标志耐溶剂检测:关键项目与方法解析
一、检测目的
二、核心检测项目
1. 溶剂擦拭测试
- 测试方法:使用特定溶剂(如异丙醇、丙酮、乙醇)浸润无尘布,以固定压力(通常200-500g/cm²)和频率(如10次/分钟)擦拭标志表面。
- 评估指标:
- 擦拭次数:标志开始脱落或模糊时的最少擦拭次数。
- 色差变化:使用色差仪(如ΔE值)量化颜色变化,ΔE>1.5通常视为明显差异。
2. 浸泡测试
- 测试方法:将标志完全浸入溶剂(如汽油、机油、化学清洗剂)中,设置不同温度(常温至80℃)和时间(1-24小时)。
- 评估指标:
- 附着力:浸泡后标志是否起泡、翘边或剥离。
- 颜色稳定性:肉眼观察褪色或渗透现象。
3. 附着力测试(划格法)
- 测试方法:按标准(如ISO 2409)在标志表面划出1mm×1mm网格,使用胶带粘贴后快速剥离。
- 评估标准:
- 等级0:无脱落(优秀);
- 等级5:超过65%区域脱落(不合格)。
4. 耐化学试剂综合测试
- 试剂类型:涵盖酸性(pH=2-5)、碱性(pH=9-12)、有机溶剂(二甲苯、乙酸乙酯)等。
- 测试流程:滴加试剂至标志表面,静置规定时间后冲洗并干燥,观察外观变化。
5. 耐磨性联合测试
- 方法:结合溶剂擦拭与机械摩擦(如Taber耐磨仪),模拟实际使用中的双重损耗。
- 判定依据:标志完整性是否满足行业标准(如包装印刷需耐受50次以上擦拭)。
三、检测标准与规范
- 国际标准:
- ISO 15790:印刷品耐溶剂性测试方法;
- ASTM D5402:涂层耐液体试剂评估标准。
- 行业特定标准:
- 汽车行业:SAE J2527(耐油性测试);
- 食品包装:FDA 21 CFR 对食品级溶剂的要求。
四、应用领域与案例
- 电子电器:设备标签需耐受酒精擦拭(如手机屏幕标签)。
- 汽车工业:引擎部件标识抗机油腐蚀测试。
- 医药包装:药品瓶身印刷需通过乙醇浸泡验证。
- 户外设备:耐候性标志需同时抵抗紫外线及雨水溶剂侵蚀。
五、检测意义与趋势
- 质量管控:避免因标志失效引发的产品召回风险。
- 环保要求:推动水性溶剂替代传统有机溶剂,检测项目随之调整。
- 技术创新:激光雕刻、UV固化油墨等新工艺需定制化检测方案。
上一篇:输出阻抗检测下一篇:双极型电路传输时间检测
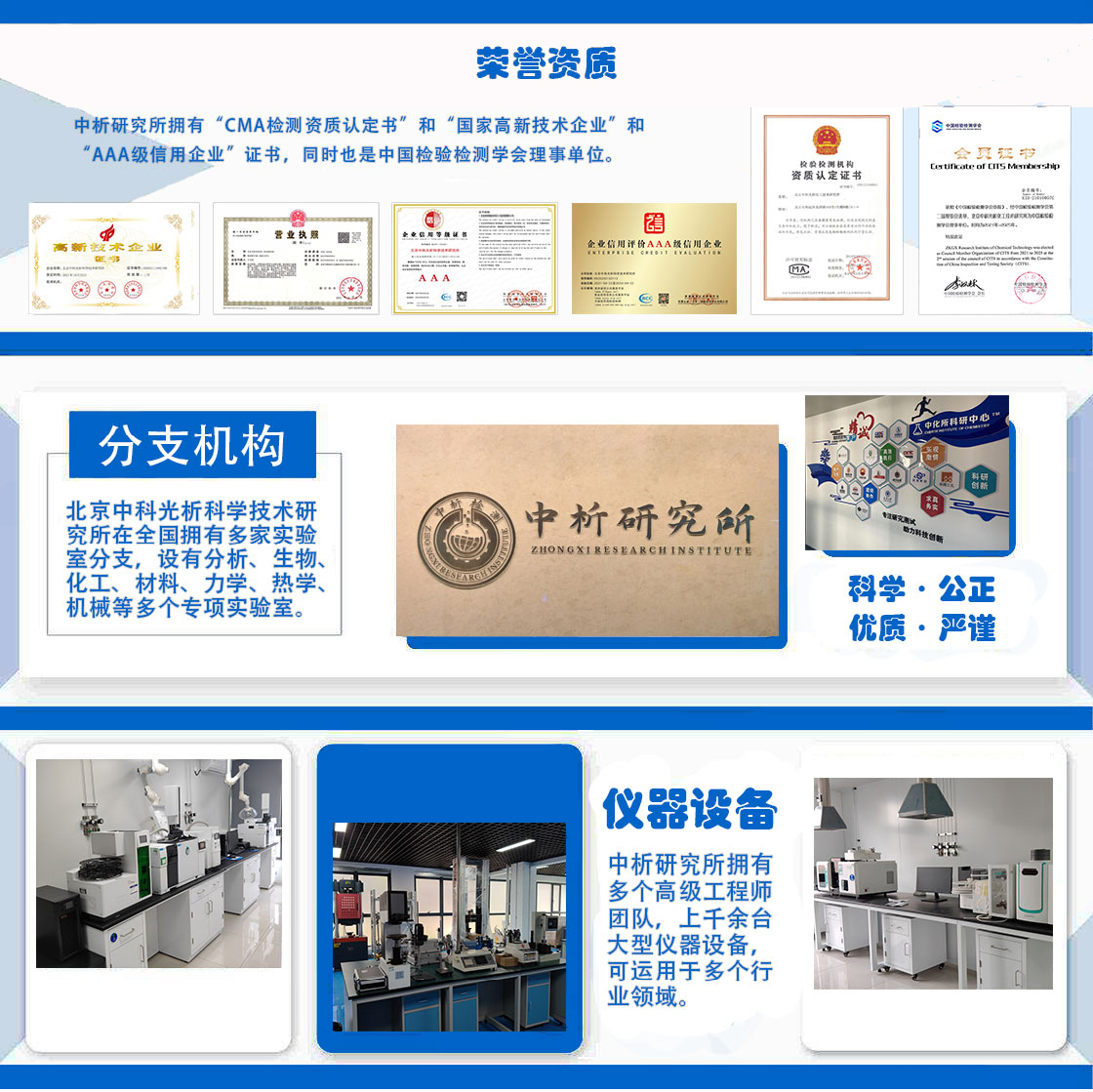
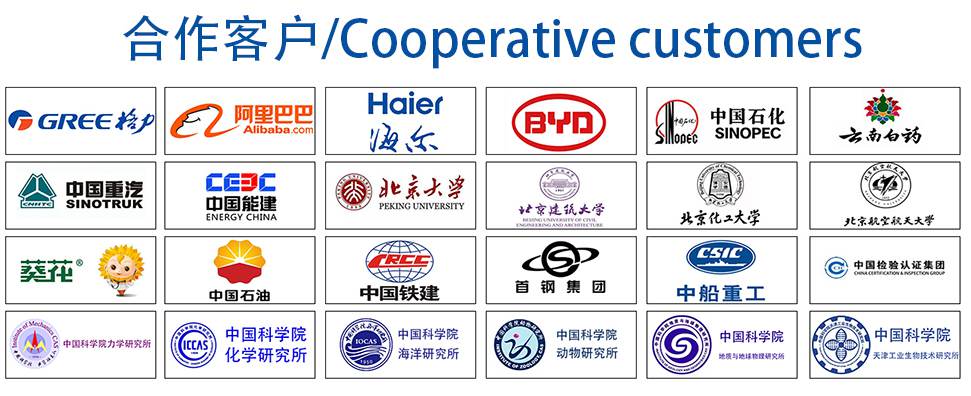
材料实验室
热门检测
254
215
190
203
197
204
210
202
207
217
203
199
203
203
197
195
210
199
209
202
推荐检测
联系电话
400-635-0567