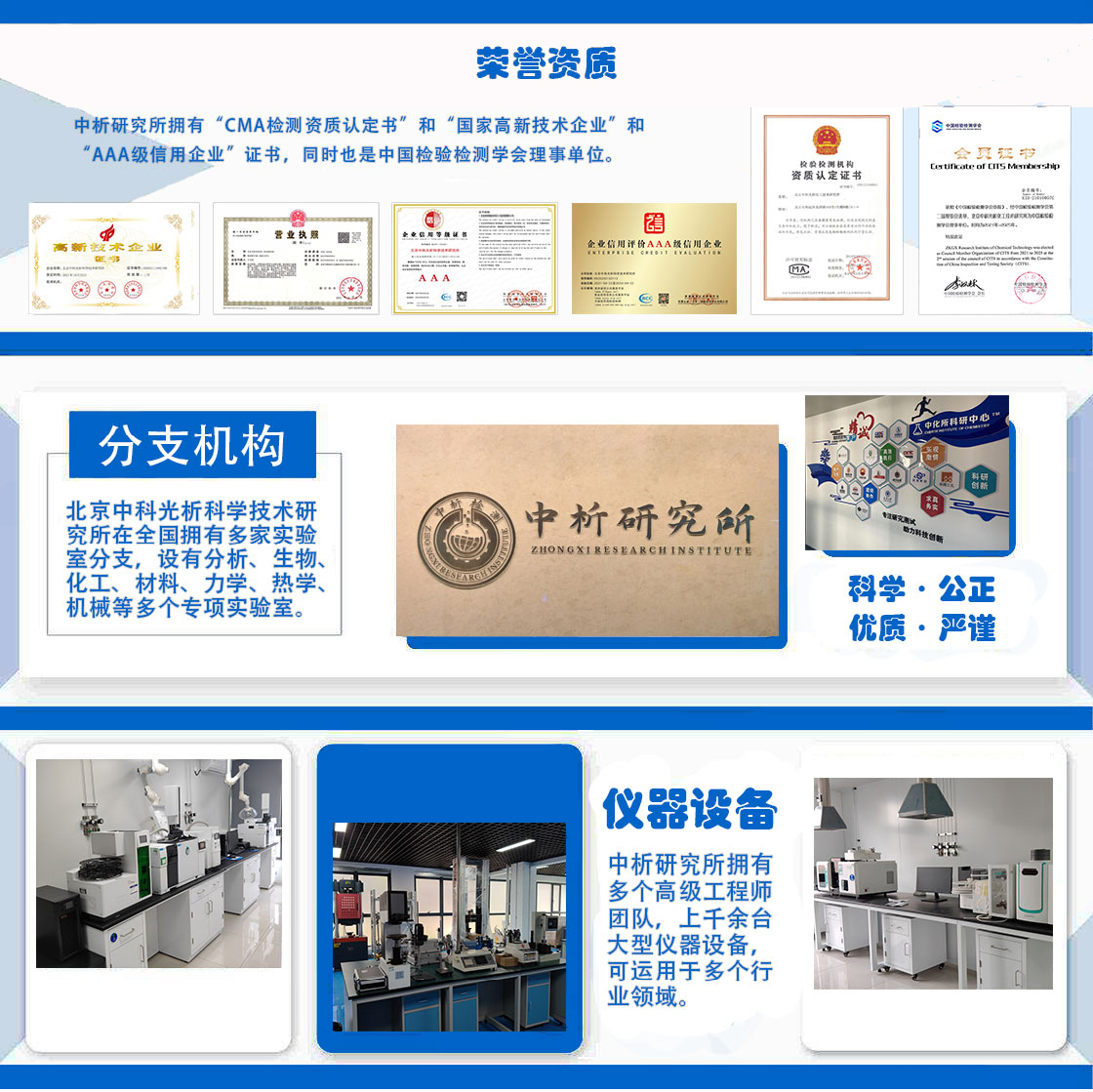
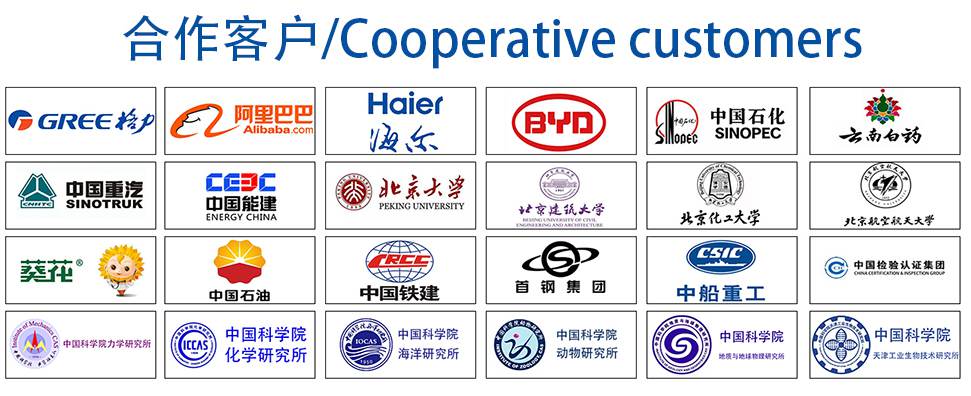
材料实验室
热门检测
254
215
190
203
197
204
210
202
207
217
203
199
203
203
197
195
210
199
209
202
推荐检测
联系电话
400-635-0567