漏极电流检测技术及其核心检测项目详解
一、漏极电流检测的核心意义
- 器件性能评估:验证MOSFET是否符合设计规格;
- 故障诊断:识别过流、短路等异常状态;
- 系统保护:触发过流保护机制,防止器件烧毁;
- 能效优化:动态调整驱动策略,降低功耗。
二、核心检测项目及技术细节
1. 静态漏极电流测试(DC ��ID)
- 目的:测量器件在稳态工作条件下的漏极电流。
- 方法:
- 施加固定栅源电压(���VGS)和漏源电压(���VDS),用万用表或源测量单元(SMU)直接读取电流值。
- 典型测试条件:���=10�VGS=10V,���=5�VDS=5V。
- 关键参数:
- 阈值电压(��ℎVth):��ID达到指定值(如250μA)时的���VGS。
- 导通电阻(���(��)RDS(on)):通过�=���/��R=VDS/ID计算。
- 应用场景:器件选型、批次一致性检验。
2. 动态漏极电流测试(瞬态响应)
- 目的:分析开关过程中的电流变化特性(如上升/下降时间、峰值电流)。
- 方法:
- 双脉冲测试(DPT):通过脉冲信号驱动MOSFET,配合电流探头(Rogowski线圈/霍尔传感器)和示波器捕捉瞬态波形。
- 短路测试:强制器件进入短路状态,检测��ID峰值及持续时间。
- 关键指标:
- 开关损耗:通过��ID-���VDS波形积分计算;
- 反向恢复电荷(���Qrr):体二极管关断时的反向电流积分。
- 工具:高带宽示波器(≥100MHz)、电流传感器、动态参数测试仪。
3. 过流保护阈值测试
- 目的:验证保护电路(如DESAT检测)的响应速度和精度。
- 方法:
- 逐步增加负载电流,观察保护电路触发时的��ID值;
- 模拟短路故障,测试从过流发生到关断的延迟时间。
- 设计要点:
- 去饱和(DESAT)检测:监测���VDS在导通期间的异常上升;
- 滤波时间设置:避免误触发(典型值:1-2μs)。
- 行业标准:AEC-Q101(车规级器件要求故障响应时间<1μs)。
4. 温度特性测试
- 目的:分析漏极电流随温度的变化规律。
- 方法:
- 在高低温箱中,测量不同温度(-40°C至150°C)下的��ID-���VGS曲线;
- 计算温度系数(如���(��)RDS(on)的温漂率)。
- 典型现象:
- ���(��)RDS(on)随温度升高而增大(正温度系数);
- 阈值电压��ℎVth随温度升高而降低。
5. 噪声与干扰抑制测试
- 目的:评估检测电路在噪声环境下的稳定性。
- 挑战:
- 高频开关噪声(如dV/dt耦合)可能导致电流采样失真;
- 共模干扰(如电机驱动中的地弹噪声)。
- 解决方案:
- 差分采样:采用隔离放大器或电流互感器;
- PCB布局优化:缩短检测路径,避免平行走线;
- 滤波设计:添加RC低通滤波器(截止频率匹配信号带宽)。
6. 长期可靠性测试
- 目的:验证器件在持续电流应力下的耐久性。
- 方法:
- HTRB测试(高温反向偏置):在高温下施加额定���VDS,监测��ID漂移;
- 功率循环测试:反复开关器件,统计失效前的循环次数。
- 失效判据:���(��)RDS(on)增幅超过20%或��ID异常波动。
三、检测设备选型指南
检测项目 | 推荐设备 | 精度要求 |
---|---|---|
静态电流测试 | 源测量单元(Keysight B2900A) | ≤0.1% FS |
动态电流测试 | 高频电流探头(Tektronix TCP0030) | 带宽≥100MHz |
温度特性测试 | 高低温试验箱(ESPEC T系列) | 温控精度±0.5°C |
过流保护测试 | 可编程负载(Chroma 63200A) | 响应时间<10μs |
四、典型案例分析
五、未来发展趋势
- 集成化检测方案:SOC芯片内置高精度ADC和温度补偿功能;
- AI驱动的预测性维护:通过��ID趋势分析预判器件寿命;
- 宽禁带器件(GaN/SiC)检测:适应更高开关频率(MHz级)的测试需求。
结语
上一篇:标志检测下一篇:WCDMA数字蜂窝移动通信系统检测
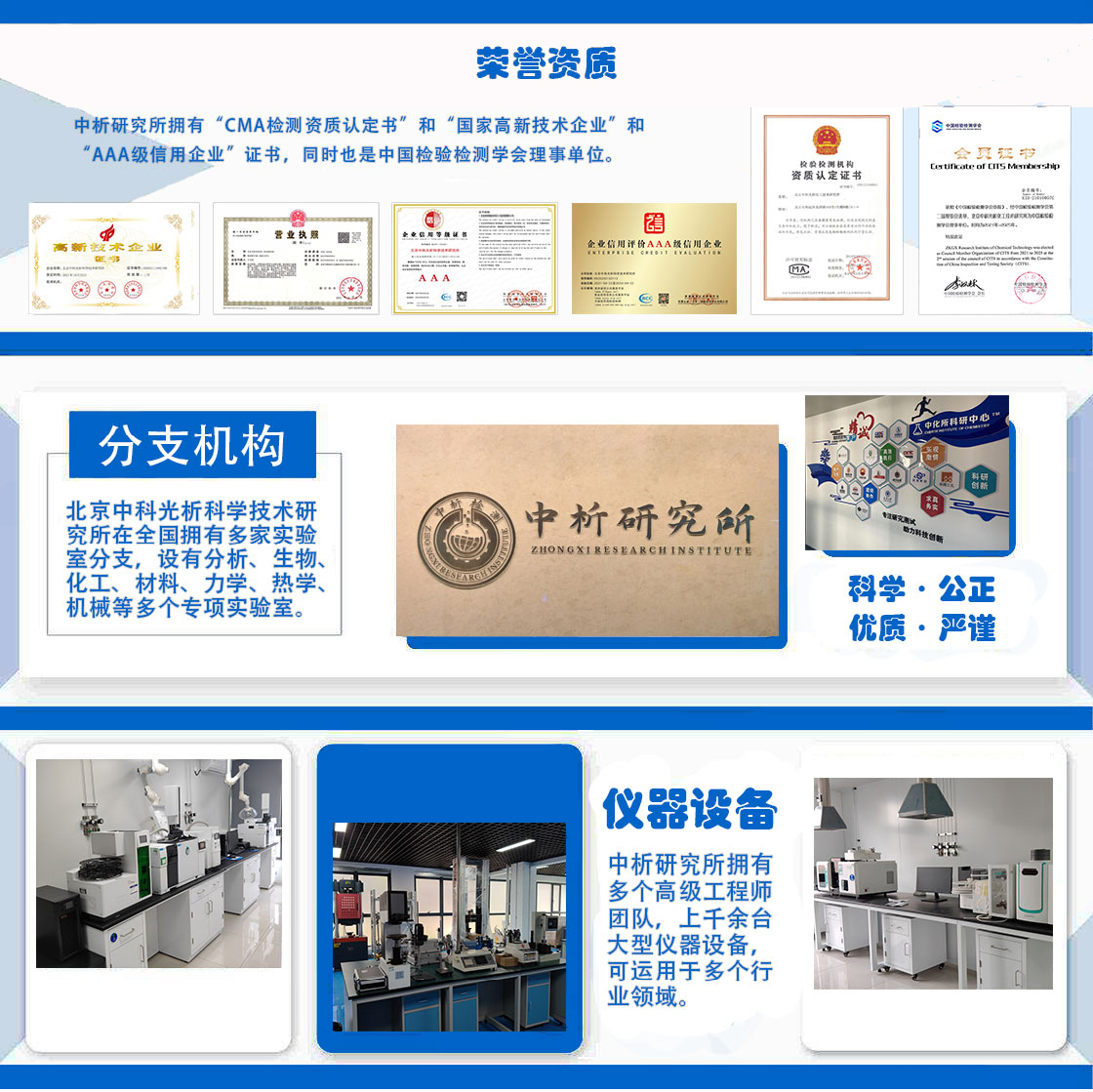
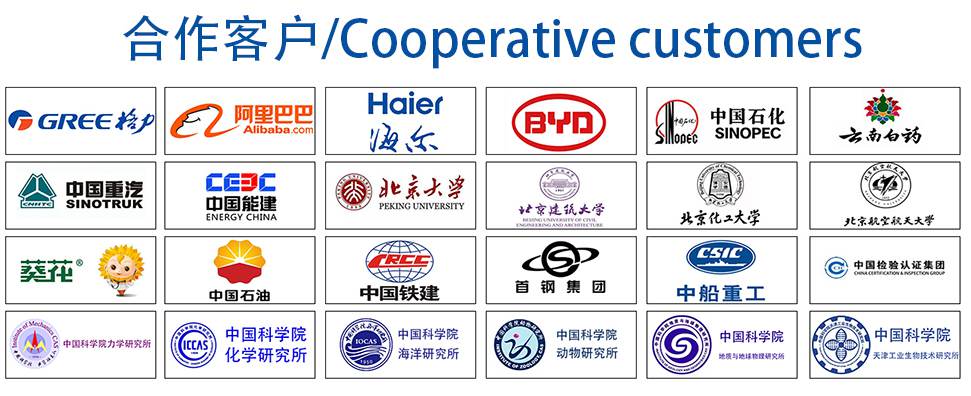
材料实验室
热门检测
253
211
188
202
195
202
207
200
206
214
202
197
195
201
194
192
205
197
206
200
推荐检测
联系电话
400-635-0567